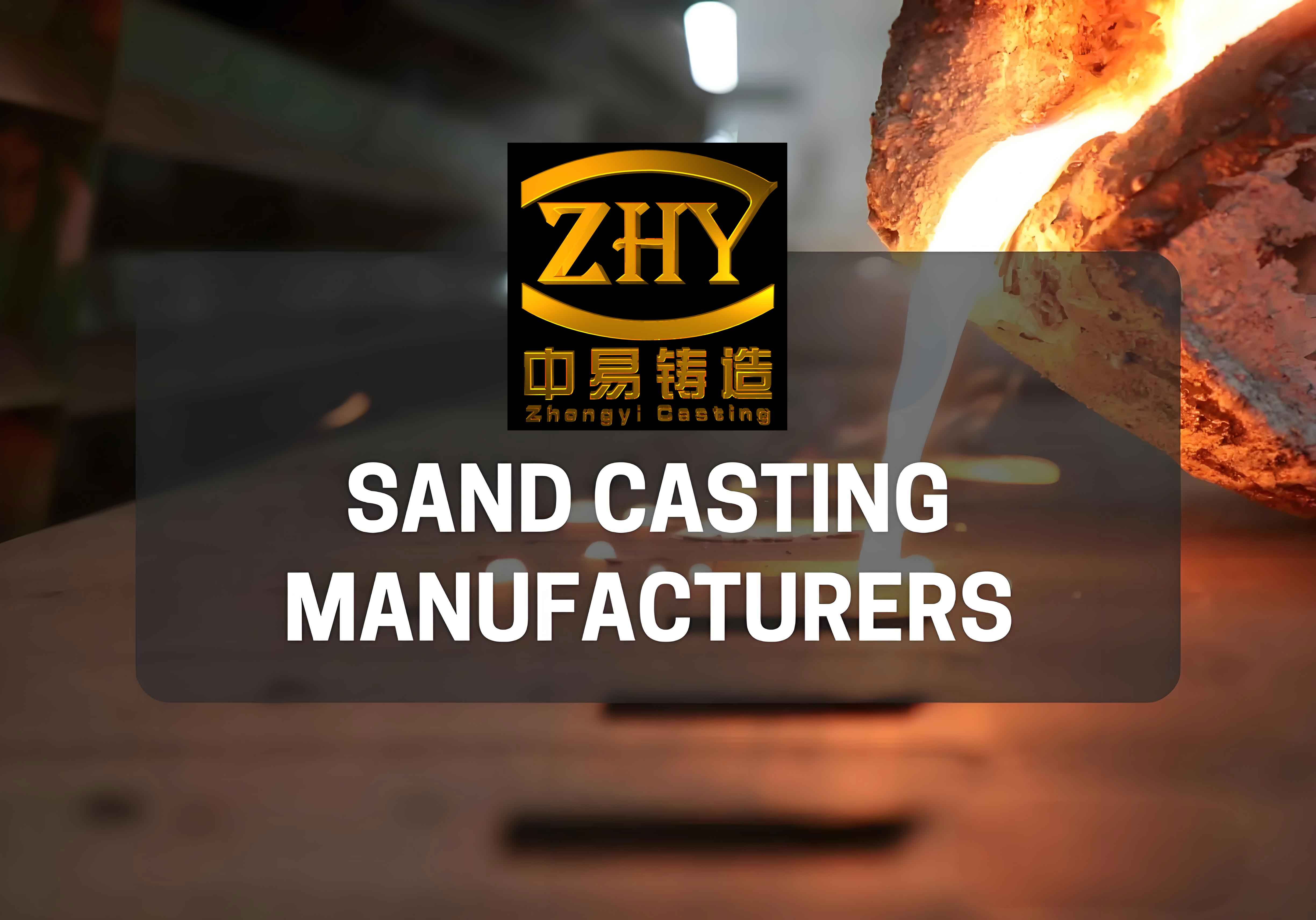
Choosing the right sand casting manufacturer is crucial for ensuring the quality, efficiency, and cost-effectiveness of your products. To make an informed decision, it’s essential to evaluate potential sand casting manufacturers based on specific key metrics. These metrics provide insights into the manufacturer’s capabilities, quality standards, production efficiency, and overall reliability. This article outlines the key metrics for assessing sand casting manufacturers and provides guidance on how to use these metrics effectively.
