1. Introduction
In the automotive industry, the demand for lightweight and high-performance components is constantly increasing. Aluminum alloys, with their excellent combination of properties such as low density, high strength-to-weight ratio, and good corrosion resistance, have become the preferred materials for many automotive parts. Among them, the ADC12 aluminum alloy is widely used in the manufacturing of automobile engine brackets due to its good mechanical properties and machinability.
Squeezing casting, also known as liquid forging, is a near-net-shape forming process that combines the advantages of casting and forging. It can produce complex-shaped parts with dense microstructure, high dimensional accuracy, and good mechanical properties. In this process, the molten metal is forced into a die cavity under high pressure and solidifies under pressure, resulting in a significant reduction in porosity and improved mechanical properties compared to traditional casting methods.
However, the quality of squeezing cast parts is highly dependent on the process parameters, such as casting temperature, holding pressure, mold temperature, and filling speed. The optimization of these parameters is crucial to ensure the production of defect-free and high-quality parts. In this study, the effects of casting temperature and holding pressure on the shrinkage porosity and mechanical properties of ADC12 aluminum alloy castings were investigated using numerical simulation and experimental methods. The aim was to determine the optimal process parameters for the indirect squeezing casting of an automobile engine bracket part.
2. Numerical Simulation
2.1 Governing Equations
The filling and solidification processes of indirect squeezing casting are complex and involve fluid flow, heat transfer, and solidification phenomena. To accurately simulate these processes, the following governing equations were used:
- Volume of Fluid (VOF) Equation: The VOF equation is used to track the free surface of the molten metal during filling. It is given by:
where is the volume fraction of the liquid phase, , , and are the velocity components in the , , and directions, respectively, and is time. - Continuity Equation: The continuity equation ensures the conservation of mass and is expressed as:
- Navier-Stokes Momentum Equation: The Navier-Stokes momentum equation describes the motion of the molten metal and is given by:
where is the density of the fluid, is the dynamic viscosity, is the pressure, and is the body force in the direction. - Fourier Heat Conduction Equation: The Fourier heat conduction equation governs the heat transfer during solidification and is written as:
where is the specific heat capacity, is the temperature, is the thermal conductivity, and is the heat source term.
2.2 Preprocessing
The three-dimensional model of the automobile engine bracket part and the ingate were designed using UG software and then imported into the ProCAST software in the x_t format. The virtual sand box was constructed in ProCAST, with the dimensions of 398 mm × 132 mm × 275 mm. The diameter of the ingate was set to 10 mm, and the length of the pressure chamber was 325 mm.
To balance the computational accuracy and efficiency, the mold was meshed with a size of 10 mm, while the casting, the molten metal in the pressure chamber, and the punch were meshed with a size of 2 mm. The total number of surface meshes was 128,764, and the total number of volume meshes was 2,948,240.
2.3 Process Parameters
The ADC12 aluminum alloy was selected as the casting material, and the H13 steel was used for the mold. The chemical compositions and thermophysical properties of the materials are shown in Tables 1 – 3.
Si | Fe | Cu | Mg | Mn | Zn | Ni | Sn | AI |
---|---|---|---|---|---|---|---|---|
9.6 – 12 | <1.3 | 1.5 – 3.5 | <0.3 | <0.5 | <1.0 | <0.5 | <0.2 | Remainder |
| C | Si | Mn | Cr | Mo | V | P | S | Fe |
| — | — | — | — | — | — | — | — | — | — |
| 0.32 – 0.45 | 0.8 – 1.2 | 0.2 – 0.5 | 4.75 – 5.5 | 1.1 – 1.75 | 0.8 – 1.2 | <0.03 | <0.03 | Remainder |
Material | Density (kg/m³) | Thermal Conductivity (W/m·K) | Specific Heat Capacity (J/kg·K) | Liquidus Temperature (°C) | Solidus Temperature (°C) |
---|---|---|---|---|---|
ADC12 | 2700 | 92 | 963 | 580 | 515 |
H13 | 7830 | 26.2 – 33.4 | 485 – 665 | 1471.2 | 1403.95 |
Shrinkage porosity is a common defect in casting, which is mainly caused by insufficient compensation of the liquid metal during solidification and cooling. The factors that affect the formation of shrinkage porosity include low squeezing pressure, improper pouring temperature, uneven wall thickness of the casting, and不合理的模具结构设计. In this study, the casting temperature and holding pressure were selected as the main optimization parameters. The casting temperature was varied from 620 to 700 °C with a constant holding pressure of 150 MPa, and the holding pressure was varied from 110 to 150 MPa with a constant casting temperature of 680 °C. The other process parameters were set as follows: filling speed of 0.1 m/s, holding time of 13 s, and mold temperature of 250 °C.
