Casting is a fundamental industry of the national economy, providing casting products for downstream industries such as automobiles, construction machinery, rail transit, mechanical equipment, thermal engineering, aerospace, etc. The casting industry can be divided into sand casting, precision casting, die casting, etc. by process category. Sand casting is the basic process of casting production, and it is a long-standing casting process that can be traced back thousands of years.
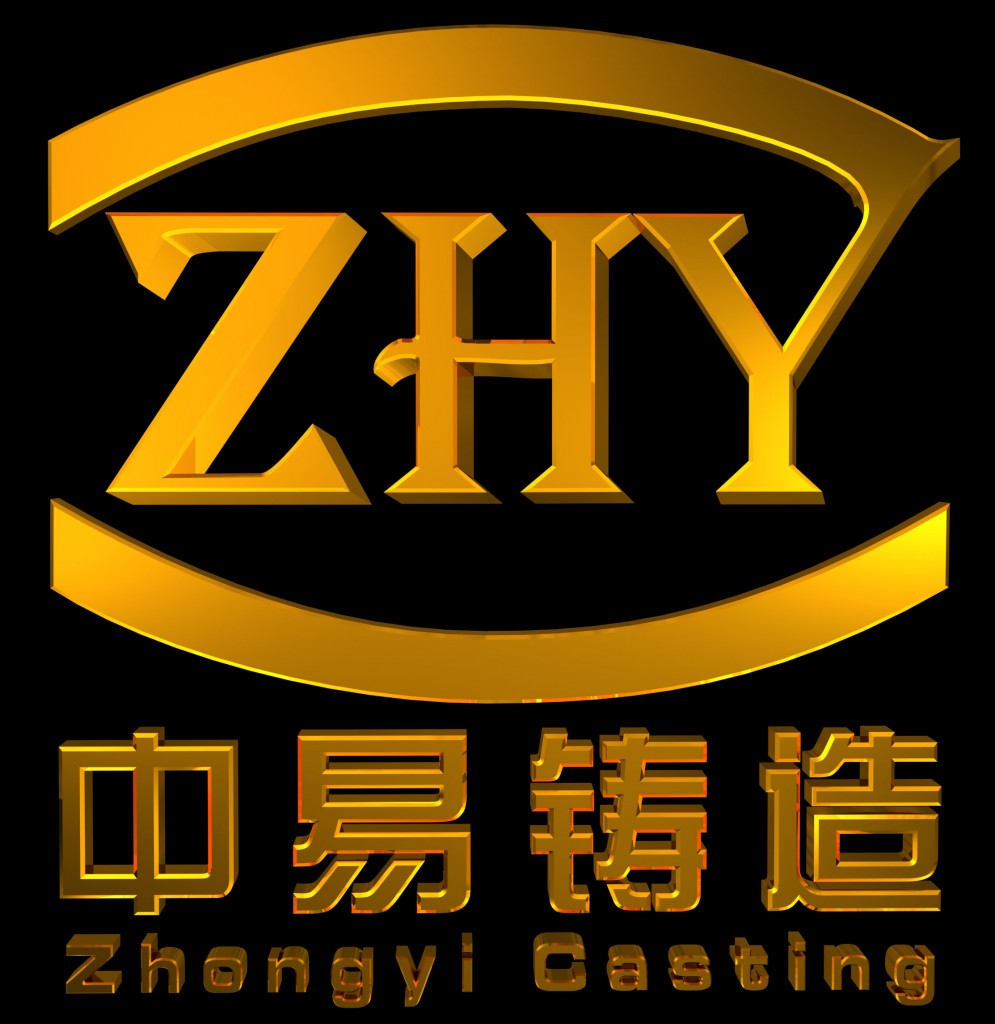
On the 20th, ZHY Casting, which focuses on sand casting, raised funds mainly for “High end Casting Equipment Production Line Technology Transformation Project”, “Green Intelligent Technology Transformation Project of Light Alloy Parts Production Line”, “New R&D Center Project”, and supplementing working capital.
Core business positioning: High end business performance continues to grow
Since its establishment, ZHY Casting has focused on the field of sand casting, implementing a development strategy of “strengthening casting equipment, expanding casting production, and providing precision casting services”. With high-end core making equipment and high-quality aluminum alloy castings as its two major businesses, ZHY Casting provides customers with efficient and intelligent core making equipment, as well as research and manufacturing of casting products. It is committed to leading and promoting technological updates and industrial upgrading in China’s casting industry, empowering the green and intelligent development of the casting industry.
