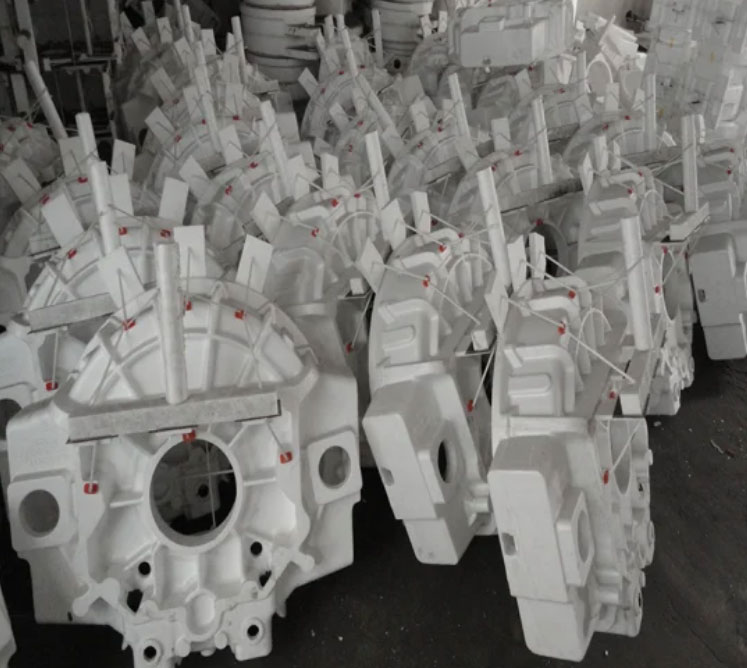
Lost foam casting (LFC) has found extensive applications in both the automotive and aerospace industries due to its ability to produce complex and lightweight components with high precision. Here are some key applications of lost foam casting in these industries:
Automotive Industry:
- Engine Blocks and Cylinder Heads: Lost foam casting is used to manufacture engine blocks and cylinder heads for internal combustion engines. Lost foam casting allows for intricate cooling passages and precise tolerances, resulting in efficient and high-performance engine components.
- Intake Manifolds: The complex geometries and internal passages in intake manifolds can be easily achieved using lost foam casting. This method ensures a smooth internal surface, promoting optimal airflow for improved engine performance.
- Transmission Housings: Lost foam casting is used to produce transmission housings with intricate designs and lightweight features. The process allows for the integration of multiple components into a single casting, reducing assembly requirements.
- Suspension Components: Lost foam casting is employed for manufacturing suspension components, such as control arms and knuckles, with complex shapes and precise tolerances. Lightweight suspension parts contribute to enhanced vehicle handling and fuel efficiency.
- Exhaust Manifolds: Lost foam casting is utilized to create exhaust manifolds with intricate shapes and reduced weight. The process enables the integration of design features that optimize exhaust gas flow and reduce emissions.
Aerospace Industry:
- Aircraft Engine Components: Lost foam casting is employed to produce various critical components of aircraft engines, such as turbine blades, compressor vanes, and casing segments. The method allows for complex internal cooling structures that enhance engine efficiency and performance.
- Aircraft Structural Parts: Lost foam casting is used to manufacture lightweight and structurally complex components, such as wing ribs, bulkheads, and fuselage sections. The near-net-shape capability of Lost foam casting reduces material waste and machining requirements.
- Rocket Engine Components: Lost foam casting is utilized in the production of rocket engine components, including nozzles and combustion chambers. The process allows for intricate internal features and reduces the need for post-casting machining.
- Aircraft Landing Gear Components: Lost foam casting is used to create landing gear components, such as main gear beams and shock strut housings. The process enables the integration of design features that enhance structural integrity and load-bearing capacity.
- Satellite and Spacecraft Components: Lost foam casting is applied to manufacture lightweight and intricate components for satellites and spacecraft, such as antenna supports and satellite structure components.
In both industries, lost foam casting’s ability to produce near-net-shape components with reduced material waste, precision, and design flexibility makes it an attractive casting method for meeting the demanding requirements of modern automotive and aerospace applications. Its capacity to create complex and lightweight parts while reducing the need for secondary operations contributes to improved efficiency, reduced costs, and enhanced overall performance in these critical industries.