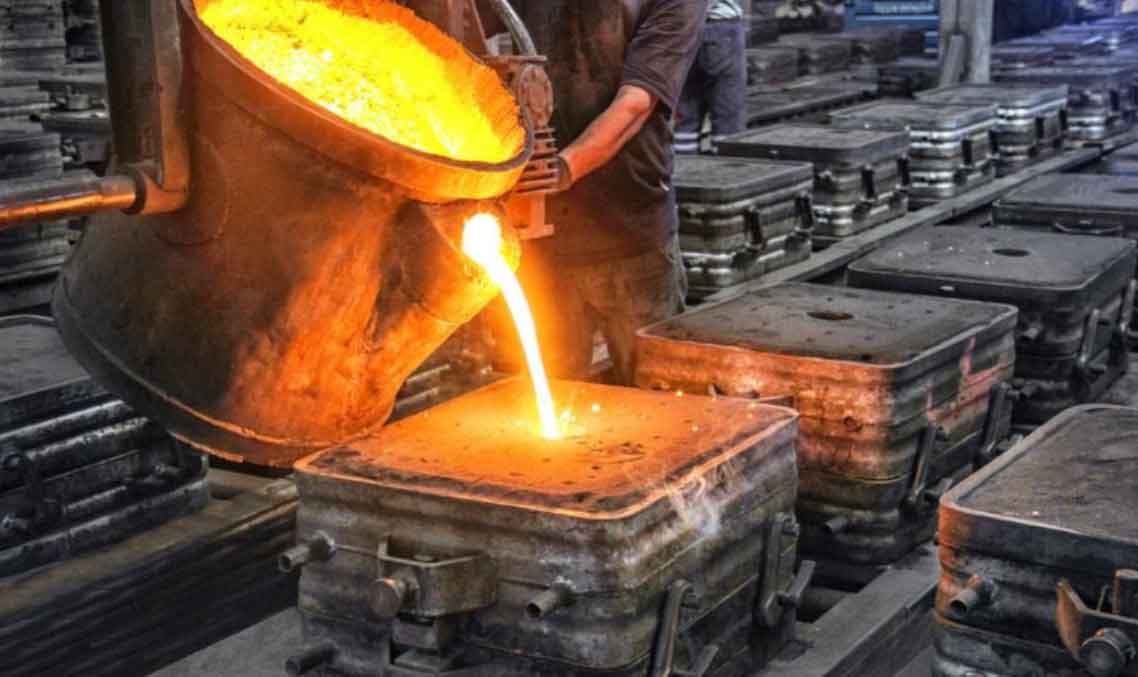
Sand casting is an ancient technique that has seen significant advancements and innovations over the years, allowing manufacturers to stay at the forefront of the industry. These innovations have enabled sand casting to remain a competitive and versatile metal casting method. Here are some key areas of innovation in sand casting:
1. 3D Printing and Rapid Prototyping:
Manufacturers have embraced 3D printing and rapid prototyping technologies to create intricate and complex patterns for sand casting. 3D-printed patterns offer greater design flexibility, faster iteration cycles, and reduced lead times, allowing for more efficient and cost-effective product development.
2. Simulation and Modeling:
Advanced computer simulation and modeling software have become essential tools for sand casting manufacturers. Casting simulation software helps predict potential defects, optimize gating systems, and improve yield, resulting in higher-quality castings and reduced material waste.
3. Binder Systems and Additives:
Innovations in binder systems and additives for molding sand have improved mold strength, reduced casting defects, and enhanced dimensional accuracy. New environmentally-friendly binder systems have also emerged, addressing sustainability concerns.
4. Automated and Robotic Systems:
Automation and robotics have been integrated into various stages of the sand casting process. Automated pouring systems ensure precise metal delivery, while robots handle tasks like mold handling, finishing, and quality inspection, improving efficiency and consistency.
5. Advanced Melting Techniques:
Modern induction and electric arc furnaces have replaced traditional cupola furnaces, providing better control over the melting process and allowing for the use of a wider range of metal alloys.
6. Advanced Materials and Alloys:
Sand casting manufacturers are working with an expanded range of materials and alloys, including high-performance metals like titanium, nickel-based alloys, and aluminum alloys, to meet the demands of diverse industries.
7. Eco-Friendly Practices:
Manufacturers are implementing sustainable practices, such as recycling molding sand and using environmentally friendly binders, to reduce waste and minimize the environmental impact of sand casting.
8. Real-Time Monitoring and Data Analytics:
IoT-enabled sensors and real-time monitoring systems are used to collect data during the casting process. Data analytics help identify trends, optimize process parameters, and improve overall casting quality and productivity.
9. Integrated Quality Control:
Advancements in non-destructive testing (NDT) techniques, like X-ray, ultrasonic testing, and magnetic particle inspection, enable manufacturers to perform rigorous quality control on castings without damaging the components.
10. Continuous Process Improvement:
Sand casting manufacturers emphasize continuous improvement methodologies like Six Sigma and Lean Manufacturing to identify bottlenecks, reduce waste, and enhance overall process efficiency.
By embracing these and other innovations, sand casting manufacturers can maintain their competitive edge, deliver high-quality castings with greater precision, and meet the evolving demands of industries ranging from automotive and aerospace to heavy machinery and beyond. Constantly pushing the boundaries of sand casting technology ensures its relevance and effectiveness in today’s manufacturing landscape.