Core making equipment is the core equipment of sand casting and the equipment foundation for the transformation and upgrading of the traditional casting industry. ZHY Casting’s core equipment products have a wide customer base and strong market influence. Sand casting manufacturers are the main manufacturers of high-end core making equipment for inorganic and cold core processes in China, and maintain long-term cooperative relationships with well-known enterprises such as Yunnei Power, China National Heavy Duty Truck, Weichai Power, Guangxi Yuchai, and FAW Casting. The core making equipment products of sand casting manufacturers have been exported to France, Mexico, Serbia, Türkiye and other countries and regions, directly participating in the international market competition.
The casting business of sand casting manufacturers is positioned as high-end products, facing the international market. Based on the equipment business foundation, they have built automated and intelligent casting workshops to provide customers with “high difficulty, high quality, and high precision” casting production and manufacturing services. Sand casting manufacturers use precision core casting technology, combined with material application technology, core making and assembly technology, industrial robot technology, visual recognition technology, laser online monitoring and information technology, to develop a green automated production system for castings, build an efficient and intelligent workshop, and achieve high-quality aluminum alloy casting automation production. The second casting workshop independently designed and built by sand casting manufacturers has been awarded the first batch of green factory titles by the Ministry of Industry and Information Technology. Sand casting manufacturers have formed long-term and stable cooperative relationships with major HVAC groups such as Weineng, Sidrui, Ideal, as well as automotive or rail transit component manufacturers such as Yunnei Power, Knorr, and Westinghouse Brakes. ZHY Casting’s two core businesses have strong market competitiveness and actively expand into international markets, resulting in sustained growth in business performance.
R&D innovation driven development with technological advantages leading the industry
ZHY Casting drives enterprise development through research and development innovation. After years of technological accumulation and research and development investment, sand casting manufacturers have formed a core technology system with independent intellectual property rights in key areas of sand casting, such as sand shooting control, sand core solidification, precision core assembly, intelligent control systems for core making equipment, and low-pressure filling. Mainly manifested as: multidisciplinary and multi domain research and development, technological systematization; Integration, innovation, and coordinated development of equipment technology and casting process technology; Developing original technologies and processes to achieve a transition from “following” to “leading”; Capable of developing both hardware technology and operating system software.
ZHY Casting, through continuous research and innovation, has mastered multiple core technologies in the fields of casting materials, processes, and equipment, committed to solving the major problems of transformation and upgrading of traditional casting enterprises and achieving engineering applications. As of now, sand casting manufacturers have 167 patents, including 82 invention patents, 83 utility model patents, and 2 design patents, widely used in equipment and casting business of sand casting manufacturers. The relevant technologies of sand casting manufacturers have been deeply integrated with the casting industry and have achieved good market performance. During the reporting period, the product revenue generated by core technologies accounted for over 90%.
After years of development, the sand casting manufacturers have become a national high-tech enterprise and has been awarded the titles of “Enterprise Technology Center”, “Precision Core Casting Process and Complete Equipment Engineering Technology Research Center”, and has a “Postdoctoral Research Workstation”. The sand casting manufacturers have undertaken 3 national and ministerial level scientific research projects and 3 provincial-level scientific research projects. The precision core molding production line of sand casting manufacturers have been awarded the “Outstanding Product of the Mechanical Industry for the 40th Anniversary of Reform and Opening up”, the MiCC300 integrated core making unit has won the “National Casting Equipment Innovation Award”, and the Inorganic Core Shooting Machine (MWD) has been rated as the first major equipment product in Jiangsu Province.
Continuous growth in market size, broad prospects for transformation and upgrading
Benefiting from the widespread application of sand casting technology, the market size of core making equipment continues to grow. China’s casting production has consistently ranked first in the world for many years. As the most widely used casting process, sand casting has brought a large demand for sand casting specialized equipment such as core making equipment. Sand casting is currently the main production process in the foundry industry, and it is expected to continue to be widely used in the next 10 to 20 years.
