Lost foam casting indeed has the potential to revolutionize the foundry industry. Thanks to its ability to produce complex shapes with high dimensional accuracy, and its sustainability features, Lost foam casting has attracted significant attention and has been increasingly adopted in the foundry industry. Here’s why it can be a game-changer:
1. Manufacturing Complex Shapes: Lost foam casting can produce intricate and complex shapes that might be challenging or impossible with traditional casting methods. This opens up new possibilities for the types of parts that can be cast, including multi-part assemblies that can be cast as a single component, reducing assembly operations and costs.
2. Increased Efficiency and Reduced Costs: The Lost foam casting process allows for near-net-shape production, reducing the need for subsequent machining and finishing processes and saving both time and costs. Moreover, the sand used in Lost foam casting can be recycled, further cutting down costs.
3. Enhanced Product Quality: Thanks to advancements in foam pattern production and coating materials,Lost foam casting can produce castings with superior surface finish and dimensional accuracy. The use of simulation software also helps to minimize defects and scrap rates, leading to improved product quality.
4. Improved Sustainability: As noted earlier, Lost foam casting offers several sustainability benefits, including reduced material waste, energy efficiency, reduced emissions, and water conservation. This makes it an attractive option in an era when environmental sustainability is becoming a crucial consideration for industries worldwide.
5. Automation Opportunities: Lost foam casting lends itself well to automation, which can lead to increased productivity, reduced labor costs, and improved consistency and quality. This can be a significant advantage in today’s industry 4.0 era, where automation and digitization are key trends.
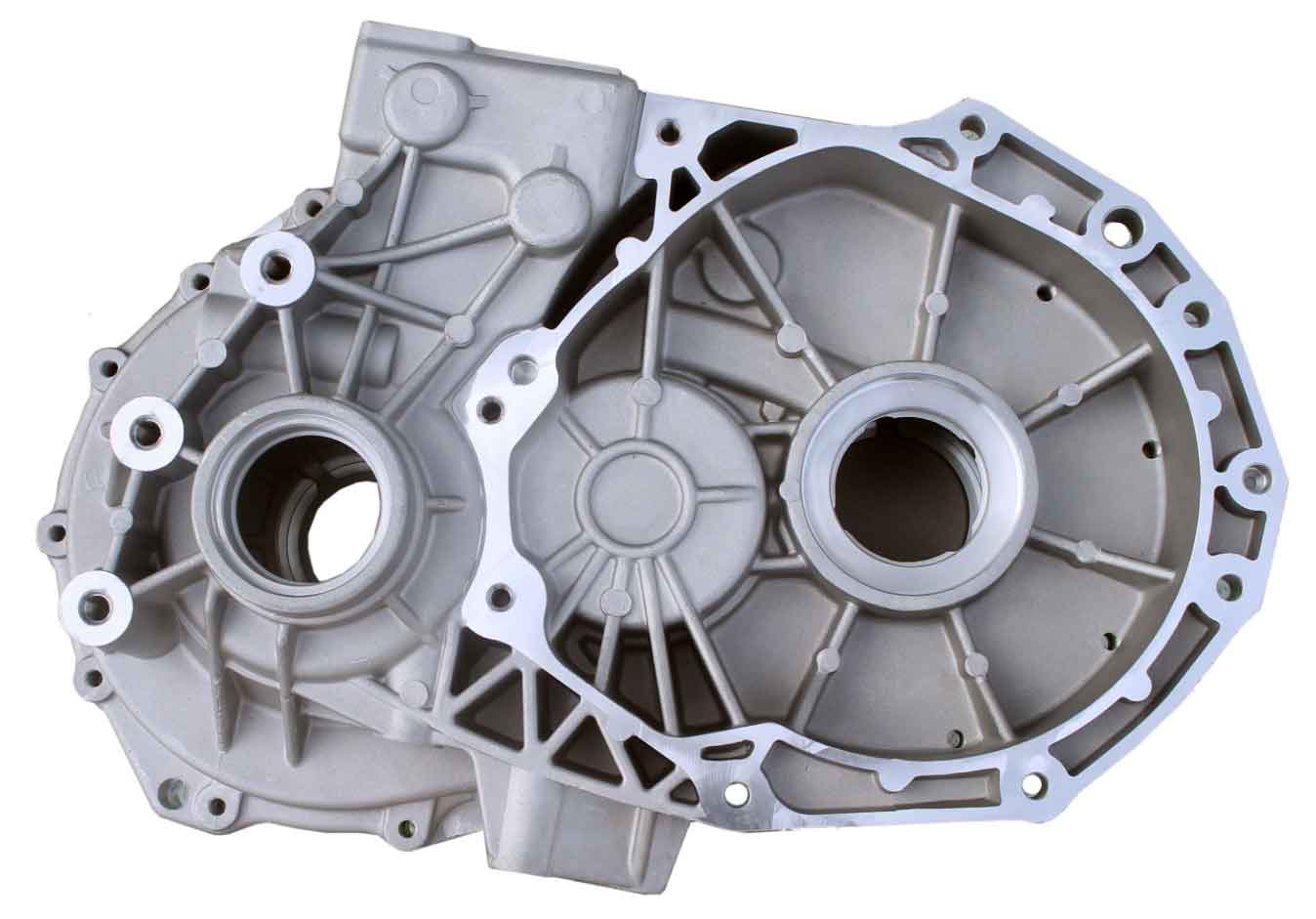
Given these benefits, it’s clear that lost foam casting has significant potential to reshape the foundry industry. However, to fully realize this potential, ongoing research and development are needed to overcome the challenges related to the Lost foam casting process, such as managing the environmental impact of polystyrene foam and improving the control of gas emissions. With continued advancements in these areas, Lost foam casting could indeed become a mainstream casting process in the foundry industry.