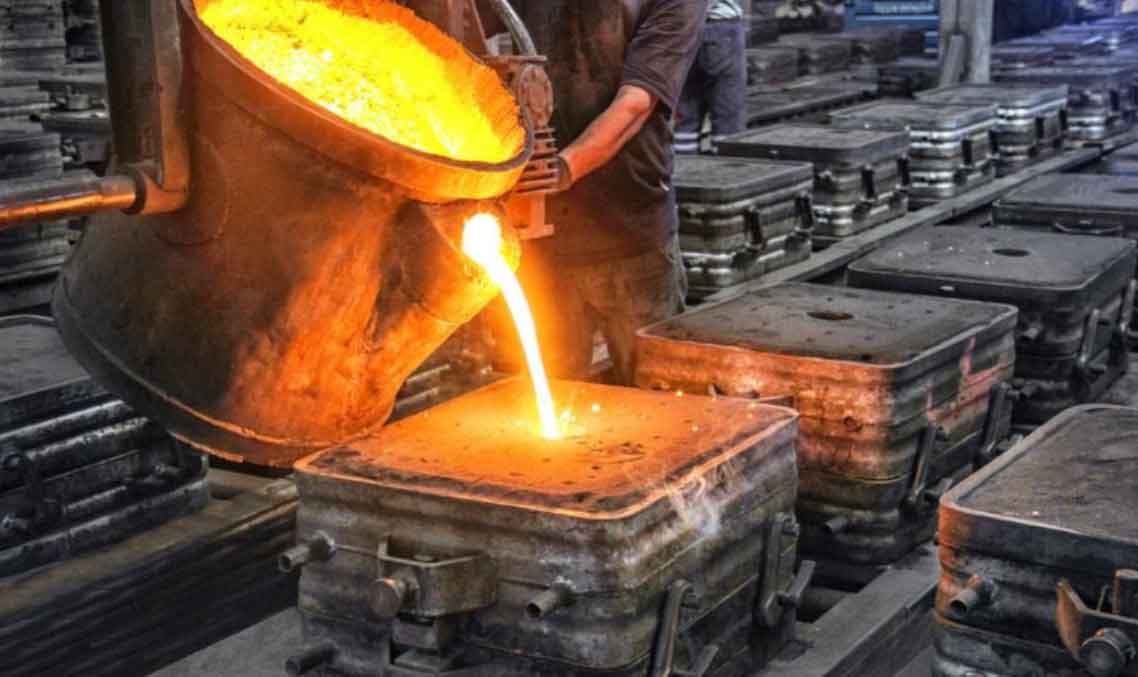
Sand casting is a traditional manufacturing method, but it has not been immune to technological advancements. To stay ahead and remain competitive, sand casting manufacturers have adopted various innovations and modern practices. Here are some of the key innovations in sand casting technology:
- Digital Design and Simulation: Advanced computer-aided design (CAD) software and simulation tools allow manufacturers to create and optimize casting designs virtually. These tools help predict and address potential defects, optimize gating systems, and improve overall casting quality.
- Additive Manufacturing for Patterns and Cores: 3D printing or additive manufacturing is being used to create sand casting patterns and cores quickly and cost-effectively. This allows for more complex geometries and reduced lead times in pattern production.
- Automated Molding Machines: Automated molding machines have been introduced to improve consistency and reduce manual labor in the mold-making process. These machines can produce high-quality molds with greater precision and speed.
- Robotics and Automation in Casting: Manufacturers are integrating robotics and automation into the casting process to handle tasks such as pouring molten metal, handling heavy molds, and removing castings from molds. Automation enhances efficiency and reduces the risk of human error.
- Innovative Sand Reclamation Techniques: Sand reclamation processes have advanced, allowing manufacturers to recycle and reuse sand more efficiently. This reduces waste and lowers raw material costs.
- Real-time Monitoring and Sensing: Sensors and real-time monitoring systems are used to track process parameters like temperature, pressure, and flow rates during the casting process. This data helps manufacturers optimize process parameters for better quality control.
- High-Performance Casting Materials: Advancements in metallurgy have led to the development of high-performance casting materials with superior mechanical properties and increased durability, expanding the range of applications for sand casting.
- Metal Additives and Modifiers: The use of metal additives and modifiers has improved the properties of castings, such as enhancing heat resistance, reducing shrinkage defects, and improving machinability.
- Improved Sand Binders and Additives: Modern sand binders and additives have been developed to enhance mold strength, improve surface finish, and reduce gas-related defects.
- Non-Destructive Testing (NDT) Techniques: NDT techniques, such as X-ray, ultrasonic testing, and 3D scanning, have been integrated into the inspection process to identify internal defects and ensure casting integrity.
- Energy Efficiency and Sustainability: Manufacturers are adopting energy-efficient practices and sustainable initiatives to minimize environmental impact and meet evolving regulations.
- IoT and Data Analytics: The integration of the Internet of Things (IoT) and data analytics enables manufacturers to monitor equipment performance, track production metrics, and identify opportunities for process optimization.
By embracing these innovations, sand casting manufacturers can enhance their capabilities, improve product quality, reduce production times, and stay competitive in the ever-evolving manufacturing landscape. Staying ahead through technological advancements allows them to meet customer demands and tackle complex casting challenges effectively.