The market size of China’s chip making equipment is relatively large, but it is mostly mid to low-end products produced by small and medium-sized enterprises. Foreign manufacturers still occupy a certain market share in the high-end product market, and the competitiveness of domestic high-end chip making equipment is relatively weak. With the country’s demand for “independence, controllability, and reliability” in the equipment manufacturing industry, the market share of domestically produced high-end core making equipment with excellent performance, reliable quality, and high cost-effectiveness continues to grow. In the future, a few domestic enterprises with core technology and independent innovation capabilities will gradually increase their market share through product technology, cost, and localization advantages, and the trend of “import substitution” for high-end products will become increasingly apparent.
With the implementation of the policy of phasing out outdated casting capacity, China’s traditional casting industry, especially the traditional sand casting industry, is facing significant pressure for transformation and upgrading. The transformation and upgrading of the sand casting industry is driving the development of the core making equipment industry. Core making equipment, especially high-end core making equipment such as core making center, as a major fixed assets investment of downstream customers, has a high amount of early investment. If problems occur in the use process, it will directly affect the quality of products produced and the continuity of production activities. Therefore, downstream customers of high-end core making equipment are currently mainly concentrated in large casting enterprises with strong financial strength, large scale, and high risk resistance.
With the improvement of performance parameters of downstream equipment products, aluminum alloy castings are showing a trend of “high quality” in precision, complexity, and thin-walling, and the production capacity of high-end castings is gradually being released. Automobile is an important application field of aluminum alloy castings, and lightweight automobile has become a future development trend in the automotive industry. Automobile lightweighting is achieved through casting material modification and process reform, improving casting accuracy, reducing casting wall thickness, and reducing casting quality.
Driven by the policy of phasing out outdated production capacity and upgrading traditional tidal sand technology, downstream foundry manufacturers will continue to release their demand for new processes and high-end core making equipment procurement. With the continuous deepening of “import substitution”, downstream foundry manufacturers have increased their trust in domestic high-end core making equipment. Sand casting manufacturers have been engaged in the research and production of casting products for nearly 20 years, possessing independent intellectual property rights and continuous innovation capabilities in core technology. High end core making equipment products have global competitiveness, and have provided core making equipment and services to multiple large domestic casting manufacturers, accumulating high customer reputation and establishing significant competitive advantages. Driven by the aforementioned opportunities and advantages, sand casting manufacturers have broad prospects for the future development of their equipment business.
Sand casting manufacturers have long focused on the research and industrialization of precision core casting technology, building intelligent, green, and high-quality casting production workshops, achieving automated and intelligent production of castings. Sand casting manufacturers adhere to a high-end positioning in their casting business, and their casting products are characterized by complex design, high process difficulty, and high precision. They have established long-term and stable cooperative relationships with multiple well-known domestic and foreign customers. With the lightweighting of automobiles and the elimination of outdated domestic casting capacity, the aluminum alloy casting market, especially the high-quality aluminum alloy casting market, will continue to grow. The development prospects of the aluminum alloy casting business market for sand casting manufacturers are broad.
The funds raised by ZHY Casting’s listing on the Science and Technology Innovation Board are mainly invested in three construction projects, namely the “High end Casting Equipment Production Line Technology Renovation Project”, the “Green and Intelligent Technology Renovation Project of Light Alloy Parts Production Line”, and the “New R&D Center Project”. The fundraising construction project is closely related to the core technology of sand casting manufacturers and enhances the development of existing businesses. Among them, high-end equipment projects can improve the production capacity and product quality of sand casting manufacturers’ high-end core making equipment business; The casting project can improve the output and production efficiency of high-quality aluminum alloy casting business for sand casting manufacturers, green intelligent manufacturing level, and reduce production costs; The R&D center project can improve the existing R&D system, enhance R&D capabilities, enhance the market competitiveness of existing businesses, and ensure the sustainable development of sand casting manufacturers.
In the future, ZHY Casting will seize the opportunities of the country’s vigorous development of high-end equipment manufacturing industry and the promotion of the implementation of the “green casting” concept through a series of business plans such as equipment and process upgrade plans, R&D and innovation plans, talent introduction and training plans, and financing plans. Through capital market financing, the company will expand its business scale, further consolidate and enhance the competitive advantages of high-end core making equipment and high-quality aluminum alloy castings for sand casting manufacturers in domestic and international markets, achieve the sustainable development of sand casting manufacturers, and maximize the interests of all shareholders.