140 The flywheel housing is shown in Figure 1, with a mass of about 32kg and an overall dimension of 450mm × 450 mm × 230mm, wall thickness 11mm, material HT250. The size area of this casting is large and easy to deform. In the existing process, the size of water inlet is 50mm (long) × 30mm high × 6 mm (wide), hot metal outlet temperature is 1460~1470 ℃, pouring temperature is 1450~1460 ℃, vacuum degree is – 0.025 MPa, no film covering, no pressure maintaining, main defects are box lifting and iron clamping at the top of flywheel housing, and the scrap rate is about 40%.
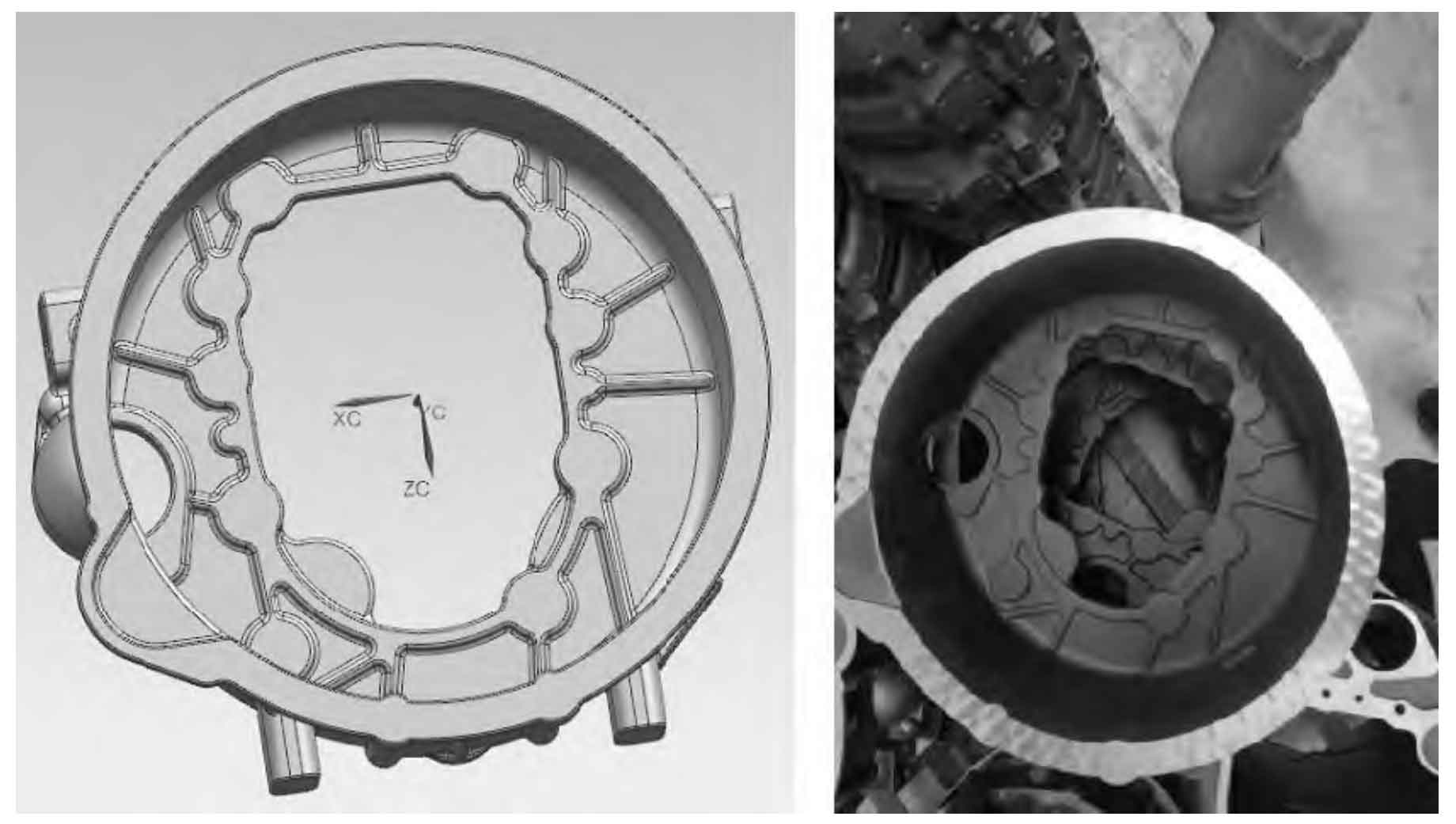
The wall thickness of the flywheel housing is large, so the negative pressure control is very important during the lost foam casting. In addition, the filter screen at the bottom of the sand box is gradually blocked with the increase of the number of production cases, which will have a great impact on the vacuum degree in the lost foam casting. The low vacuum in the sand box, the early closing of the vacuum after the pouring of thick and large parts, and the small amount of sand above the model will cause the casting to have the defects of lifting the box. After lifting the case, the top of the flywheel housing was deformed, and the circular seam was extruded into an ellipse (see Figure 2). The roundness dimension of the seam after machining was out of tolerance, resulting in scrapping. In order to ensure production efficiency, film covering is not considered. Pour in the way that the vacuum degree is turned to the maximum (vacuum does not bleed), hold the pressure for 60s, and the result is still lifting the box, and then extend the holding time to 90s, and the defects of lifting the box are eliminated. In order to improve the molding efficiency and ensure the production, the pressure holding time was reduced to 75s in combination with the process validation, and the result was still free of box lifting defects.