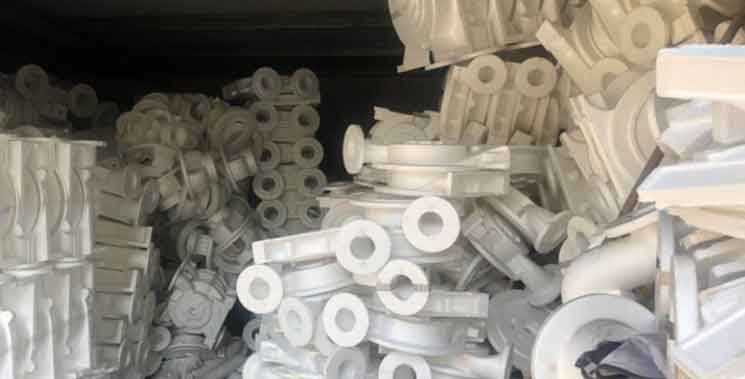
Lost foam casting has witnessed significant advancements and continues to evolve as a highly innovative and efficient metal casting process. These advancements have expanded its applications across various industries. Here are some key innovations and applications in lost foam casting:
1. Improved Foam Materials:
Advancements in foam materials have led to increased dimensional stability, enhanced surface finish, and improved heat resistance. These improvements ensure more accurate and reliable reproduction of intricate details during the casting process, resulting in high-quality finished products.
2. Pattern Coating Technology:
The development of advanced pattern coatings has significantly contributed to the efficiency and success of lost foam casting. These coatings provide excellent refractory properties, reduce pattern degradation, and improve surface finish. They also help to minimize the generation of gas and defects during the metal pouring stage, resulting in higher casting quality.
3. Digital Design and Simulation:
The use of computer-aided design (CAD) and simulation software has revolutionized the design and optimization of lost foam castings. Virtual casting simulations enable engineers to visualize and analyze the filling and solidification behavior of the molten metal, optimizing gating systems and reducing the likelihood of defects. This digital design approach enhances casting quality, reduces production time, and minimizes the need for costly trial-and-error iterations.
4. Automation and Robotics:
Automation and robotics have been integrated into the lost foam casting process to enhance productivity, efficiency, and repeatability. Automated foam pattern molding, handling, and coating systems enable faster production cycles, reduce manual labor, and ensure consistent quality. Robotic systems are also utilized for precise pouring of molten metal into the foam patterns, minimizing the risk of human error and achieving greater process control.
5. Lightweight Component Production:
Lost foam casting offers exceptional capabilities for manufacturing lightweight components with complex geometries. This makes it an ideal choice for industries such as automotive and aerospace, where weight reduction is critical. The process allows for the creation of intricate internal structures, hollow sections, and thin walls, resulting in lightweight castings that maintain strength and structural integrity.
6. Engine and Powertrain Components:
Lost foam casting finds extensive application in the production of engine and powertrain components. Cylinder heads, engine blocks, intake manifolds, and transmission cases are just a few examples. The design freedom and precision of lost foam casting enable the creation of complex cooling passages, intricate internal features, and optimized geometries, contributing to improved engine performance, fuel efficiency, and reduced emissions.
7. Agricultural and Construction Equipment:
Lost foam casting is utilized in the production of various components for agricultural and construction equipment. These include hydraulic valve bodies, gearboxes, structural brackets, and implement parts. The process allows for the integration of functional features, weight reduction, and increased durability, meeting the demanding requirements of these rugged applications.
8. Custom and Prototype Components:
Lost foam casting offers a cost-effective solution for the production of custom and prototype components. The flexibility of foam patterns allows for quick design iterations and modifications without the need for expensive tooling. This makes lost foam casting an attractive choice for manufacturers seeking fast turnaround times, rapid prototyping, and small production runs.
The continuous innovation in lost foam casting has expanded its applications in various industries, enabling the production of high-quality, complex, and lightweight components. The combination of advanced materials, digital design tools, automation, and specialized coatings has elevated the efficiency, precision, and overall performance of the lost foam casting process.