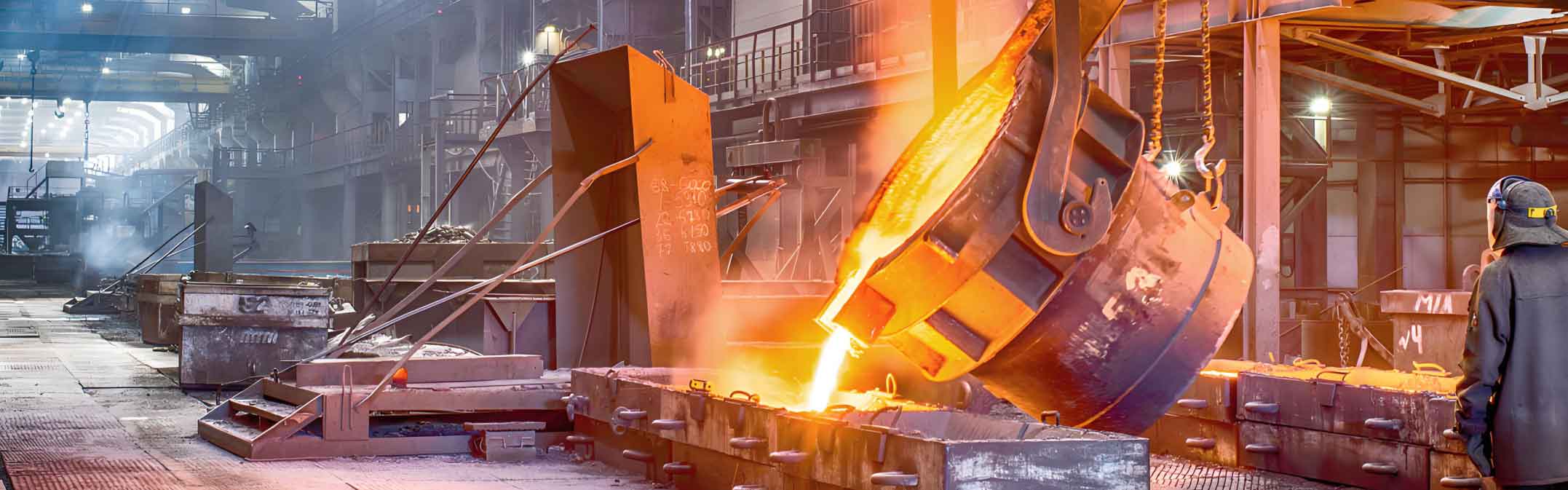
The manufacturing industry has witnessed significant advancements with the advent of innovative technologies such as lost foam casting and additive manufacturing. These two techniques, each with its own unique advantages, can be synergistically integrated to enhance production processes, improve product quality, and reduce costs. This article explores the synergies and integration opportunities between lost foam casting and additive manufacturing, providing insights into how these methods can be combined to revolutionize modern manufacturing.
Overview of Lost Foam Casting
Lost foam casting is a precise and cost-effective casting technique that involves creating a foam pattern, which is later vaporized and replaced by molten metal to form the final part. This method is known for its design flexibility, high dimensional accuracy, and minimal material waste.
Key Benefits of Lost Foam Casting:
- Design Flexibility: Enables the production of intricate and complex shapes.
- High Precision: Ensures superior surface finish and dimensional accuracy.
- Cost Savings: Reduces the need for extensive machining and assembly.
- Material Efficiency: Minimizes material waste, contributing to sustainable manufacturing practices.
- Environmental Benefits: Generates less waste material and consumes less energy compared to traditional casting methods.
Overview of Additive Manufacturing
Additive manufacturing, commonly known as 3D printing, involves building parts layer by layer from a digital model. This technology allows for the creation of complex geometries that would be challenging or impossible to achieve with traditional manufacturing methods.
Key Benefits of Additive Manufacturing:
- Complex Geometries: Allows for the creation of parts with intricate designs and internal structures.
- Customization: Enables the production of customized parts tailored to specific requirements.
- Rapid Prototyping: Facilitates quick design iterations and prototyping, reducing time-to-market.
- Material Efficiency: Uses only the necessary amount of material, reducing waste.
- Reduced Tooling Costs: Eliminates the need for traditional tooling, lowering initial setup costs.
Synergies between Lost Foam Casting and Additive Manufacturing
The integration of lost foam casting and additive manufacturing can leverage the strengths of both methods, creating new opportunities for innovation and efficiency in manufacturing. Key synergies include:
- Enhanced Design Capabilities: Additive manufacturing can be used to create complex foam patterns for lost foam casting, enabling the production of intricate parts with high precision.
