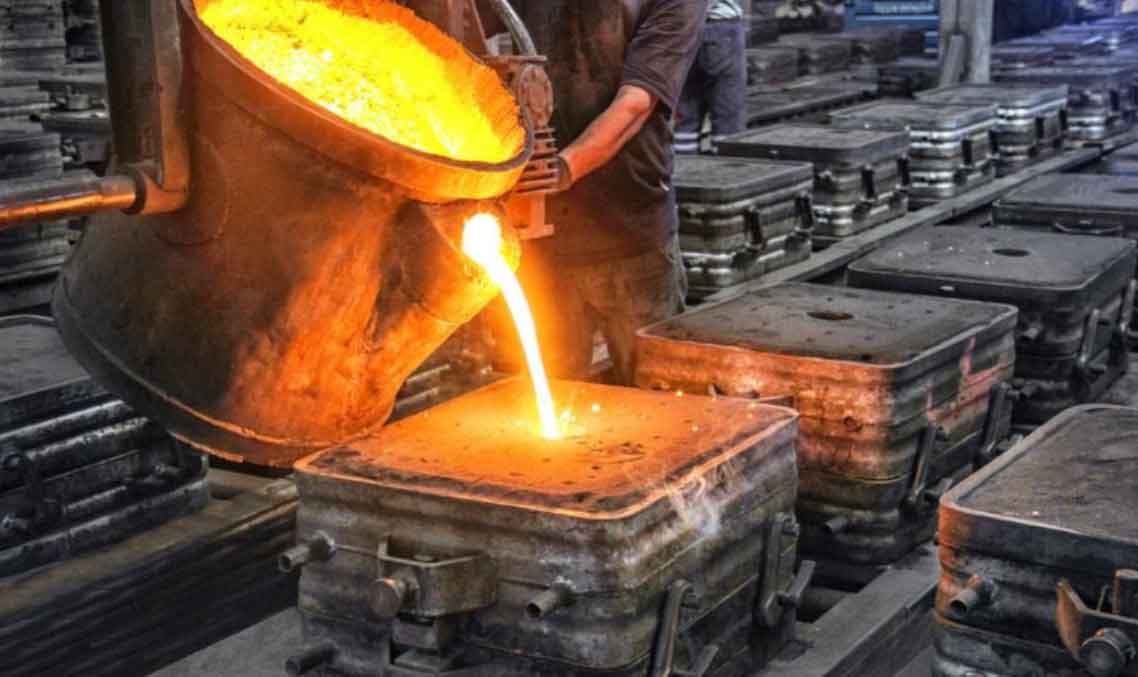
Investing in workforce development and providing training and skills development opportunities are essential for the success and growth of sand casting manufacturers. A skilled and knowledgeable workforce can significantly improve production efficiency, product quality, and overall operational excellence. Here are some key aspects of investing in workforce development in sand casting manufacturing:
1. Comprehensive Training Programs:
- Develop comprehensive training programs for new hires and existing employees. These programs should cover all aspects of sand casting processes, including pattern making, molding, melting, pouring, finishing, and quality control.
2. Cross-Training and Multiskilling:
- Encourage cross-training and multiskilling to equip employees with diverse skills. This allows for flexibility in the workforce, better job rotation, and improved problem-solving capabilities.
3. Continuous Learning and Upskilling:
- Encourage a culture of continuous learning and upskilling. Offer workshops, seminars, and online courses to keep employees updated with the latest advancements in sand casting technology and best practices.
4. On-the-Job Training (OJT):
- Provide on-the-job training to new hires and employees working on new processes or equipment. OJT allows employees to learn by doing and gain practical experience.
5. Mentorship Programs:
- Implement mentorship programs where experienced employees mentor and guide newcomers. Mentorship helps transfer knowledge and fosters a supportive work environment.
6. Certifications and Accreditation:
- Encourage employees to pursue relevant certifications and accreditations related to sand casting and foundry operations. Certifications add value to both the employee and the company.
7. Safety Training:
- Prioritize safety training to ensure a safe working environment for all employees. Proper safety training reduces the risk of accidents and injuries in a foundry setting.
8. Leadership Development:
- Invest in leadership development programs to groom potential leaders within the organization. Strong leadership is essential for driving growth and fostering a positive work culture.
9. Employee Engagement:
- Foster employee engagement and involvement in decision-making processes. Involve employees in improvement initiatives and value their input and ideas.
10. Performance Recognition and Incentives:
- Recognize and reward employees for their contributions and achievements. Performance-based incentives motivate employees to excel in their roles.
11. Collaboration with Educational Institutions:
- Collaborate with technical schools, community colleges, and universities to promote careers in foundry and sand casting manufacturing. Establish internship programs to attract young talent.
12. Benchmarking and Best Practices:
- Benchmark against industry best practices and continuously strive for improvement. Participate in industry events, conferences, and forums to gain insights and knowledge.
By investing in workforce development, sand casting manufacturers can build a skilled and motivated team that is equipped to handle challenges, drive innovation, and adapt to the evolving needs of the industry. A well-trained workforce leads to higher productivity, better product quality, and ultimately, a competitive advantage in the market.