1. Introduction
Lost foam casting technology has witnessed significant growth in recent years due to its numerous advantages such as low pollution, process flexibility, low labor intensity, and good repeatability. It has become particularly popular in the production of box and shell products. This article focuses on analyzing the defects that occur during the lost foam casting process of products like flywheel housings and presents solutions to these problems.
1.1 Advantages of Lost Foam Casting
Lost foam casting offers several benefits compared to traditional sand casting. It provides more accurate casting dimensions, better repeatability, greater production flexibility, and superior internal quality. Since the patent expired in 1980, this technology has spread rapidly worldwide and has now reached a relatively mature stage, with wide applications, especially for complex shell components.
1.2 Common Defects in Lost Foam Casting
Despite its advantages, lost foam casting is prone to certain defects. In the production of flywheel housings and similar castings, common defects include sand sticking, porosity, and sand washing. These defects can significantly affect the quality of the final product and lead to increased production costs due to scrap.
2. Sand Sticking Defect Analysis and Solutions
2.1 Causes of Sand Sticking
Sand sticking occurs when the molten metal adheres to the sand on the casting surface during pouring. In the case of flywheel housing castings, improper placement, structural design, or process design can prevent the mold cluster from being properly vibrated and compacted in the sand box, resulting in sand sticking. For example, the 9661 flywheel housing with a material of HT250, weighing about 22 kg and having specific dimensions, exhibited sand sticking in the top of the inner cavity. The existing process had certain limitations, such as the motor hole being at the bottom, which led to loose sand at the top during vibration as the top angle was greater than 90°. Additionally, factors like the tightness of the molding sand, the refractoriness of the coating, the pouring temperature, and the coating thickness also influenced the sand sticking defect.
Factors Affecting Sand Sticking | Description |
---|---|
Molding Sand Tightness | Insufficient sand filling or inability to compact the sand at the top of the flywheel housing |
Coating Refractoriness | Affects the ability of the coating to resist the adhesion of molten metal |
Pouring Temperature | Higher temperatures may increase the likelihood of sand sticking |
Coating Thickness | Inappropriate thickness can impact the separation of metal and sand |
2.2 Control Measures for Sand Sticking
To address the sand sticking issue, the following measures were taken:
- Adjusting the placement of the white model: The motor hole of the flywheel housing was turned upwards to facilitate sand filling and ensure sufficient sand at the top.
- Increasing the distance between flywheel housings: The distance between two flywheel housings was increased from 80 mm to 120 mm to enhance the compactness of the sand.
2.3 Production Verification of Sand Sticking Solutions
After implementing these measures and keeping other variables such as the dipping process, pouring temperature, and vacuuming unchanged, production verification was carried out. The results showed that the sand sticking defect was completely eliminated, demonstrating the effectiveness of the proposed solutions.
3. Porosity Defect Analysis and Solutions
3.1 Causes of Porosity
Porosity in castings occurs when the gas and residues generated by the vaporization of the white model cannot be expelled in a timely manner as the molten iron enters the mold cluster. In the case of the flywheel housing for SAIC Maxus, porosity defects were observed, especially in the motor hole at the top of the product. The main factors contributing to porosity included the pouring temperature, coating permeability, pouring speed, and the lack of proper exhaust at the top of the flywheel housing. For example, a lower pouring temperature could lead to incomplete combustion of the foam and gas entrapment, while a too-thick coating at the motor hole could prevent gas escape. Additionally, insufficient vacuuming and an improper process design without an exhaust port at the top also played a role.
Factors Affecting Porosity | Description |
---|---|
Pouring Temperature | Low temperature causes incomplete foam combustion and gas entrapment |
Coating Thickness at Motor Hole | Thick coating hinders gas escape |
Vacuum Degree | Inadequate vacuuming fails to remove gas in time |
Process Design | Lack of exhaust port at the top of the flywheel housing |
3.2 Control Measures for Porosity
The following measures were implemented to address the porosity problem:
- Increasing the pouring temperature: The pouring temperature was raised from 1430 – 1440°C to 1450 – 1460°C.
- Reducing the coating thickness at the motor hole: The coating thickness was decreased from 2.0 mm to 0.5 mm.
- Increasing the vacuum degree: The vacuum was increased from -0.025 MPa to -0.045 MPa.
- Adding an exhaust piece at the motor hole: An exhaust piece of 50mm (long) x 30 mm (high) x 5 mm (width) was added.
3.3 Production Verification of Porosity Solutions
Production verification was carried out by varying one parameter at a time while keeping the others constant. The results showed that adding an exhaust piece at the motor hole was the most effective solution, completely eliminating the porosity defect in subsequent large-scale production.
4. Sand Washing Defect Analysis and Solutions
4.1 Causes of Sand Washing
Sand washing occurs when the sand in the mold cluster cavity is washed into the casting by the molten metal. In the case of the connecting rod rest casting, the main reasons for sand washing were the incomplete sealing of the pouring system, especially the straight runner which could cause siphoning, and an unreasonable pouring system design resulting in an unsmooth filling process and high local pressure in the inner runner. These factors led to coating rupture and sand being carried into the cavity by the molten metal. The sand washing defect was mainly observed near the bottom inner runner.
