To stay ahead in the sand casting manufacturing industry, it is important to keep up with the latest trends and advancements. Here are some key trends that are shaping the industry:
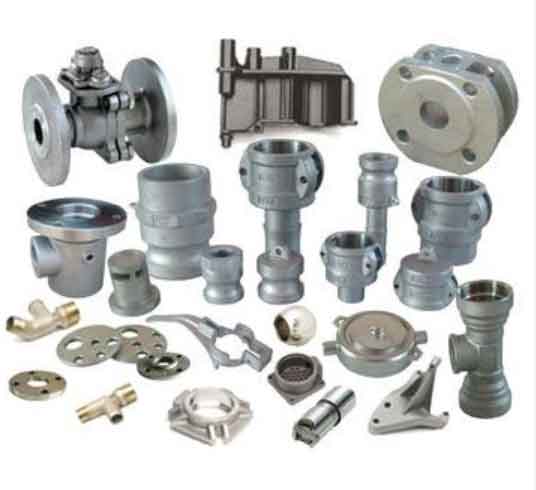
- Automation and Digitalization: Automation and digitalization are transforming sand casting manufacturing processes. Manufacturers are adopting advanced technologies such as robotics, computer-aided design (CAD), computer-aided manufacturing (CAM), and simulation software to improve efficiency, accuracy, and productivity. Automation streamlines processes, reduces human error, and enables faster production cycles.
- 3D Printing and Additive Manufacturing: 3D printing, also known as additive manufacturing, is gaining popularity in sand casting. It allows for the production of complex geometries with intricate details and internal features that would be challenging or impossible to achieve with traditional methods. 3D printing also enables rapid prototyping and reduces lead times, making it an attractive option for custom and low-volume production.
- Green Sand Casting: Environmental sustainability is a growing concern in the manufacturing industry. Green sand casting focuses on using environmentally friendly materials, optimizing energy consumption, and reducing waste. Manufacturers are adopting sustainable practices such as recycling sand, implementing efficient cooling systems, and minimizing emissions to reduce their environmental impact.
- Simulation and Virtual Prototyping: Simulation software plays a crucial role in optimizing sand casting processes. Manufacturers use simulation tools to analyze and predict the behavior of molten metal, flow patterns, solidification, and shrinkage during the casting process. Virtual prototyping allows for the identification and correction of potential defects before physical production, saving time and resources.
- Improved Sand Casting Materials: Advances in sand casting materials are expanding the possibilities for stronger, lighter, and more durable castings. Manufacturers are exploring the use of new alloys, including high-strength steels, aluminum alloys, and metal matrix composites, to meet the demands of various industries. These materials offer enhanced mechanical properties, corrosion resistance, and better performance in extreme conditions.
- Quality Control and Inspection Technologies: Quality control is a critical aspect of sand casting manufacturing. Manufacturers are adopting advanced inspection technologies such as X-ray and CT scanning, ultrasonic testing, and 3D coordinate measuring machines (CMM) to ensure the dimensional accuracy, integrity, and quality of castings. These technologies enable comprehensive inspections, non-destructive testing, and precise measurement of complex geometries.
- Lean Manufacturing and Continuous Improvement: Lean manufacturing principles and continuous improvement methodologies are being applied to sand casting processes. Manufacturers are focusing on waste reduction, optimizing process flows, implementing efficient work cells, and adopting just-in-time (JIT) production strategies. These initiatives aim to minimize lead times, reduce costs, and improve overall operational efficiency.
- Collaboration and Co-creation: Collaboration between sand casting manufacturers, customers, and suppliers is becoming increasingly important. Manufacturers are working closely with customers during the design phase to provide input on manufacturability, material selection, and cost optimization. Co-creation approaches foster innovation, improve product performance, and ensure that castings meet specific application requirements.
By staying informed about these trends and actively embracing new technologies and practices, sand casting manufacturers can enhance their competitiveness, improve efficiency, and deliver high-quality castings to meet the evolving needs of their customers.