In recent years, the development of nodular cast iron is very fast in our country. The proportion of nodular cast iron in the total amount of castings is increasing year by year. From 1998 to 2016, the output of middle-aged castings has increased nearly 9 times, and the proportion of the total output of castings has also increased from 14% to about 27%. In 2014, China’s total production of various castings reached 46.2 million tons, an increase of 3.8% over 2013. According to the analysis of material structure, the growth of nodular cast iron is 6.9%.
According to the data released by China Casting Association at the 2019 Casting Association meeting, the total output of all kinds of castings in China is 46.6 million tons, down 1.30% compared with that in 2018, which is the first time that the total amount of castings in China has a negative growth in more than ten years, but the growth of nodular iron castings is 1.61% according to the change of casting material structure.
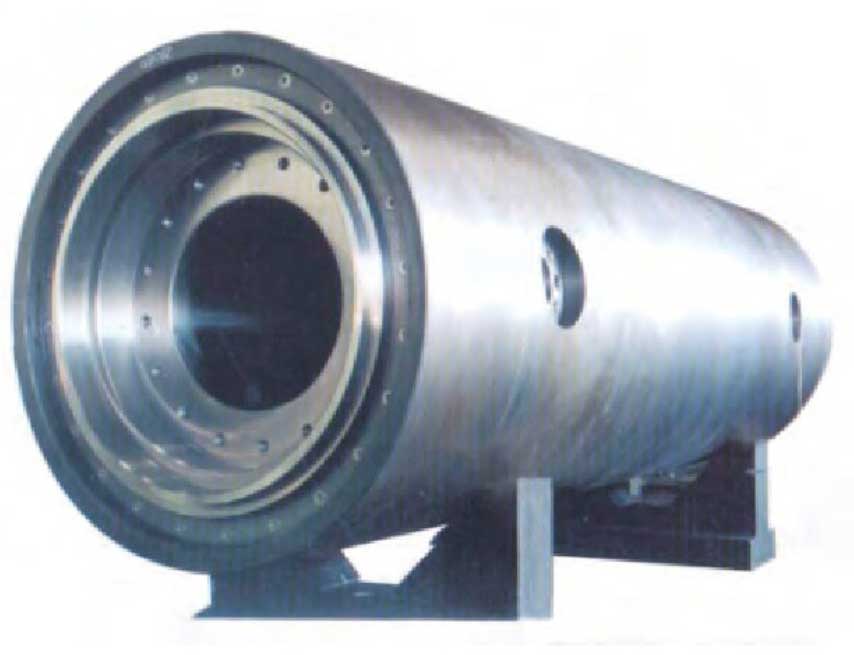
Therefore, more and more attention has been paid to the research of nodular cast iron. How to reasonably design the casting process, set the smelting parameters and produce high quality castings will become the main problem in the production process of ductile iron castings.
This paper introduces the application and research status of some advanced technologies at home and abroad, aiming at promoting the research and application of ductile iron casting technology.
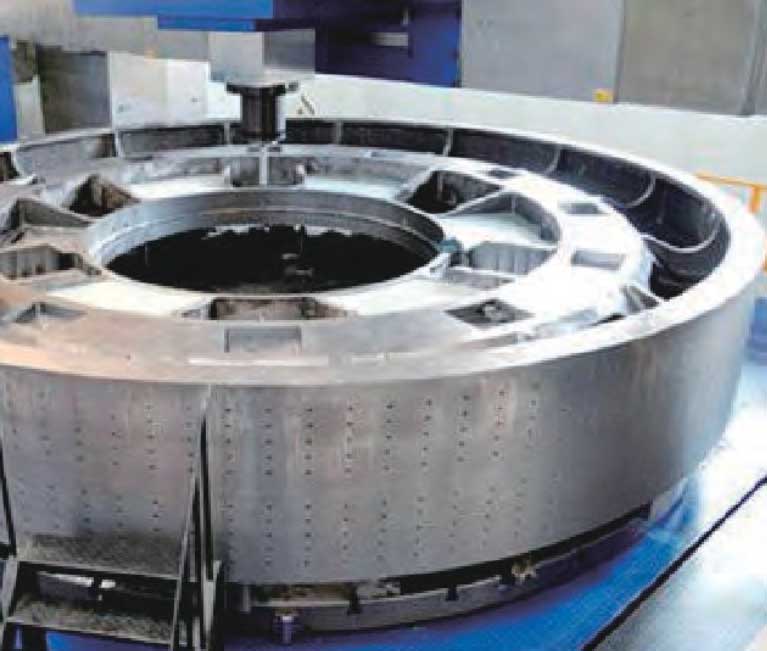
1. Production status
The production of nodular cast iron in some foreign developed countries has a high level of professional technology. For example, Siempelkamp company of Germany has achieved great success in the production of Nuclear Spent Fuel nodular cast iron storage and transportation vessel castings with complex structure, harsh technical conditions and poor environmental conditions (Figure 3). The size of the castings is φ 2500 mm × 5976 mm, the wall thickness is 400 mm, and the total mass is 115000 kg, Its production process control requirements are extremely strict, and it is the representative of the highest level of ductile iron castings in the world [4]. GE’s 6MW offshore wind power is the largest wind turbine product put into commercial operation in the world. The rotor casting (Figure 4) used has a diameter of 6900m m and a total mass of 40000 kg. It is a large rotating product with high difficulty and thin wall in the casting field. It is not only required to be free of structural defects, but also within the diameter range of 6900mm, the center deviation cannot exceed 15 μ M, The product has been trial produced in Italy, France and other factories, but it failed because of casting defects.