Key Metrics for Assessing Sand Casting Manufacturers
1. Quality Metrics
Quality is a paramount consideration when assessing sand casting manufacturers. The quality of the castings directly impacts the performance and durability of the final products.
Common Quality Metrics
- Defect Rate: The percentage of castings that have defects.
- Surface Finish Quality: The smoothness and uniformity of the casting surface.
- Dimensional Accuracy: The degree to which the castings meet specified dimensions and tolerances.
- Material Integrity: The absence of internal defects such as porosity, inclusions, and shrinkage.
Table 1: Quality Metrics
Metric | Description | Importance |
---|---|---|
Defect Rate | Percentage of defective castings | Indicates overall quality control |
Surface Finish Quality | Smoothness and uniformity of casting surface | Affects aesthetic and functional aspects |
Dimensional Accuracy | Adherence to specified dimensions and tolerances | Ensures parts fit and function correctly |
Material Integrity | Absence of internal defects | Ensures structural integrity and performance |
2. Production Efficiency Metrics
Production efficiency metrics help evaluate the sand casting manufacturer’s ability to produce castings in a timely and cost-effective manner.
Common Production Efficiency Metrics
- Cycle Time: The time required to complete one production cycle.
- Yield Rate: The percentage of castings produced that meet quality standards on the first attempt.
- Lead Time: The time from order placement to delivery.
- Utilization Rate: The percentage of available production capacity being utilized.
Table 2: Production Efficiency Metrics
Metric | Description | Importance |
---|---|---|
Cycle Time | Time to complete one production cycle | Affects production speed and throughput |
Yield Rate | Percentage of first-pass quality castings | Indicates efficiency and waste reduction |
Lead Time | Time from order placement to delivery | Affects customer satisfaction and scheduling |
Utilization Rate | Percentage of production capacity used | Indicates efficiency and potential for scaling |
3. Cost Metrics
Cost metrics provide insights into the financial aspects of working with a sand casting manufacturer, including pricing, cost-effectiveness, and value for money.
Common Cost Metrics
- Unit Cost: The cost to produce one casting.
- Total Cost of Ownership (TCO): The total cost associated with purchasing, using, and maintaining the castings over their lifecycle.
- Cost Variance: The difference between estimated and actual costs.
- Return on Investment (ROI): The financial return from using the sand casting manufacturer’s services.
Table 3: Cost Metrics
Metric | Description | Importance |
---|---|---|
Unit Cost | Cost to produce one casting | Affects pricing and profitability |
Total Cost of Ownership | Total lifecycle cost of the castings | Provides a comprehensive cost perspective |
Cost Variance | Difference between estimated and actual costs | Indicates accuracy of cost estimations |
Return on Investment | Financial return from the manufacturer’s services | Measures financial benefit and value |
4. Capability Metrics
Capability metrics assess the technical and operational capabilities of the sand casting manufacturer, including their ability to meet specific requirements and handle complex projects.
Common Capability Metrics
- Material Range: The variety of materials the manufacturer can work with.
- Casting Size Range: The range of sizes and weights the manufacturer can produce.
- Complexity Handling: The manufacturer’s ability to produce complex geometries and intricate designs.
- Technology and Equipment: The availability and condition of advanced casting technologies and equipment.