Factors Affecting Sand Washing | Description |
---|---|
Inner Runner Coating Strength | Low coating strength leads to rupture under the impact of molten metal |
Inner Runner Pressure | High pressure causes coating rupture |
Molten Metal Backspray | Severe backspray can also cause coating rupture |
4.2 Control Measures for Sand Washing
To solve the sand washing problem, the following measures were taken:
- Increasing the coating thickness of the inner runner: An additional coating process was added to the inner runner, increasing the coating thickness to 2.2 mm.
- Increasing the number of inner runners: An additional inner runner of the same size was added at the bottom.
4.3 Production Verification of Sand Washing Solutions
Production verification was carried out with different measures. The results showed that adding an inner runner at the bottom was the most effective solution, completely eliminating the sand washing defect in subsequent production. The optimized process included 3 inner runners at the bottom and 1 at the top, which achieved a good flow distribution and pressure reduction effect.
5. General Considerations in Lost Foam Casting Process Optimization
5.1 Design Considerations for New Products
When developing new products, it is essential to consider the potential causes of casting defects and avoid them through careful process design. This requires a thorough understanding of the product structure and the characteristics of the lost foam casting process.
5.2 Process Verification Steps
During the process verification, the number of products should be gradually increased from small batches to large batches. This approach helps to identify and address any potential issues in a timely manner and avoid significant losses due to insufficient consideration of the process. The process verification should involve five key steps: understanding the current situation, analyzing the causes, formulating a plan, implementing countermeasures, and confirming the effectiveness.
6. Conclusion
Lost foam casting technology has great potential in the production of various castings, but it also faces challenges such as sand sticking, porosity, and sand washing defects. By analyzing the causes of these defects and implementing appropriate control measures, as demonstrated in the case of flywheel housings and other castings, it is possible to significantly improve the quality of the castings and reduce production costs. The key lies in a thorough understanding of the process, careful design, and systematic verification to ensure the successful application of lost foam casting technology.
6.1 Coating Materials and Their Properties
The choice of coating materials is crucial in lost foam casting. Coatings not only protect the foam pattern from damage during handling and storage but also play a significant role in determining the final quality of the casting. Different coating materials have varying properties such as refractoriness, permeability, and adhesion strength.
- Refractoriness: A coating with high refractoriness is essential to withstand the high temperatures of the molten metal without breaking down. This property ensures that the coating does not react with the metal and maintains its integrity during the casting process. For example, ceramic-based coatings are often used due to their excellent refractoriness.
- Permeability: The permeability of the coating allows the gases generated during the vaporization of the foam to escape. If the coating is too impermeable, gas entrapment can occur, leading to porosity defects. Coatings with an appropriate level of permeability need to be selected based on the specific requirements of the casting process.
- Adhesion Strength: The coating must adhere well to the foam pattern to prevent it from peeling off during the casting process. A weak adhesion can result in coating detachment and subsequent defects in the casting.
6.2 Vacuum System and Its Optimization
The vacuum system is an integral part of lost foam casting. It helps in removing the gases generated during the process and maintaining a proper pressure environment. An optimized vacuum system can significantly improve the quality of the casting.
- Vacuum Level Control: The appropriate vacuum level needs to be maintained throughout the casting process. Too low a vacuum level may not be sufficient to remove all the gases, while too high a vacuum level can cause deformation of the foam pattern or even collapse of the mold. Precise control of the vacuum level is necessary to ensure a smooth casting process.
- Vacuum Distribution: Uniform distribution of the vacuum within the mold is crucial. Uneven vacuum distribution can lead to differences in the filling rate of the molten metal and the escape of gases, resulting in defects such as porosity and incomplete filling. Designing an efficient vacuum distribution system is essential for obtaining high-quality castings.
6.3 Pattern Design and Its Impact on Casting Quality
The design of the foam pattern has a direct impact on the quality of the casting. A well-designed pattern can minimize defects and ensure a smooth casting process.
- Pattern Complexity: The complexity of the pattern should be carefully considered. While lost foam casting is suitable for complex shapes, overly complex patterns may increase the likelihood of defects. For example, intricate internal structures may pose challenges in terms of gas escape and filling of the molten metal. Simplifying the pattern design where possible can help in reducing defects.
- Pattern Density and Porosity: The density and porosity of the foam pattern affect the amount of gas generated during vaporization and the ease of metal filling. A pattern with an appropriate density and porosity needs to be selected to ensure efficient gas removal and complete filling of the mold.
6.4 Molten Metal Pouring Parameters
The parameters related to the pouring of the molten metal also play a crucial role in determining the quality of the casting.
- Pouring Temperature: As discussed earlier, the pouring temperature affects the combustion of the foam, gas generation, and the fluidity of the molten metal. An optimal pouring temperature needs to be determined based on the specific alloy and the casting requirements. A too-high or too-low pouring temperature can lead to various defects.
- Pouring Speed: The pouring speed determines the rate at which the molten metal fills the mold. A proper pouring speed is necessary to ensure a smooth filling process without causing turbulence or excessive pressure. Too fast a pouring speed can lead to sand washing and other defects, while too slow a pouring speed can result in incomplete filling and porosity.
