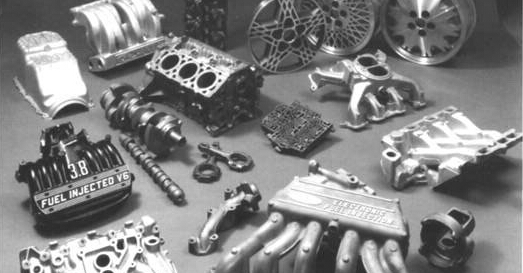
Lost wax casting is one of the glass forming processes. The main content is heating glass to a very high temperature so as to have certain flowability, then flowing into a pre-made shell mould for forming. By lost wax casting, complicated shape and exquisite handicrafts can be created.
Manufacturing Process and Characteristics
The main content is heating glass to a very high temperature so as to have certain flowability, then flowing into a pre-made shell mould for forming. As castings are formed by removing out of wax moulds on the shell moulds, it’s called as lost wax casting. As the glass contained with lead oxide (commonly known as synthetic quartz) features high refractive index like diamonds and high liquidity in high temperature, synthetic quartz is commonly used as one material for casting different glass types. In the current Chinese market, English crystal created by the said lost wax casting is generally called as coloured glaze.
Lost wax casting, also known as investment casting, is a traditional metal casting process that dates back thousands of years. It is used to create intricate and finely detailed metal objects, often for artistic or industrial purposes. The process involves several steps to produce high-quality, accurate, and complex metal parts.
- Pattern Creation: The first step is to create a pattern of the object that needs to be cast. This pattern can be made from various materials, such as wax, clay, plastic, or even metal. The pattern should be an exact replica of the desired final product.
- Assembly: The pattern is attached to a wax “sprue,” forming a wax tree. Multiple patterns can be attached to the same sprue, allowing multiple castings to be made in a single casting cycle.
- Investment Mold: The wax tree is then coated with a ceramic slurry, which gradually builds up layers to create a mold. This ceramic shell mold is also called the “investment.” The investment mold is usually created by dipping the wax tree into the slurry and then covering it with a fine refractory material like sand or stucco. This process is repeated several times to achieve the desired thickness and strength.
- Dewaxing: Once the investment mold is complete, it is heated in an oven or furnace. The high temperature melts and vaporizes the wax inside, leaving a hollow cavity within the ceramic mold that is an exact replica of the original wax pattern.
- Casting: The ceramic mold is preheated to ensure that it is ready to receive the molten metal. Molten metal is poured into the mold, filling the cavity previously occupied by the wax pattern. The metal fills in all the intricate details of the mold, reproducing the exact shape of the original pattern.
- Cooling and Solidification: After the metal is poured, the mold is allowed to cool and solidify. The metal takes the shape of the mold and forms the final casting.
- Mold Removal: Once the metal has cooled down and solidified, the ceramic mold is carefully broken away to reveal the metal casting inside. The sprue and any excess metal are removed, and the final casting is cleaned and finished to achieve the desired surface texture and appearance.
Lost wax casting is widely used in various industries, including jewelry making, art, aerospace, and engineering, to produce intricate and detailed metal components that are challenging or impossible to create through other manufacturing methods. The process allows for high precision and repeatability, making it a popular choice for creating complex metal objects.
The lost wax casting process stems from the development of varieties of ancient casting processes. In late neolithic pottery period, Chinese ancient craftsmen have widely applied lost wax casting in manufacturing bronze workings.