The durability of steel casting is crucial for their performance in various industrial applications, ranging from automotive and aerospace to construction and heavy machinery. To enhance the durability and longevity of steel casting, innovative surface treatment technologies are being developed and implemented. This article explores these cutting-edge technologies, highlighting their benefits, applications, and future prospects. Detailed tables and lists are included for clarity.
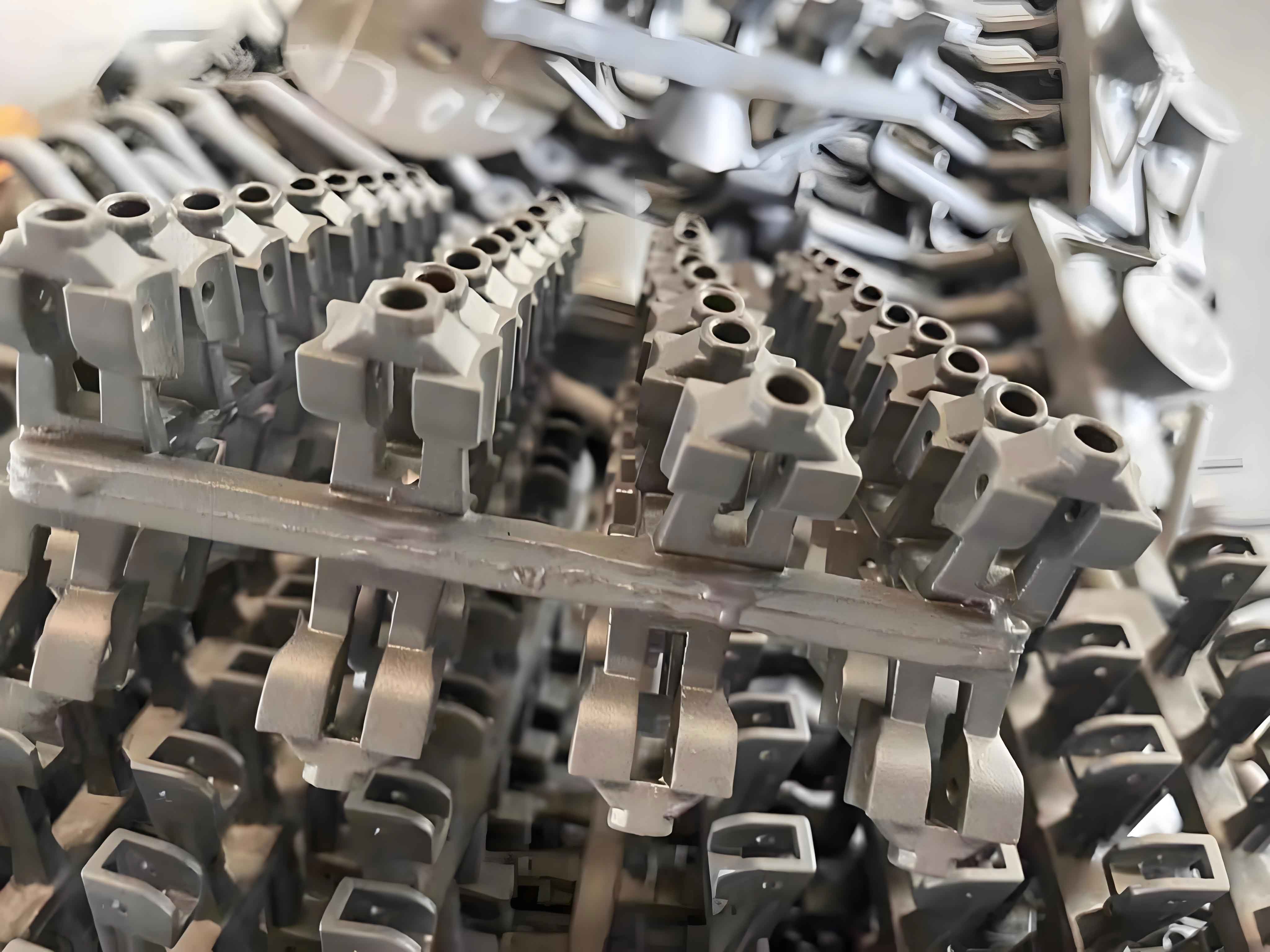
Introduction
Surface treatment technologies play a vital role in improving the mechanical properties of steel casting. These treatments can enhance wear resistance, corrosion resistance, fatigue strength, and overall durability. With continuous advancements in material science and engineering, several innovative surface treatment methods have emerged, each offering unique benefits for specific applications.
Importance of Surface Treatment for Steel Casting
- Increased Wear Resistance:
- Surface treatments significantly improve the wear resistance of steel casting, extending their service life in abrasive environments.
- Enhanced Corrosion Resistance:
- Treatments create protective barriers on the surface, preventing corrosion and degradation in harsh conditions.
- Improved Fatigue Strength:
- Surface hardening techniques enhance the fatigue strength of steel casting, making them more resistant to cyclic loading.
- Aesthetic and Functional Improvements:
- Surface treatments can also improve the appearance and functional properties of steel casting, such as reducing friction or enhancing adhesion for coatings.
