With the rapid development of aviation manufacturing industry in recent years, large-scale precision titanium alloy castings are more and more favored by designers due to their high overall size accuracy, good stiffness, light weight and high stability.
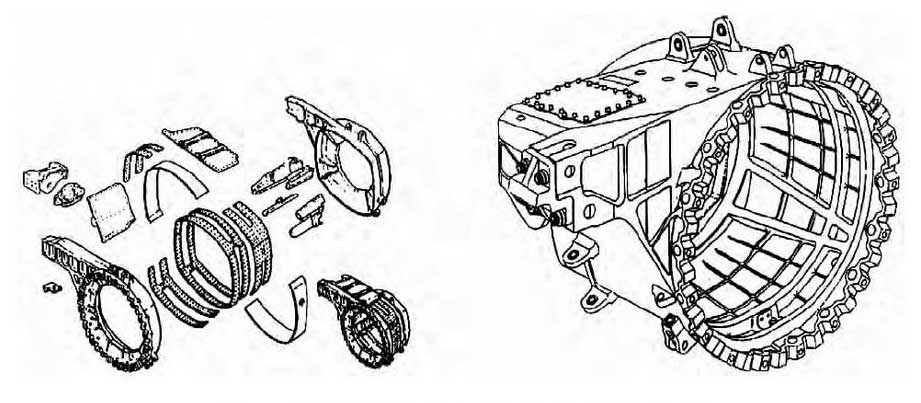
In the bell Boeing V-22 helicopter drive system, Howmet and Bell Helicopter replaced the components made of 43 aluminum alloy forgings and 536 fasteners with 3 titanium alloy integral precision castings and 32 fasteners, greatly reducing the quality of components, reducing the manufacturing cost by 30% and the manufacturing cycle by 62%. The U.S. F-22 fighter uses a large number of titanium alloy precision castings in the vertical tail rudder actuator support and other key bearing parts, accounting for about 7.1% of its overall structural quality.
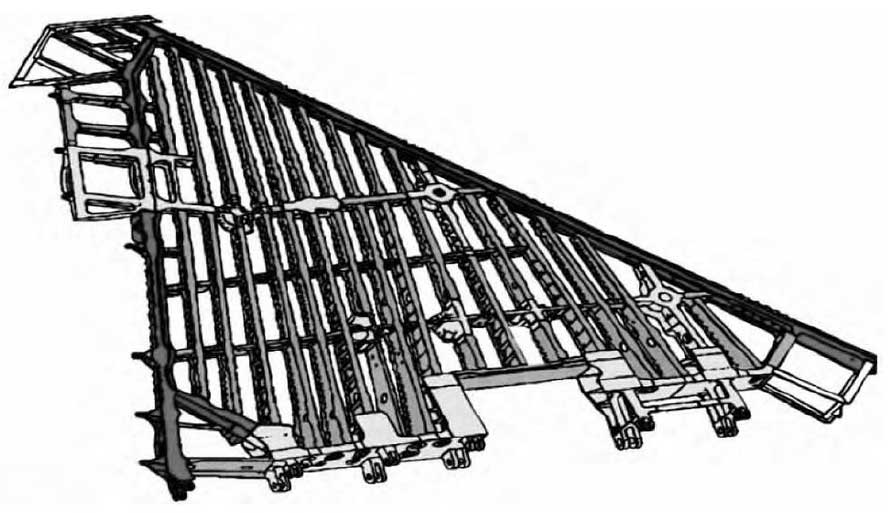
In the 1960s, the United States began the research of titanium alloy precision casting technology, and developed investment casting ceramic mold, machining graphite mold and hot isostatic pressing technology. Howmet company in the United States has been able to produce large-scale and complex thin-walled integral titanium alloy precision castings with a size of more than 400mm in 1984, and Ti Al company in Germany also has the production capacity of this technology in 1986 [19]. In the 1980s, PCC company of the United States manufactured GE90 engine fan hub with a diameter of 2000 mm. It is the largest titanium alloy precision casting in the world, with a casting dimension tolerance of ± 0.13 mm and a minimum wall thickness of 1.0-2.0 mm.
Since the end of 1970s, the research on titanium alloy casting and its forming process has been carried out in China. Through introducing foreign technology, digestion, absorption and technological innovation, the titanium alloy precision casting technology with partial independent intellectual property rights has been formed. ZTC4, ZTA7 and ZTA15 were studied and applied in the aviation casting of titanium alloy, and the technologies of machining graphite, ramming, special sand and many kinds of investment casting were developed and mastered successively, including graphite, tungsten surface ceramic and oxide ceramic.