- Reduced Lead Times: Combining additive manufacturing for pattern creation with lost foam casting can significantly reduce lead times, allowing for faster production cycles.
- Cost Efficiency: Additive manufacturing reduces the cost and time associated with traditional pattern-making processes, while lost foam casting provides cost-effective production of metal parts.
- Material Optimization: Both methods minimize material waste, contributing to more sustainable manufacturing practices.
- Prototyping and Production: Additive manufacturing can be used for rapid prototyping, while lost foam casting can be employed for high-volume production, streamlining the transition from prototype to final product.
Integration Opportunities for Lost Foam Casting and Additive Manufacturing
Several integration opportunities exist for combining lost foam casting and additive manufacturing, enhancing the capabilities of both technologies. Key opportunities include:
- Hybrid Pattern Creation: Using additive manufacturing to produce complex foam patterns for lost foam casting. This approach allows for the creation of detailed and customized patterns that would be challenging to produce using traditional methods.
- Rapid Tooling: Additive manufacturing can be used to create molds and tooling for lost foam casting, reducing the time and cost associated with traditional tooling processes.
- Design Iteration and Prototyping: Additive manufacturing enables rapid prototyping and design iteration, allowing manufacturers to test and refine their designs before committing to full-scale production using lost foam casting.
- Complex Assemblies: Combining the strengths of both methods to produce complex assemblies with multiple components, each optimized for the best production method.
- On-Demand Manufacturing: Utilizing additive manufacturing for low-volume, customized parts, and lost foam casting for high-volume production runs, offering flexibility and scalability in manufacturing.
Case Studies: Integration of Lost Foam Casting and Additive Manufacturing
The following table provides an overview of successful integration projects where lost foam casting and additive manufacturing were combined to achieve remarkable results:
Project | Industry | Integration Approach | Benefits Achieved |
---|---|---|---|
Automotive Components | Automotive | Additive manufacturing of foam patterns | Reduced lead times, enhanced design flexibility, cost savings |
Turbine Blades | Aerospace | Rapid prototyping with additive manufacturing | High precision, rapid design iterations, reduced material waste |
Medical Implants | Medical Devices | Custom patterns for lost foam casting | Customization, high dimensional accuracy, superior surface finish |
Industrial Valves | Industrial Equipment | Hybrid pattern creation | Improved production efficiency, reduced tooling costs, material optimization |
Challenges and Solutions in Integrating Lost Foam Casting and Additive Manufacturing
While the integration of lost foam casting and additive manufacturing offers numerous benefits, it also presents certain challenges that manufacturers must address:
- Pattern Durability: Foam patterns created using additive manufacturing may require careful handling to avoid damage.
- Solution: Implementing rigorous quality control measures and using durable materials for pattern creation.
- Process Compatibility: Ensuring compatibility between additive manufacturing processes and lost foam casting requirements.
- Solution: Conducting thorough testing and optimization of additive manufacturing parameters to ensure successful integration.
- Cost Management: Balancing the costs associated with additive manufacturing and lost foam casting to achieve overall cost savings.
- Solution: Performing detailed cost-benefit analyses to identify the most cost-effective integration strategies.
Future Prospects of Integrating Lost Foam Casting and Additive Manufacturing
The future of manufacturing lies in the seamless integration of advanced technologies such as lost foam casting and additive manufacturing. As both methods continue to evolve, their combined capabilities will unlock new possibilities for innovation, efficiency, and sustainability in manufacturing.
Key Future Trends:
- Advanced Materials: Development of new materials for additive manufacturing that are compatible with lost foam casting, enhancing the quality and durability of foam patterns.
- Automation and Digitalization: Integration of automation and digital tools to streamline the entire manufacturing process, from design and prototyping to production and quality control.
- Sustainability: Continued emphasis on sustainable manufacturing practices, leveraging the material efficiency and environmental benefits of both lost foam casting and additive manufacturing.
- Customization and Personalization: Increased demand for customized and personalized products, driving the adoption of hybrid manufacturing approaches that combine the strengths of both methods.
Conclusion
The integration of lost foam casting and additive manufacturing offers significant synergies and opportunities for innovation in modern manufacturing. By leveraging the strengths of both methods, manufacturers can achieve enhanced design capabilities, reduced lead times, cost efficiency, and material optimization. Successful integration projects across various industries demonstrate the potential of this combined approach to revolutionize production processes and drive sustainable manufacturing practices. As technology continues to advance, the future prospects for integrating lost foam casting and additive manufacturing are promising, paving the way for a new era of manufacturing excellence.