This article delves deep into the lost foam casting process, with a primary focus on the testing methods for molten metal filling ability. By analyzing the influencing factors, conducting experimental research on sample design and optimization, and introducing the design of sample molds, a comprehensive understanding of the topic is presented. The established testing method and designed samples can effectively measure the filling ability of molten metal in lost foam casting of cast iron parts, providing valuable guidance for optimizing the lost foam casting production process.
1. Introduction
Lost foam casting is a green casting production method that has gained significant attention in the casting industry. It uses polystyrene foam patterns, which vaporize under the high – temperature action of molten metal, ultimately forming castings. This method offers several advantages such as environmental friendliness, high casting accuracy, low cost, and reduced labor intensity. It has found extensive applications in various fields like agricultural machinery, automobiles, and power machinery.
However, compared to traditional cavity casting, the lost foam casting process has a relatively high scrap rate. Defects related to filling account for approximately 80% of all defects. Currently, there is a lack of a complete and accurate scientific method for optimizing the lost foam casting process and quantitative data on metal fluidity. The filling process in lost foam casting is significantly different from traditional cavity casting due to the complex physical and chemical reactions between the molten metal and the polystyrene foam pattern. While there are standard methods for testing the filling ability of molten metal in traditional cavity casting, no such method has been established for lost foam casting. This article aims to address this gap by researching the testing method for the filling ability of molten metal in lost foam casting of cast iron parts.
2. Influencing Factors Analysis in Lost Foam Casting Filling Process
2.1 Negative Pressure Degree
The negative pressure degree in the lost foam casting process serves two main functions. It gives the sand mold a certain strength to prevent box collapse and expansion, and it also enables the rapid removal of the decomposition products of the white mold from the cavity. Previous studies have shown that the filling speed in lost foam casting increases linearly with the increase of the negative pressure degree. That is, the greater the negative pressure degree, the faster the filling speed. However, its impact on the filling ability is not clearly defined. In the lost foam casting of cast iron parts, the commonly used negative pressure degree ranges from 0.03 to 0.06MPa. A summary of the relationship between negative pressure degree and filling speed is shown in Table 1.
Negative Pressure Degree (MPa) | Filling Speed Trend |
---|---|
0.03 – 0.06 | Increases linearly |
2.2 Pattern Density
The higher the density of the white mold pattern, the more decomposition products per unit volume of the white mold, which increases the resistance to the filling of the molten metal. For cast iron parts in lost foam casting, the commonly used pattern materials are EPS and STMMA. The density range of EPS is typically 20 – 25g/L, and the density of STMMA is generally controlled at 22 – 26g/L. Table 2 shows the relationship between pattern density and filling resistance.
Pattern Material | Density Range (g/L) | Filling Resistance Trend |
---|---|---|
EPS | 20 – 25 | Increases with density |
STMMA | 22 – 26 | Increases with density |
2.3 Pouring Temperature
Research indicates that as the pouring temperature increases in lost foam casting, the filling speed initially shows an upward trend. However, when the pouring temperature is further increased, the filling speed starts to decline. At lower pouring temperatures, as the temperature rises, the gasification speed of the foam plastic accelerates, reducing the filling resistance and increasing the filling speed. But when the pouring temperature reaches a certain level, the type of decomposition products of the foam plastic pattern changes. There is an increase in small – molecule decomposition products and a decrease in liquid and high – molecular – weight gaseous decomposition products. This leads to an increase in the amount of gas products in the gas gap in front of the molten metal, which cannot be discharged quickly, thus affecting the filling speed. In practical production, a high pouring temperature is often used to compensate for the heat absorbed by the decomposition of the white mold and improve the filling ability of the molten metal. However, for some thin – walled parts with complex structures, simply increasing the pouring temperature may not effectively improve the filling ability of the molten metal. The commonly used pouring temperature for cast iron parts in lost foam casting is 1480 – 1520°C. The relationship between pouring temperature and filling speed is presented in Table 3.