6.5 Post-Casting Treatment and Inspection
After the casting process is completed, post-casting treatment and inspection are essential to ensure the quality of the final product.
- Cleaning and Finishing: The casting needs to be cleaned to remove any adhering sand, coatings, or other residues. This process may involve mechanical cleaning methods such as shot blasting or chemical cleaning depending on the nature of the contaminants. After cleaning, finishing operations such as machining may be required to achieve the final dimensions and surface finish of the product.
- Inspection and Quality Control: Thorough inspection of the casting is necessary to detect any defects. Non-destructive testing methods such as X-ray inspection, ultrasonic inspection, or visual inspection can be used to identify internal and external defects. Quality control measures should be in place to ensure that only castings that meet the specified quality standards are accepted.
In conclusion, lost foam casting is a complex process that requires careful consideration of various factors to achieve high-quality castings. From the choice of coating materials to the optimization of the vacuum system, pattern design, pouring parameters, and post-casting treatment and inspection, each aspect plays a crucial role in determining the success of the casting process. By continuously improving and optimizing these aspects, the potential of lost foam casting technology can be fully realized, leading to the production of high-quality castings with fewer defects and improved overall performance.
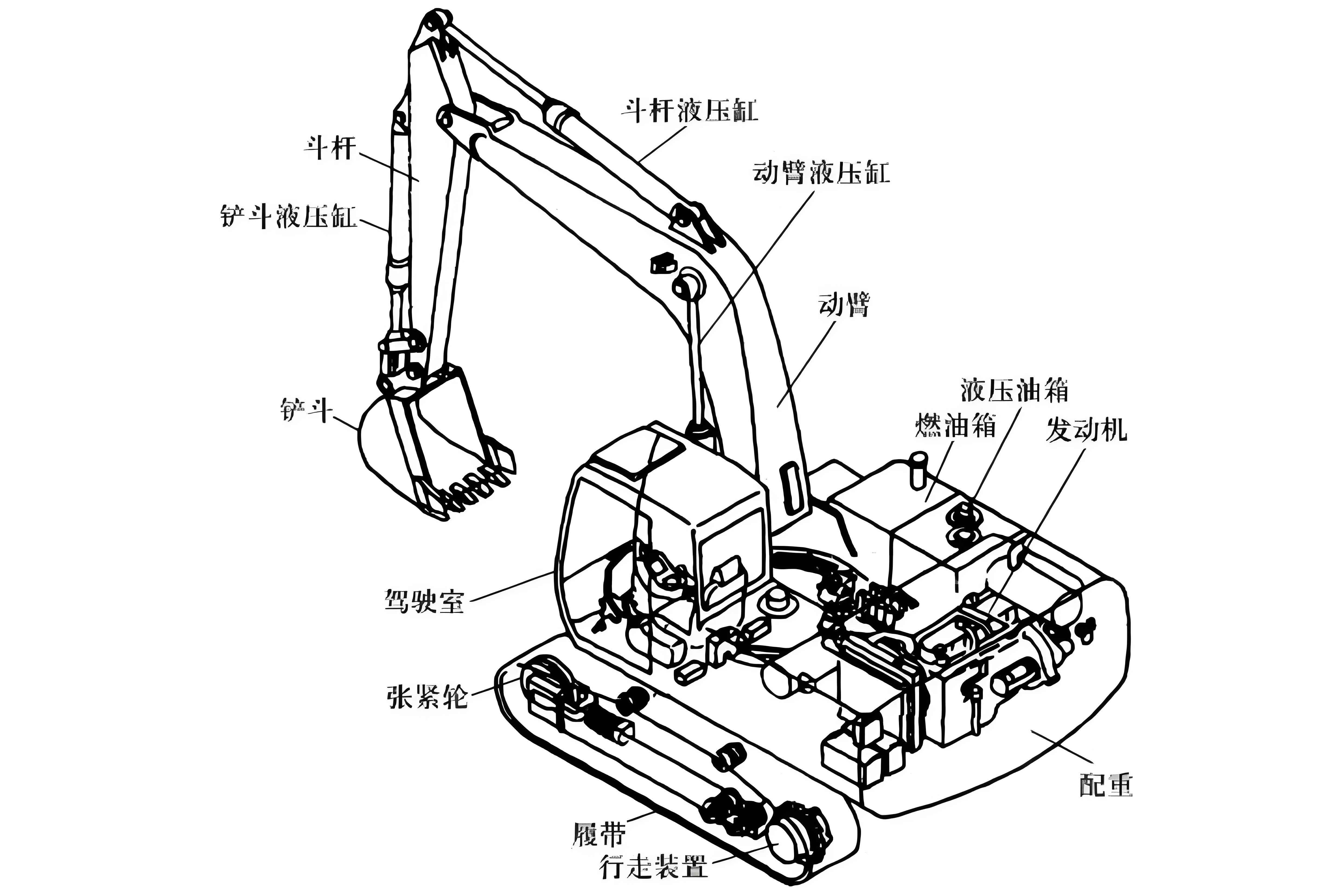