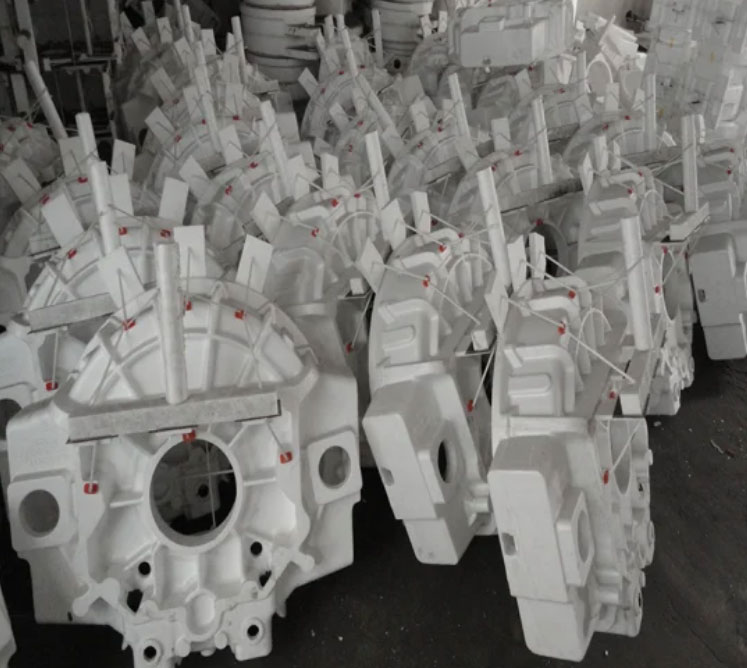
Lost foam casting, also known as evaporative pattern casting or full mold casting, is a modern casting process used to produce complex and intricate metal parts. In this comprehensive guide, we will explore the entire lost foam casting process, from pattern creation to the finished product.
1. Pattern Creation:
The lost foam casting process begins with the creation of a foam pattern. The pattern can be made using different methods:
- Manual Foam Cutting: Foam blocks are manually cut and shaped to match the desired part’s geometry.
- CNC Machining: Computer numerical control (CNC) machines can accurately mill foam patterns based on digital design data.
- 3D Printing: Additive manufacturing (3D printing) allows for the direct production of foam patterns from digital designs.
The foam pattern is a replica of the final part, including all intricate details and features.
2. Pattern Assembly:
Multiple foam patterns are assembled together to form a cluster or pattern tree. The pattern tree may contain several patterns attached to a common gating system, forming a single unit to be cast in one mold.
3. Pattern Coating:
The assembled pattern tree is coated with a refractory material or ceramic slurry. The coating adds strength to the foam pattern and creates a refractory shell around it.
4. Drying:
Once the coating is applied, the pattern tree is left to dry and harden. The drying process ensures that the refractory material forms a strong shell around the foam pattern.
5. Pre-Heating:
Before casting, the dried pattern tree is pre-heated to remove any remaining moisture and improve the casting’s surface finish.
6. Sand Molding:
The pre-heated pattern tree is placed inside a flask filled with unbonded sand. The sand used in lost foam casting is typically a mixture of fine and coarse sand with a binder.
7. Vacuum/Vibration Assisted Sand Compaction:
To achieve a tight packing of sand around the foam pattern, the flask may be subjected to vibration or vacuum to facilitate better sand compaction.
8. Metal Pouring:
Molten metal, usually aluminum or cast iron, is poured into the flask. The hot metal vaporizes the foam pattern, causing it to evaporate, leaving behind an empty mold cavity in the shape of the original pattern.
9. Solidification:
The poured metal cools and solidifies within the refractory mold cavity, taking the shape of the original foam pattern.
10. Cooling and Removal:
After solidification, the metal part is allowed to cool before being removed from the mold. The refractory shell is typically broken away to reveal the cast metal part.
11. Finishing and Quality Control:
The finished castings may require some post-processing, such as trimming or machining, to achieve the desired dimensional accuracy and surface finish. Quality control measures are employed to ensure that the castings meet the required specifications.
12. Recycling:
One of the eco-friendly aspects of lost foam casting is that the evaporated foam pattern can be captured and recycled, minimizing waste.
Lost foam casting offers several advantages, including the ability to cast complex shapes with fine details, reduced tooling costs, and minimal parting lines. However, the process requires precise control over the pattern coating and metal pouring to avoid defects like porosity or sand inclusions. With proper implementation and process control, lost foam casting can be an efficient and cost-effective method for manufacturing complex metal parts across various industries.