Table 4: Capability Metrics
Metric | Description | Importance |
---|---|---|
Material Range | Variety of materials the manufacturer can handle | Indicates flexibility and ability to meet diverse needs |
Casting Size Range | Range of sizes and weights that can be produced | Ensures the manufacturer can handle specific project requirements |
Complexity Handling | Ability to produce complex geometries and designs | Important for projects requiring high precision and detail |
Technology and Equipment | Availability of advanced technologies and equipment | Indicates the manufacturer’s ability to deliver high-quality and efficient production |
5. Customer Service Metrics
Customer service metrics evaluate the sand casting manufacturer’s responsiveness, communication, and overall customer support.
Common Customer Service Metrics
- Response Time: The time taken to respond to inquiries and issues.
- Problem Resolution Rate: The percentage of issues resolved satisfactorily.
- Customer Satisfaction: Feedback and ratings from customers.
- After-Sales Support: The level of support provided after delivery.
Table 5: Customer Service Metrics
Metric | Description | Importance |
---|---|---|
Response Time | Time taken to respond to inquiries and issues | Affects customer experience and satisfaction |
Problem Resolution Rate | Percentage of issues resolved satisfactorily | Indicates the effectiveness of customer support |
Customer Satisfaction | Feedback and ratings from customers | Reflects overall customer experience |
After-Sales Support | Level of support provided after delivery | Important for long-term customer relationships |
6. Sustainability Metrics
Sustainability metrics assess the sand casting manufacturer’s commitment to environmentally friendly practices and social responsibility.
Common Sustainability Metrics
- Energy Efficiency: The efficiency of energy use in production processes.
- Waste Management: The effectiveness of waste reduction, recycling, and disposal practices.
- Carbon Footprint: The total greenhouse gas emissions from production activities.
- Compliance with Environmental Regulations: Adherence to local, national, and international environmental standards.
Table 6: Sustainability Metrics
Metric | Description | Importance |
---|---|---|
Energy Efficiency | Efficiency of energy use in production | Reduces operational costs and environmental impact |
Waste Management | Effectiveness of waste reduction and recycling | Ensures sustainable and responsible operations |
Carbon Footprint | Total greenhouse gas emissions | Reflects environmental impact |
Compliance with Environmental Regulations | Adherence to environmental standards | Ensures legal compliance and sustainable practices |
How to Use These Metrics Effectively
Define Your Priorities
Different projects may prioritize different metrics. Define what is most important for your project – whether it’s quality, cost, capability, customer service, or sustainability – and focus on those metrics.
Create a Balanced Scorecard
Develop a balanced scorecard to evaluate sand casting manufacturers against a range of key metrics. This approach provides a comprehensive view of their performance and capabilities.
Conduct Regular Reviews
Regularly review and update your assessment criteria and metrics to ensure they remain relevant to your evolving needs and industry standards.
Involve Cross-Functional Teams
Involve teams from different functions such as engineering, procurement, and quality assurance in the evaluation process to get diverse perspectives and comprehensive assessments.
Use Data-Driven Decisions
Leverage data and analytics to make informed decisions. Quantitative metrics provide objective insights that can guide your selection process.
Table 7: Steps to Use Metrics Effectively
Step | Action | Importance |
---|---|---|
Define Priorities | Identify the most important metrics for your project | Ensures focus on critical aspects |
Create Balanced Scorecard | Develop a comprehensive evaluation tool | Provides a holistic view of manufacturer performance |
Conduct Regular Reviews | Review and update assessment criteria | Keeps the evaluation relevant and accurate |
Involve Cross-Functional Teams | Engage multiple teams in the evaluation process | Ensures diverse perspectives and thorough assessments |
Use Data-Driven Decisions | Utilize quantitative data for decisions | Enhances objectivity and accuracy in selection |
Conclusion
Assessing sand casting manufacturers using key metrics is essential for making informed decisions that align with your project requirements and business objectives. By focusing on quality, production efficiency, cost, capability, customer service, and sustainability metrics, you can comprehensively evaluate potential manufacturers and choose the best partner for your needs. Regular reviews and a data-driven approach will further enhance your decision-making process, ensuring long-term success and high-quality outcomes in your sand casting projects.