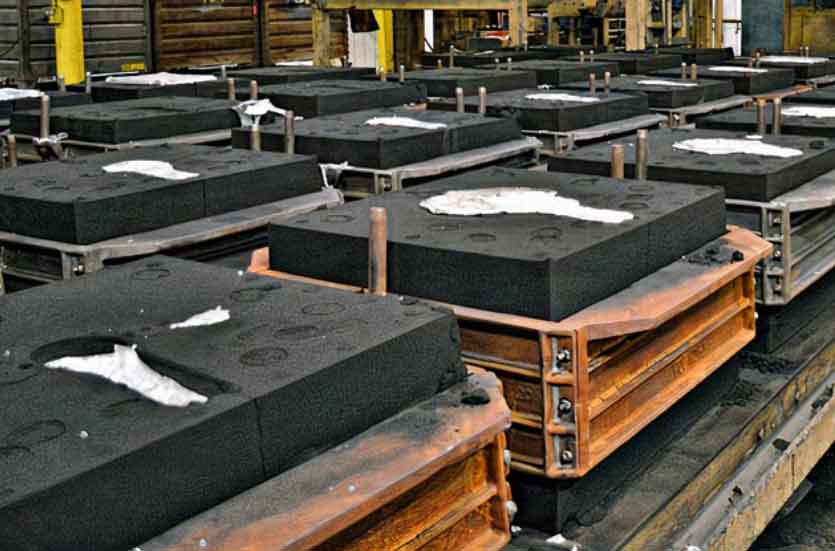
Innovations in resin sand casting have been instrumental in pushing the boundaries of metalwork, enabling the creation of intricate and complex metal components with greater efficiency and precision. These advancements leverage modern technologies and materials, offering new possibilities and expanding the capabilities of the resin sand casting process. Here are some notable innovations driving the progress of resin sand casting:
1. Digital Simulation and Modeling:
The integration of digital simulation and modeling tools has revolutionized resin sand casting. Finite element analysis (FEA) and computational fluid dynamics (CFD) simulations are employed to optimize mold designs, gating systems, and cooling processes. These simulations help identify potential defects and optimize the casting process before physically producing the mold, reducing costs and improving casting quality.
2. 3D Printing for Patterns and Cores:
The combination of 3D printing and resin sand casting has opened up new design opportunities. 3D printing is used to create precise and intricate patterns and cores, allowing for the production of highly complex metal components without the need for traditional pattern-making methods. This integration significantly reduces lead times for rapid prototyping and production.
3. Hybrid Casting Methods:
Hybrid casting methods, such as combining resin sand casting with other processes like investment casting or lost foam casting, have emerged to leverage the strengths of each method. These hybrid approaches offer improved surface finishes, reduced material usage, and increased design freedom, expanding the range of applications for resin sand casting.
4. Smart Sensors and Monitoring Systems:
Advancements in sensor technology enable real-time monitoring of key process parameters during casting. Smart sensors are employed to monitor mold temperature, casting temperature, and solidification rates, providing valuable data for process optimization and ensuring consistent and high-quality castings.
5. Sustainable Resin Binders:
Foundries are exploring the use of more sustainable resin binders, such as bio-based or recycled resins, to reduce the environmental impact of resin sand casting. These eco-friendly binders offer similar performance to traditional resins while contributing to more sustainable manufacturing practices.
6. AI and Machine Learning Integration:
AI (Artificial Intelligence) and machine learning technologies are being applied to optimize process parameters and predict potential defects in resin sand casting. By analyzing historical data and process variables, these technologies help improve process control and casting performance.
7. Advanced Sand Reclamation Systems:
Efficient sand reclamation systems have been developed to recycle and recondition used sand, extending its lifespan and reducing waste generation. These systems contribute to more sustainable foundry practices and minimize the environmental impact of resin sand casting.
8. Lightweighting Solutions:
Resin sand casting is increasingly employed in lightweighting solutions, where complex designs and thin-walled structures are used to reduce component weight while maintaining strength. This is particularly valuable in industries like automotive and aerospace, where weight reduction is critical for fuel efficiency and performance.
These innovations in resin sand casting technology continue to push the boundaries of metalwork, making the process more efficient, precise, and environmentally friendly. As research and development efforts persist, further advancements are expected, unlocking even more possibilities and applications for resin sand casting in the realm of metal fabrication.