Sandwich is a kind of iron-coated sand defect caused by excessive temperature of molten iron, insufficient fire resistance of coating, thin coating, insufficient fire resistance of molding sand, loose vibration of pattern and molding sand, etc.
1. Sample stage
140 When the flywheel housing is molded, a 110mm wide connection space is used between the two flywheel housings. Due to the cross-shaped deep hole (about 41mm deep, see Figure 1) on the side of the flywheel housing, it is difficult to fill the mold with sand, and the molten iron is easy to run during the lost foam casting of the flywheel housing. After immersion coating, it is necessary to manually plug the self-hardening sand. After comprehensive consideration, the station foot is selected as the water inlet point for manual combination of bottom injection, as shown in Figure 2. In order to ensure the air permeability during dip-coating, the dip-coating and drying shall be carried out with the top up. The simple flywheel shell vibration formula shall be used during molding. The cast flywheel shell shall have a good appearance in lost foam casting, and the size shall be accurate after processing and verification.
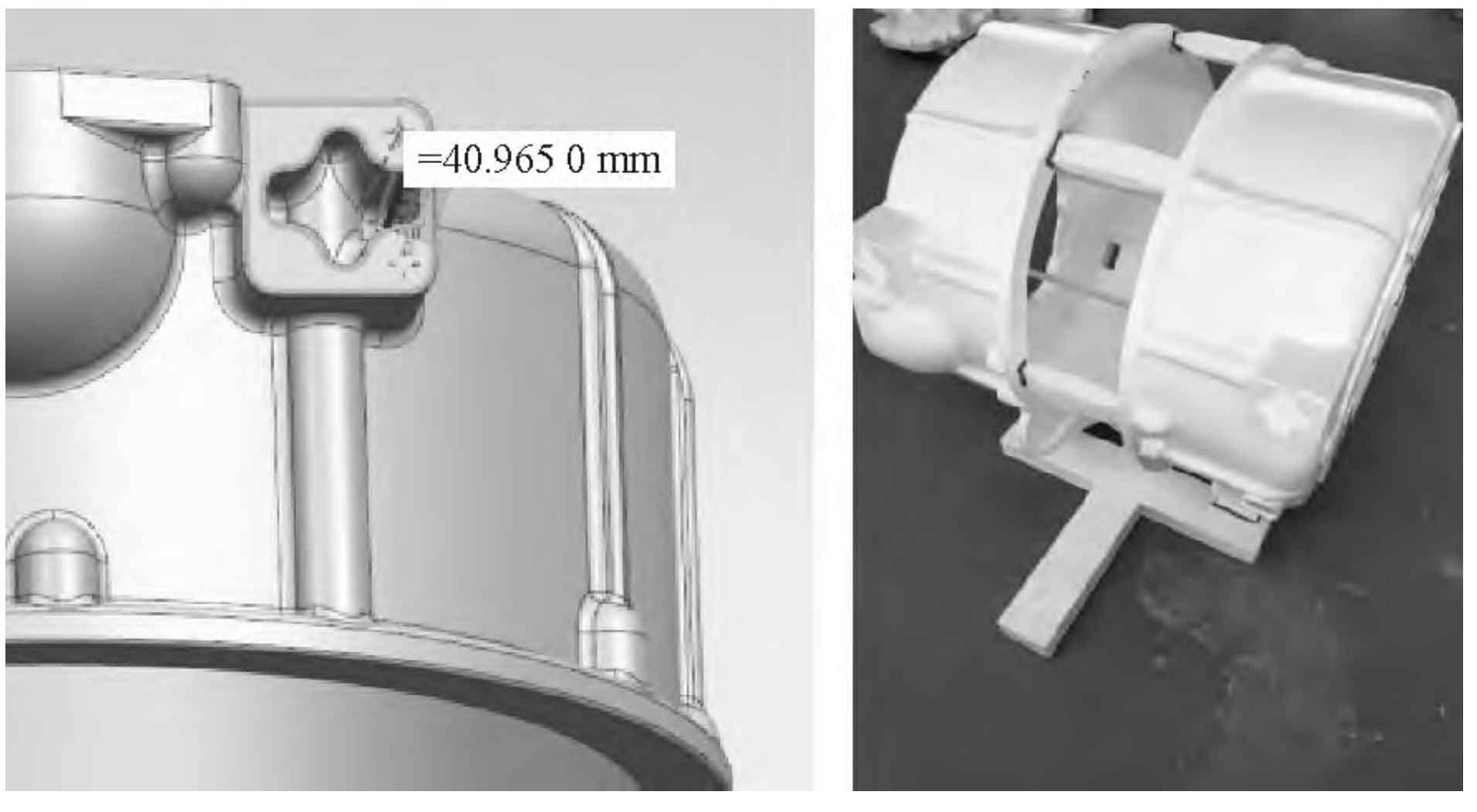
2. Small batch stage
In the small batch production stage, in order to improve the molding efficiency, on the premise that the size of the sand box is fixed, the distance between connecting points is shortened (from 110mm to 20mm) (see Figure 3) to achieve four pieces in a box (see Figure 4). Because the thickness of the 140 flywheel housing is 170mm (see Figure 5), the gap between the flywheel housing and between the flywheel housing and the sand box is reduced after the model cluster is removed from the sand box, and the difficulty of filling the molding sand in real time is increased. After the molding line is cleaned, the massive iron clips begin to appear on the top of the flywheel housing (see Figure 6), which is difficult to clean and easy to scrap.

