The journey of sand casting parts involves several key steps, from the initial design to the final product. Here is a comprehensive overview of the process:
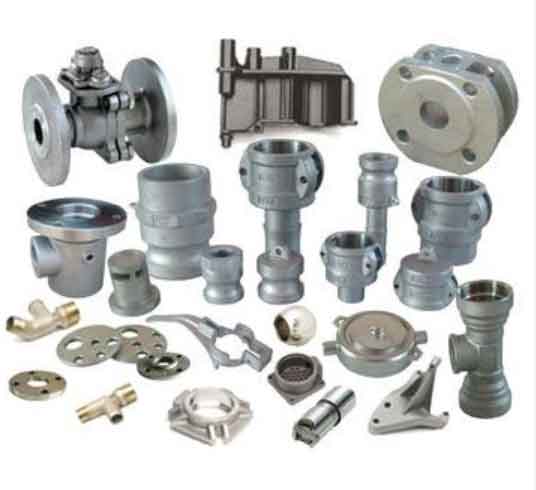
- Design and Pattern Making:
- The process begins with the design of the component that needs to be cast.
- A pattern is created, which is a replica of the final part, typically made from wood, metal, or plastic.
- The pattern accounts for the casting’s shrinkage and other factors that influence its final dimensions.
- Mold Preparation:
- The pattern is placed in a molding box or flask, and molding sand is packed around it.
- The molding sand is typically a mixture of silica sand, clay, and other additives to enhance its properties.
- Mold Assembly and Gating System:
- After the molding sand is compacted, the top half of the flask is placed, and the two halves are securely clamped together.
- Channels and gates (pouring system) are created in the sand to allow molten metal to flow into the mold and fill the cavity.
- Melting and Pouring:
- The chosen metal alloy is melted in a furnace at the foundry to its required temperature.
- Once the metal reaches the desired temperature, it is poured into the mold through the gating system.
- Solidification and Cooling:
- The molten metal fills the mold cavity and solidifies into the shape of the pattern.
- As the metal cools, it shrinks and takes on the exact shape of the pattern within the mold.
- Mold Removal and Cleaning:
- Once the metal has solidified and cooled sufficiently, the flask is opened, and the sand mold is removed.
- The casting is separated from the excess sand, which is reclaimed and reused for future molds.
- Finishing and Inspection:
- The casting may undergo various finishing processes, such as trimming, grinding, and machining, to achieve the desired surface finish and dimensional accuracy.
- The finished casting is inspected for defects, dimensional accuracy, and other quality parameters.
- Post-Casting Heat Treatment (if required):
- Some castings may undergo heat treatment processes to improve their mechanical properties and remove internal stresses.
- Surface Treatment and Coating (if required):
- Some castings may receive additional surface treatments or coatings, such as painting, plating, or powder coating, to enhance their corrosion resistance or appearance.
- Final Assembly and Application:
- The finished castings are ready for final assembly into the intended product or application.
- They are then incorporated into various industries and applications, as discussed in previous responses.
Throughout the entire journey of sand casting parts, close attention to quality control and process optimization is crucial to ensuring the production of high-quality and precise components for various industries.