Liquid die forging is a green forming technology with high energy efficiency for metal materials, also known as squeeze casting liquid die forging. To some extent, it has the common advantages of casting and forging. It is to melt qualified molten metal directly into the liquid forging die cavity used in production, and then the hydraulic press puts a certain pressure on the liquid metal to make the molten or semi molten metal complete rheological forming, solidification and feeding under the action of pressure. Through liquid die forging process, the internal structure of the casting is dense, the appearance is smooth, and the size is accurate. The application of liquid die forging has received extensive attention at home and abroad. It is an advanced forming technology with broad application prospects. The process flow of liquid forging is shown in the figure. It includes four basic steps: pouring, pressurizing, holding and demoulding.
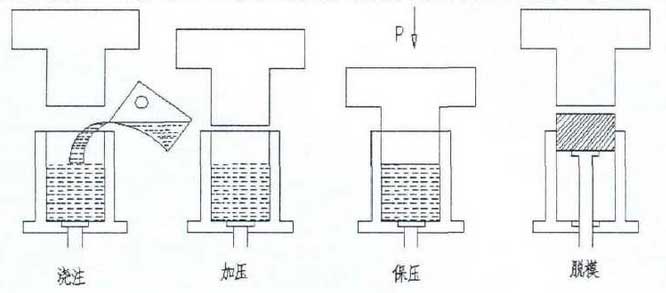
Pouring refers to the hydraulic injection of a certain amount of molten metal into the mold cavity, which can be divided into manual pouring and mechanical pouring. Pressurization refers to the working process of applying a pressure to the metal melt by using special equipment (hydraulic forging machine), which can be divided into two ways of direct pressure and indirect pressure; pressure holding refers to the continuous setting after the metal melt fills the pressure chamber or cavity It is the last step in the process of liquid forging, which is mainly to take the solidified casting out of the mold cavity.
Liquid die forging was developed in 1940s, more than 100 years later than die casting. Benedyk, an American scholar, published a famous paper named “squeezecasting”. The process has two names: “squeeze casting” and “liquid die forging”. Some experts in China call the forming process “liquid die forging”. The term “liquid die forging” is adopted in this paper. In the 1960s and 1970s, liquid die forging technology was the most active period in the world. In the mid-1960s, the former Soviet Union developed more than 200 kinds of liquid die forging technology for parts. In recent years, liquid die forging technology has been developed rapidly in China since the early 1970s.