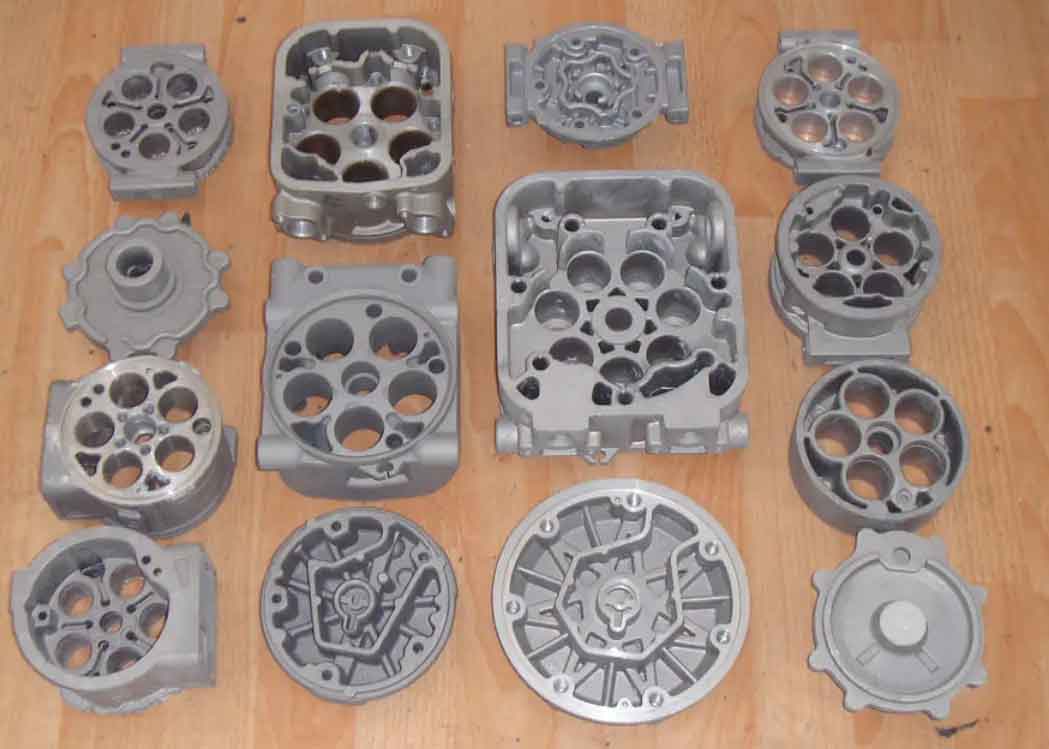
Because the equipment is the core platform for implementing the process, and the composite squeeze casting method is quite different from the traditional squeeze casting method, which also makes it difficult for the existing squeeze casting equipment to realize the composite squeeze casting method. Therefore, the composite squeeze casting equipment must be designed according to the requirements of the composite squeeze casting method and the technical level of the existing squeeze casting equipment. As the object of composite squeeze casting is a large part, the following key technical problems need to be solved in the overall design:
1.Large volume molten liquid transportation (determine mold filling temperature)
Since large parts require a large amount of molten metal, in order to ensure the quality of molten metal, the contact between molten metal and air must be reduced as much as possible to avoid oxidation. At the same time, due to the large amount of infusion, the quantitative requirements for molten liquid are relatively high.
The method to solve the quantitative transportation of large volume molten liquid and reduce oxidation is to let the molten metal be transported in the closed pipe, and at the same time, realize the mold pre closing before mold filling. Mold pre closing means that the mold is closed in a state close to the forming size of the casting, and the extrusion stroke of the mold to the molten metal only reserves the reduction of the cavity volume required by the solidification shrinkage of the molten metal and a small amount of plastic deformation during the extrusion process, that is, the pressure surface of the mold to the molten metal is in full contact with the molten metal when the mold is filled, so that when the mold applies pressure, it can be immediately transmitted to the entire liquid level of the molten metal and maintain high static pressure, Ensure that the molten metal crystallizes and solidifies under high pressure to achieve the effects of strengthening feeding and densification and improving the formability of squeeze casting.
2.Large volume molten liquid filling (determine the filling speed)
Large parts have a large amount of molten metal for filling, but the filling speed of molten metal must be moderate. If the filling speed is too slow, the molten liquid entering the mold cavity will solidify prematurely, resulting in pressure difficulty or even failure to form; If the mold filling speed is too fast, the molten metal will easily appear turbulence, involve in gas and oxide skin, resulting in stress, cracks, bubbles, shrinkage porosity and other defects. In order to ensure that the molten metal can fill the mold cavity, the volume of molten metal filling will be slightly larger than that required by the casting. At the same time, some errors are inevitable during the transportation of large volume molten metal. Therefore, in addition to ensuring the stable filling of molten metal, it is also necessary to ensure the quantitative filling of molten metal.
3.Large volume molten liquid extrusion (determination of specific pressure)
The compound squeeze casting process uses the upper die of the die to squeeze the molten metal. Due to the large pressure area of large parts, the squeeze pressure of the equipment is relatively high. At the same time, after the completion of mold filling, it is necessary to quickly establish a high extrusion force on the molten metal in the mold cavity, and ensure that the uniform, effective and continuous extrusion force can be obtained on the whole pressure surface of the molten metal. At the same time of applying pressure to the upper die, the filling head must be able to maintain the position in the filling cavity, that is, the filling head has the function of passive pressing.