Pouring Temperature Range (°C) | Filling Speed Trend | Reason |
---|---|---|
Below a certain value (e.g., initial stage) | Increases | Accelerated gasification of foam plastic reduces filling resistance |
Above a certain value | Decreases | Change in decomposition product types increases gas in the gas gap |
2.4 Coating Permeability
The main function of the coating in lost foam casting is to isolate the molten metal from the sand mold to prevent sand adhesion. However, the coating permeability has a significant impact on the filling of the molten metal. A good coating permeability is beneficial for the discharge of the decomposition products of the white mold, reducing the gas pressure at the front end of the molten metal and increasing the filling speed. The coating permeability is closely related to the thickness of the coating layer and the number of coating applications. The greater the thickness of the coating layer and the more times it is applied, the worse the coating permeability. In the lost foam casting of cast iron parts, the commonly used coating is usually applied 2 – 3 times, with a coating thickness of 1 – 1.2mm. Table 4 shows the relationship between coating – related factors and permeability.
Coating Application Times | Coating Thickness (mm) | Coating Permeability Trend |
---|---|---|
2 – 3 | 1 – 1.2 | Decreases with more applications and greater thickness |
2.5 Static Pressure Head
Generally, the size of the static pressure head depends on the height of the sprue. Under the condition that other process parameters remain unchanged, the larger the static pressure head, the faster the filling speed.
3. Process Parameter Selection
To test the filling ability of molten iron under different pouring parameters, the main pouring parameters include pouring temperature, vacuum degree, pattern density, and coating permeability.
The pouring temperature can generally be set within the range of 1400 – 1500°C. The vacuum degree is usually set at 0.03 – 0.06MPa, the pattern density is 20 – 26g/L. Since the coating permeability is difficult to control in actual production, different coating application times (2 – 4 times) at the same Baume degree are used to represent different permeabilities. The static pressure head is replaced by different sprue heights according to the test requirements. Table 5 summarizes the process parameter ranges.
Process Parameter | Range |
---|---|
Pouring Temperature (°C) | 1400 – 1500 |
Vacuum Degree (MPa) | 0.03 – 0.06 |
Pattern Density (g/L) | 20 – 26 |
Coating Application Times | 2 – 4 |
Static Pressure Head (represented by sprue height) | Varies according to test requirements |
4. Sample Design and Optimization
4.1 Original Sample Design Scheme
The original sample design scheme is shown in Figure 1. The sample has a maximum circle diameter , a sample width , and the sample thickness is a variable, set as 6mm, 8mm, and 10mm respectively. The total length of the sample .
Two experiments were carried out with the above samples under different process parameters.
Experiment 1:
- Fixed parameters: The static pressure head was 150mm, the pattern density was 20g/L, and the coating was applied 2 times.
- Variable parameters: Different sample thicknesses (7mm, 10mm, 12mm), pouring temperatures (1420°C, 1480°C), and vacuum degrees (0.03MPa, 0.06MPa).
The sample assembly process of Experiment 1 is shown in Figure 2. Each pattern cluster contained 3 types of wall – thickness samples. After pouring at 1420°C and 1480°C and cleaning, the samples were obtained as shown in Figure 4. The results showed that at negative pressure degrees of 0.03MPa and 0.06MPa, and pouring temperatures of 1420°C and 1480°C, all wall – thickness samples could be completely filled. This indicates that this sample structure cannot sensitively reflect the influence of changes in pouring temperature and negative pressure degree on the flow length.
Experiment 2:
Based on Experiment 1, the pouring results were compared under different pouring static pressure heads. The sample assembly process of Experiment 2 is shown in Figure 5. The distance between samples on the same pattern cluster was 40mm. Pouring was carried out at 1420°C and 1480°C, and other pouring parameters were the same as in Experiment 1. The pouring results are shown in Figure 6. The results showed that at 1420°C and 1480°C, all wall – thickness samples could basically be completely filled, without obvious unfilled phenomena.
From the pouring results of Experiment 1 and Experiment 2, it can be seen that under different pouring parameters such as high and low pouring temperatures, high and low vacuum degrees, and different pressure heads, the samples can basically be completely filled. However, they cannot sensitively reflect the filling ability of molten iron under different pouring parameters. Therefore, it is necessary to further improve the sample size to obtain the best experimental method.
