Sand casting, a traditional manufacturing process, has also seen advancements and innovations in recent years, opening up new possibilities and improving the production of sand casting parts. Here are some innovations in sand casting:
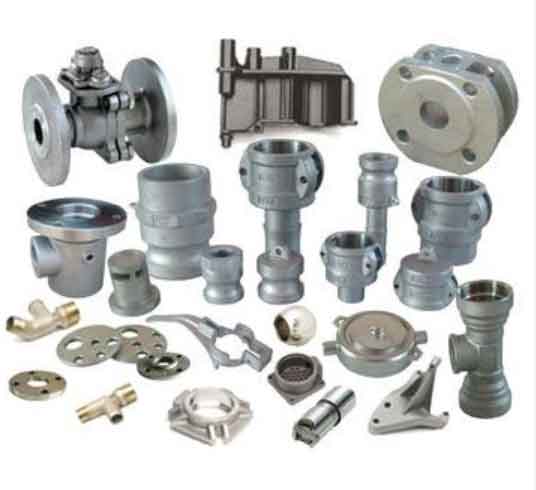
- Digital design and simulation: The use of computer-aided design (CAD) software and advanced simulation tools allows for more accurate and efficient design of sand casting parts. Virtual simulations can predict and optimize the casting process, identifying potential defects and optimizing gating and risering systems.
- 3D printing for sand molds and cores: Additive manufacturing, specifically 3D printing, has gained popularity in sand casting. It enables the rapid production of sand molds and cores directly from digital designs, reducing the lead time and costs associated with traditional pattern-making methods. Complex geometries and internal features can be achieved more easily.
- Advanced molding materials: Innovations in molding materials have led to the development of binders and additives that improve mold strength, dimensional accuracy, and surface finish. These materials enhance the overall quality of sand casting parts and reduce the likelihood of defects.
- Robotic automation: Robotic systems are increasingly being integrated into sand casting processes to automate tasks such as mold handling, pouring, and post-casting operations. This improves efficiency, reduces labor costs, and enhances process control.
- Advanced casting techniques: Various advanced casting techniques have been developed to enhance the sand casting process. These include vacuum-assisted casting, centrifugal casting, and low-pressure casting. These techniques offer improved casting quality, reduced porosity, and better control over solidification.
- Digital monitoring and control systems: Sensor technology and data monitoring systems have been introduced to monitor and control critical parameters during the casting process. Real-time data collection allows for better process control, reducing the risk of defects and ensuring consistent quality.
- Improved material properties: Research and development efforts have focused on enhancing the mechanical and physical properties of sand casting materials. This includes the development of alloy compositions, heat treatments, and post-casting processes that improve the strength, hardness, and corrosion resistance of the cast parts.
- Green sand reclamation: Environmentally conscious practices have led to advancements in green sand reclamation techniques. These techniques allow for the reuse of sand and reduce waste generation, making the sand casting process more sustainable and cost-effective.
- Advanced post-casting processes: Innovations in post-casting processes, such as heat treatment, surface treatment, and machining technologies, contribute to the improvement of the final product’s quality and performance. These processes enhance the dimensional accuracy, surface finish, and overall integrity of the sand casting parts.
These advancements in sand casting technology and processes offer improved quality, efficiency, and design flexibility. They enable the production of more complex and high-performance sand casting parts while reducing lead times and costs. Manufacturers are continually exploring new possibilities and pushing the boundaries of sand casting through ongoing research and development efforts.