The boundary conditions were set as follows: the punch speed in the -Z direction was set to 0.1 m/s, and the pressure boundary condition was applied at the interface between the punch and the molten metal. The outer surface of the mold was set to air cooling, and the heat transfer coefficient between the casting and the mold was set according to the pressure change during the filling and solidification processes. In the pressure holding and solidification stage, the feeding surface method was used for feeding, and the contact surface between the end of the punch stroke and the molten metal was set as the feeding surface.
2.4 Simulation Results and Analysis
The numerical simulation results of the shrinkage porosity under different casting temperatures and holding pressures are shown in Figs. 4 and 5. It can be seen that the defect positions are basically the same. As the casting temperature increases, the defect volume first decreases and then increases, reaching the minimum at 680 °C. When the casting temperature is too low, the fluidity of the molten metal is poor, and the solidification time is short. As a result, a solidified shell is quickly formed at the interface between the molten metal and the mold cavity and continues to thicken, preventing the pressure from being effectively transmitted to the internal molten metal during the pressure holding and solidification stage, resulting in poor feeding effect. When the casting temperature is too high, the shrinkage of the liquid metal increases, and the solidification time is long, resulting in isolated liquid phase regions inside the casting after pressure holding, which are prone to shrinkage porosity during free solidification.
As the holding pressure increases, the defect volume generally decreases, and the change becomes relatively flat after reaching 140 MPa. The essence of pressure holding and feeding in squeezing casting is that the punch applies external force to cause plastic deformation of the solidified shell outside the molten metal and强制补缩 through the flow of the molten metal. When the pressure is low, the feeding effect is poor, resulting in shrinkage porosity in the hot spot area of the casting.
3. Experimental Procedure
3.1 Casting Production
Based on the numerical simulation results, several groups of castings were produced under different process conditions for mechanical property testing. The casting process was carried out using an indirect squeezing casting machine. The ADC12 aluminum alloy was melted in a resistance furnace and heated to the specified casting temperature. The molten metal was then poured into the pressure chamber, and the punch was pressed down at a constant speed to fill the mold cavity and maintain the pressure for a certain time. After solidification, the casting was removed from the mold and cooled in air.
3.2 Mechanical Property Testing
The mechanical properties of the castings were tested using a WDW100 electronic universal testing machine for tensile testing and an HBS3000V visual Brinell hardness tester for hardness testing. The tensile specimens were machined from the castings according to the standard ASTM E8, with a gauge length of 50 mm and a diameter of 10 mm. The hardness specimens were prepared with a surface roughness of Ra 0.8 μm. For each group of specimens, three samples were tested, and the average values were taken as the results.
3.3 Microstructural Analysis
Small samples were taken from the core and outer regions of the castings for metallographic analysis. The samples were polished and etched with an aluminum alloy etchant (5% HNO₃ + 5% HCl + 5% HF) for about 10 seconds. The microstructures were observed using a Leica6000M metallurgical microscope. The microstructural characteristics, such as the grain size, shape, and distribution of the phases, were analyzed to study the effect of the process parameters on the microstructure of the ADC12 aluminum alloy castings.
4. Results and Discussion
4.1 Effect of Casting Temperature on Mechanical Properties and Microstructure
The mechanical property test results of the castings at different casting temperatures are shown in Fig. 7a. It can be seen that when the casting temperature is 680 °C, the tensile strength, elongation, and hardness of the casting reach the best values. However, as the casting temperature further increases, the mechanical properties begin to decrease. This is because when the casting temperature is too low, the fluidity of the molten metal is poor, resulting in incomplete filling of the mold cavity and the formation of shrinkage porosity, which reduces the mechanical properties of the casting. When the casting temperature is too high, the coarse grains are formed due to the slow cooling rate, and the segregation of alloy elements is aggravated, also leading to a decrease in mechanical properties.
The microstructural analysis results of the castings at different casting temperatures are shown in Fig. 8. It can be seen that as the casting temperature increases, the grain size of the α-Al phase first slightly decreases and then slightly increases, and the grain morphology does not change significantly. This is because at a lower casting temperature, the nucleation rate is relatively high due to the larger undercooling degree, resulting in a finer grain size. However, as the casting temperature increases, the growth rate of the grains also increases, leading to a slight increase in grain size.