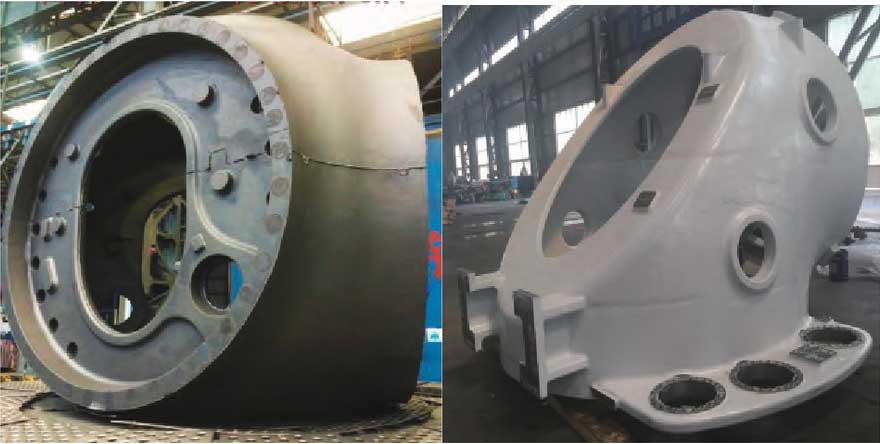
The domestic overall casting level is relatively backward, and the research and production of high-end ductile iron castings are still difficult, especially in raw materials and process control. At present, the production capacity of large-scale 100 ton ductile iron castings has not been formed. Several large-scale ductile iron casting manufacturers in China mainly focus on the research of wind power casting, such as ZHY casting. At the same time, some manufacturers have also made significant production and research results in the field of high-end ductile iron castings, such as heavy-duty gas turbine cylinder castings, marine diesel engine body castings, water pump frame castings, etc.
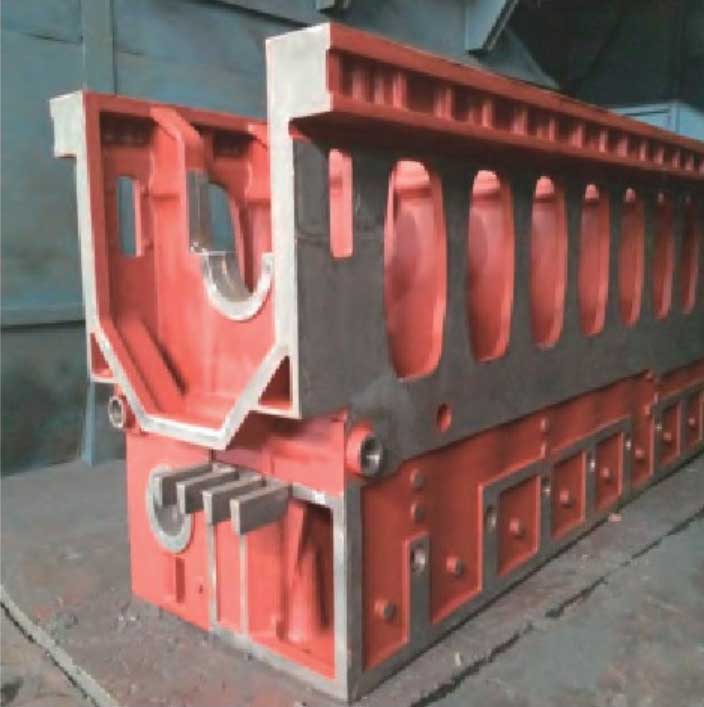
2. Technology research progress
At present, the development of ductile iron technology in China is in an important stage of focusing on casting quality, which is a period of expanding application scope and rapid growth of production [5]. The requirements and Research on the quality stability of nodular cast iron, such as low temperature impact, fatigue property, strength and toughness, are also constantly improving. From a large number of research results and production status, further research on the casting technology of nodular cast iron is needed in China.