4.2 Sample Design Scheme Optimization
After analysis and improvement, the optimized sample structure is shown in Figure 7. The optimized sample size is: maximum circle diameter , sample width , sample thickness , and sample total length .
[Insert Figure 7: Optimized sample structure here]
The sample assembly process of the optimized scheme is shown in Figure 8. Each group has 3 samples, and the sample density is 20g/L. The vertical distance between two samples is 100mm to reduce the thermal influence between the two samples and ensure a static pressure head difference of 100mm for each sample during pouring. The verification test was carried out with the coating applied 2 times, a negative pressure degree of 0.06MPa, and pouring temperatures of 1480°C and 1420°C.
The buried – box molding is shown in Figure 9, and the pouring results are shown in Figure 10. It can be seen from Figure 10 that when pouring at 1420°C and 1480°C, each group of samples cannot be completely filled, and the filling distances are different. Moreover, at both 1480°C and 1420°C, the filling length gradually increases from bottom to top. The overall filling length at 1480°C is longer than that at 1420°C, and at the same static pressure head position, the filling length at 1480°C is longer than that at 1420°C. Therefore, the optimized samples are very sensitive to changes in process parameters, and the filling ability is different under different pouring parameters. The influence of each pouring factor on the filling ability of lost foam casting can be basically determined according to the filling distance of the samples.
[Insert Figure 9: Buried – box molding here]
[Insert Figure 10: Pouring results of the optimized samples here]
5. Sample Mold Design
The samples in the previous experiments were made by manually cutting foam plates, which had low efficiency, poor dimensional accuracy, and were difficult to change the pattern density and determine the sample structure according to the experimental requirements. To address this issue, a lost foam mold for the samples was designed according to the sample structure. Using the mold to make white molds not only has high efficiency and high dimensional accuracy but also can change the sample density according to the experimental requirements.
The design of the sample white mold is shown in Figure 11. When designing the sample white mold, the following points should be noted:
- Anti – deformation ribs are formed integrally with the sample white mold to prevent the sample from deforming and breaking during demolding. They need to be removed after mold assembly.
- The length scale interval is 50mm, which is convenient for directly reading the filling length after pouring.
- The sprue bonding area is used to bond the inner sprue and is at a certain distance from the sample to facilitate the removal of the inner sprue after pouring.
6. Conclusion
A testing method for the fluidity of molten metal in lost foam casting of cast iron parts has been designed. The selected spiral – shaped fluidity test strip with a width of 20mm and a thickness of 8mm can represent the filling situation of common castings in actual production and sensitively reflect the influence of changes in process parameters on the flow length. By using this method, enterprises can test the influence of various factors on the filling ability according to their own process parameter conditions, providing basic data for guiding process design and optimization. This research is of great significance for improving the quality of lost foam casting products and reducing the scrap rate, which will promote the development of the lost foam casting technology in the casting industry.
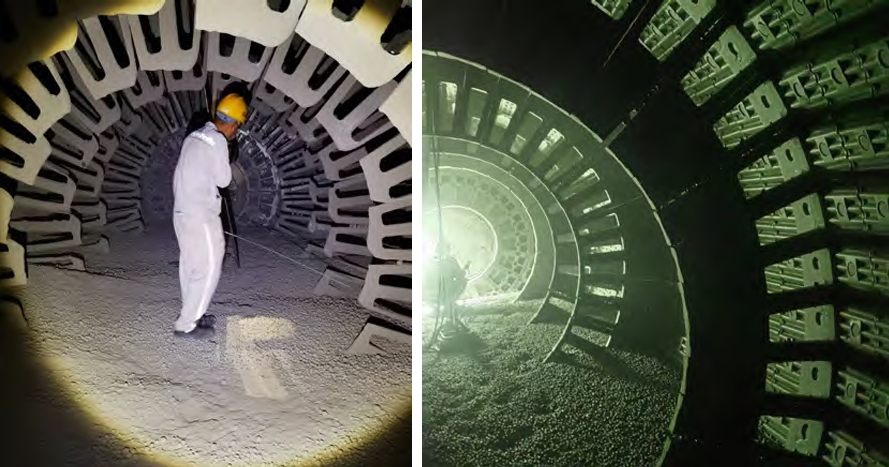