4.2 Effect of Holding Pressure on Mechanical Properties and Microstructure
The mechanical property test results of the castings at different holding pressures are shown in Fig. 7b. It can be seen that as the holding pressure increases from 110 MPa to 130 MPa, the mechanical properties of the casting significantly improve. After reaching 130 MPa, the improvement rate slows down. In actual production, it is found that when the holding pressure is further increased, problems such as difficult demolding and mold sticking and scratching may occur, and excessive pressure will also accelerate the wear of the mold. Therefore, from the perspective of production efficiency, it is not suitable to select a higher holding pressure.
The microstructural analysis results of the castings at different holding pressures are shown in Figs. 9 and 10. It can be seen that as the holding pressure increases, the grain size of the α-Al phase明显减小, and the grain morphology changes from a rosette shape to a spherical shape. At a lower holding pressure, the Al-Si eutectic phase appears in a flaky and needle-like structure. The coarse primary Si flakes and needle-like eutectic Si组织 will割裂 the alloy matrix, and the tips and corners of the Si phase will cause stress concentration, resulting in a significant decrease in the mechanical properties of the alloy. When the holding pressure increases to 130 MPa, the amount of flaky eutectic组织 decreases, the grain size decreases, the length of the needle-like eutectic组织 decreases, and the α-Al phase changes from a dendritic crystal to a rosette crystal. When the holding pressure reaches 150 MPa, the pressure is effectively transmitted to the core of the casting, and the molten metal changes from free solidification to solidification under pressure, resulting in a significant change in the metallographic morphology. At this time, the grain morphologies in the core and outer regions of the casting are basically the same, with a uniform fine-grained structure, and the mechanical properties of the casting reach the best.
4.3 Relationship between Defect, Microstructure, and Mechanical Properties
The results show that the changes in the defect volume, microstructure, and mechanical properties of the casting are consistent. As the holding pressure increases, the defect volume decreases, accompanied by a change in the grain structure morphology and a significant decrease in the grain size, resulting in a rapid improvement in mechanical properties. After reaching 140 MPa, the effect of the holding pressure on eliminating defects, refining grains, and improving mechanical properties decreases. When the casting temperature increases, the defect volume and grain size first decrease and then increase, reaching the minimum at 680 °C, and the mechanical properties are the best at this time.
When the casting temperature is 680 °C and the holding pressure is 150 MPa, the defect volume of the casting is the smallest, the grains are significantly refined, and the mechanical properties are ideal. Therefore, these are the optimal process parameters for this casting.
4.4 Dominant Factor Analysis
In the range of casting temperatures from 620 to 700 °C and holding pressures from 110 to 150 MPa, the changes in the defect volume, mechanical properties, and microstructure with the holding pressure are more significant than those with the casting temperature. This indicates that the holding pressure is the dominant factor in this process parameter range.
5. Conclusion
(1) The optimization of the squeezing casting process parameters for the ADC12 aluminum alloy automobile bracket part was successfully carried out using numerical simulation and experimental methods. The effects of casting temperature and holding pressure on the shrinkage porosity, mechanical properties, and microstructure of the castings were investigated.
(2) The optimal process parameters were determined as follows: casting temperature of 680 °C, holding pressure of 150 MPa, and mold temperature of 250 °C. Under these conditions, the casting has the smallest defect volume, refined grains, and excellent mechanical properties.
(3) The holding pressure plays a dominant role in eliminating shrinkage porosity defects, improving the microstructure, and enhancing the mechanical properties of the castings. The results of this study can provide a reference for the industrial production of high-quality ADC12 aluminum alloy automobile bracket parts using the squeezing casting process.
In future research, further optimization of other process parameters, such as filling speed and holding time, can be considered to further improve the quality and performance of the castings. Additionally, the study of the effect of alloying elements on the squeezing casting process and the mechanical properties of the castings can also be explored to develop new aluminum alloy materials with better performance for automotive applications.
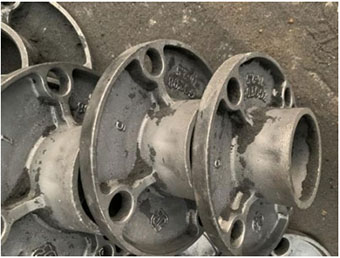