After removing the factors such as coating, pouring temperature, negative pressure, etc., the blocky sandwich iron still exists when the coating is applied at the top; Subsequently, the method of coating repair+micro modification and compaction process is still invalid; Finally, the vibration compaction scheme was improved. After shot blasting, there was still a small piece of iron on the top (see Figure 7), which could only be removed manually.
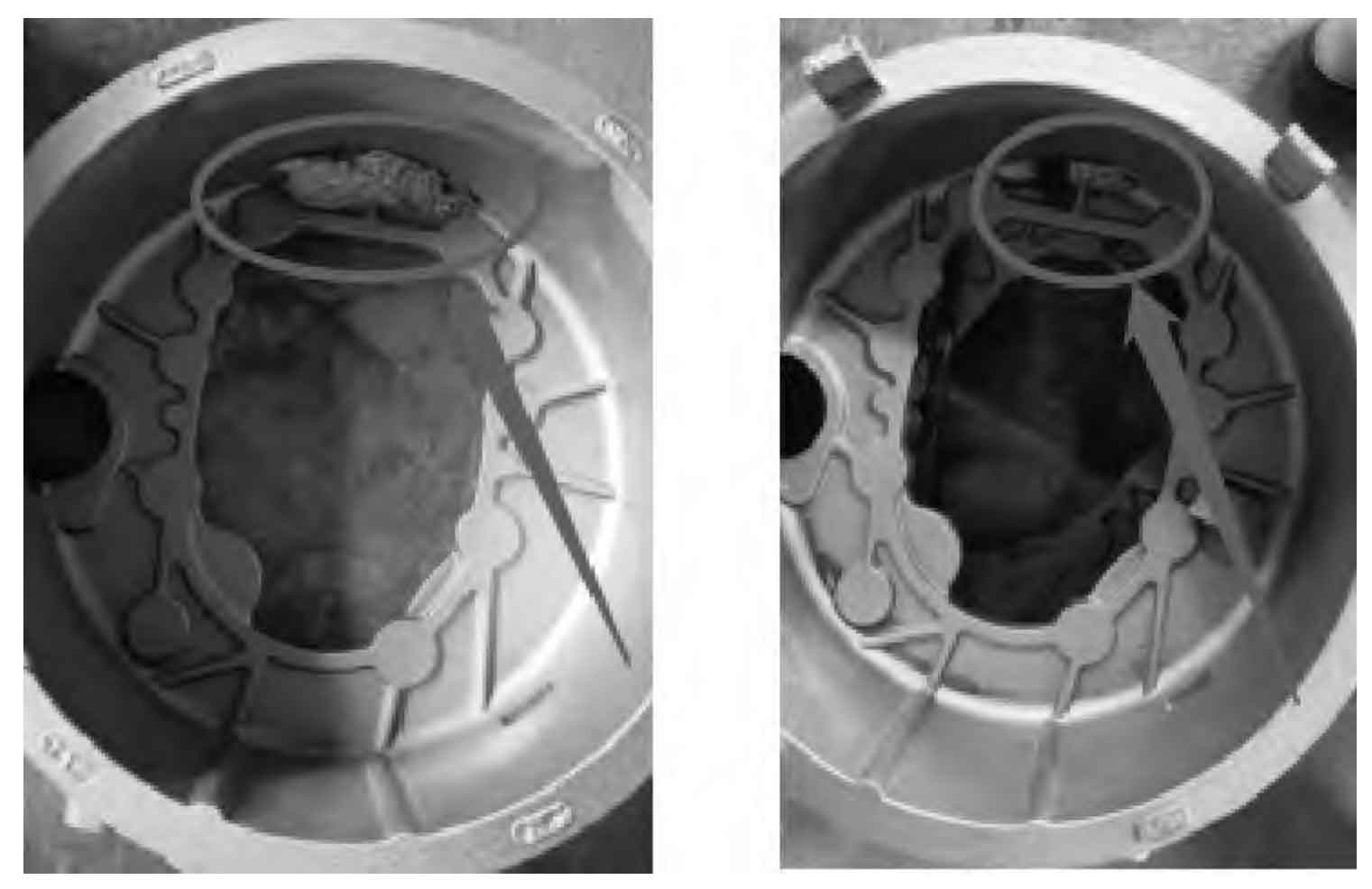
Finally, the analysis found that the coupling distance (connection point) of the flywheel housing was small, and the distance was expanded to 45mm (see Figure 8), and the iron defect was