Table: Importance of Surface Treatment for Steel Casting
Benefit | Description | Impact on Steel Casting |
---|---|---|
Increased Wear Resistance | Improves resistance to abrasive wear | Longer service life in harsh environments |
Enhanced Corrosion Resistance | Creates protective barriers to prevent corrosion | Extended lifespan in corrosive conditions |
Improved Fatigue Strength | Enhances resistance to cyclic loading | Greater durability under repeated stress |
Aesthetic and Functional Improvements | Enhances appearance and functional properties | Better performance and visual appeal |
Innovative Surface Treatment Technologies
- Thermal Spraying:
- Description: A process where molten or semi-molten materials are sprayed onto the surface to form a coating.
- Benefits: Provides high wear and corrosion resistance, suitable for large and complex shapes.
- Laser Cladding:
- Description: A technique that uses a laser to fuse a coating material onto the substrate, creating a metallurgically bonded layer.
- Benefits: Produces coatings with excellent adhesion and minimal dilution, ideal for repairing and enhancing high-wear areas.
- Physical Vapor Deposition (PVD):
- Description: A vacuum deposition method where thin films are deposited on the surface through condensation of vaporized material.
- Benefits: Produces hard, wear-resistant coatings with excellent adherence and uniform thickness.
- Chemical Vapor Deposition (CVD):
- Description: A process where gaseous reactants form a solid coating on the substrate through chemical reactions.
- Benefits: Creates uniform, high-purity coatings with excellent thermal stability and wear resistance.
- Electroplating:
- Description: An electrochemical process that deposits a layer of metal onto the surface through an electric current.
- Benefits: Enhances corrosion resistance and wear properties, commonly used for decorative and functional purposes.
- Nitriding:
- Description: A thermochemical process that diffuses nitrogen into the surface to create a hard, wear-resistant layer.
- Benefits: Increases surface hardness and fatigue strength without significant dimensional changes.
Table: Innovative Surface Treatment Technologies
Technology | Description | Key Benefits | Typical Applications |
---|---|---|---|
Thermal Spraying | Spraying molten materials to form a coating | High wear and corrosion resistance | Turbine blades, engine components |
Laser Cladding | Fusing coating material onto substrate with a laser | Excellent adhesion, minimal dilution | Tooling, repair of worn parts |
Physical Vapor Deposition (PVD) | Vacuum deposition of thin films | Hard, wear-resistant coatings | Cutting tools, medical devices |
Chemical Vapor Deposition (CVD) | Gaseous reactants form a solid coating | Uniform, high-purity coatings | Semiconductor industry, aerospace |
Electroplating | Electrochemical deposition of metal layer | Enhanced corrosion resistance | Decorative finishes, electrical contacts |
Nitriding | Diffusion of nitrogen into the surface | Increased hardness and fatigue strength | Automotive components, gears |
Applications of Surface Treatments in Various Industries
- Automotive Industry:
- Engine components, gears, and suspension parts benefit from enhanced wear and corrosion resistance.
- Aerospace Industry:
- Turbine blades, landing gear, and structural components require surface treatments for durability in extreme conditions.
- Construction and Infrastructure:
- Structural steel components and machinery parts need improved durability and corrosion resistance.
- Heavy Machinery:
- Excavator parts, mining equipment, and industrial machinery benefit from increased wear resistance and lifespan.
List: Key Applications of Surface Treatments by Industry
- Automotive:
- Engine components, gears, suspension parts
- Aerospace:
- Turbine blades, landing gear, structural components
- Construction and Infrastructure:
- Structural steel components, machinery parts
- Heavy Machinery:
- Excavator parts, mining equipment, industrial machinery
Future Prospects of Surface Treatment Technologies
- Nanotechnology:
- The application of nanotechnology in surface treatments can lead to the development of coatings with superior properties, such as self-healing and enhanced mechanical performance.
- Green Surface Treatments:
- Focus on environmentally friendly processes and materials to reduce the ecological impact of surface treatments.
- Integration with Additive Manufacturing:
- Combining surface treatments with additive manufacturing techniques to create complex parts with enhanced surface properties.
- Smart Coatings:
- Development of smart coatings that can respond to environmental changes, such as temperature or stress, to provide real-time protection.
List: Future Prospects for Surface Treatment Technologies
- Nanotechnology:
- Development of coatings with superior properties
- Green Surface Treatments:
- Environmentally friendly processes and materials
- Integration with Additive Manufacturing:
- Enhanced surface properties for complex parts
- Smart Coatings:
- Responsive coatings for real-time protection
Conclusion
Innovative surface treatment technologies are revolutionizing the durability and performance of steel casting across various industries. From thermal spraying and laser cladding to PVD and CVD, these advanced methods offer significant benefits in terms of wear resistance, corrosion protection, and overall longevity. The ongoing development of new technologies, such as nanotechnology and smart coatings, promises to further enhance the capabilities of surface treatments. By embracing these advancements, industries can achieve greater efficiency, reliability, and sustainability in their steel casting applications, ensuring a robust and resilient infrastructure for the future.