eliminated. However, it is easy to get stuck when the hydraulic separator separates the pouring system of the lost foam casting of the flywheel housing from the body. Finally, the spacing of the connection points is adjusted to 50mm within the limit range of the sand box, which eliminates the iron clip and reduces the difficulty of cleaning the separation pouring system. Enlarge the connecting clearance of flywheel housing, increase the molding sand filling clearance, which is conducive to filling the mold cluster cavity with molding sand. The cleaned flywheel housing has good appearance quality and meets the processing standard.
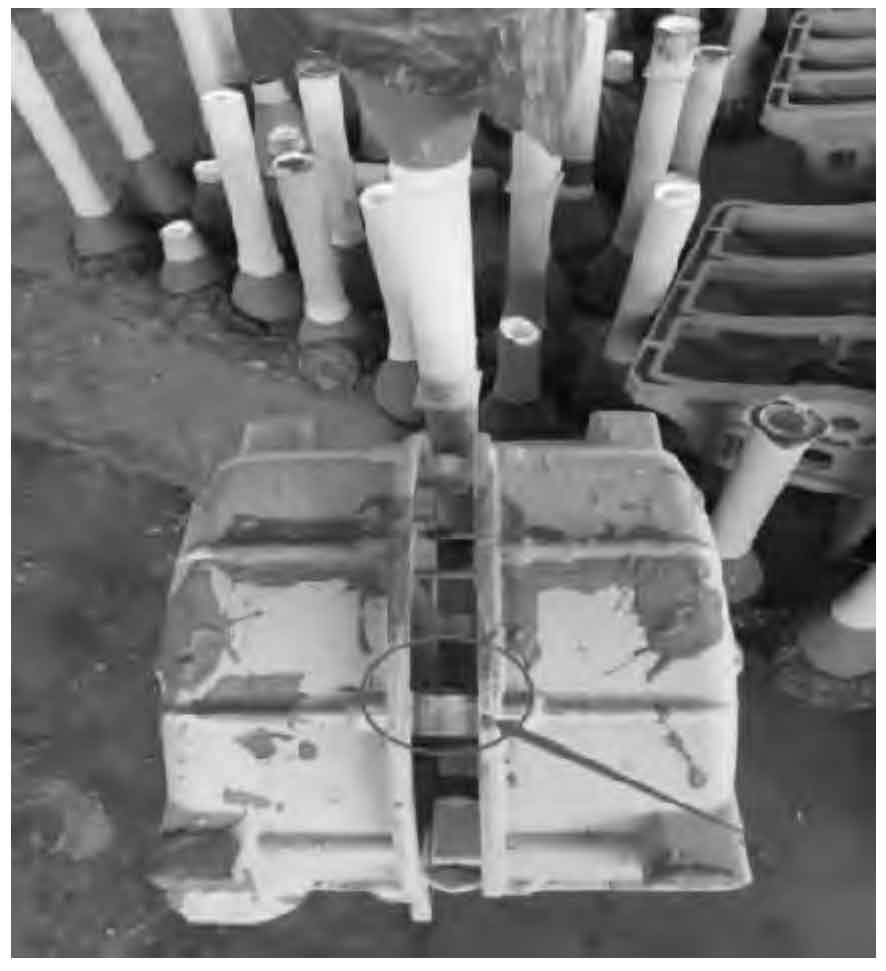