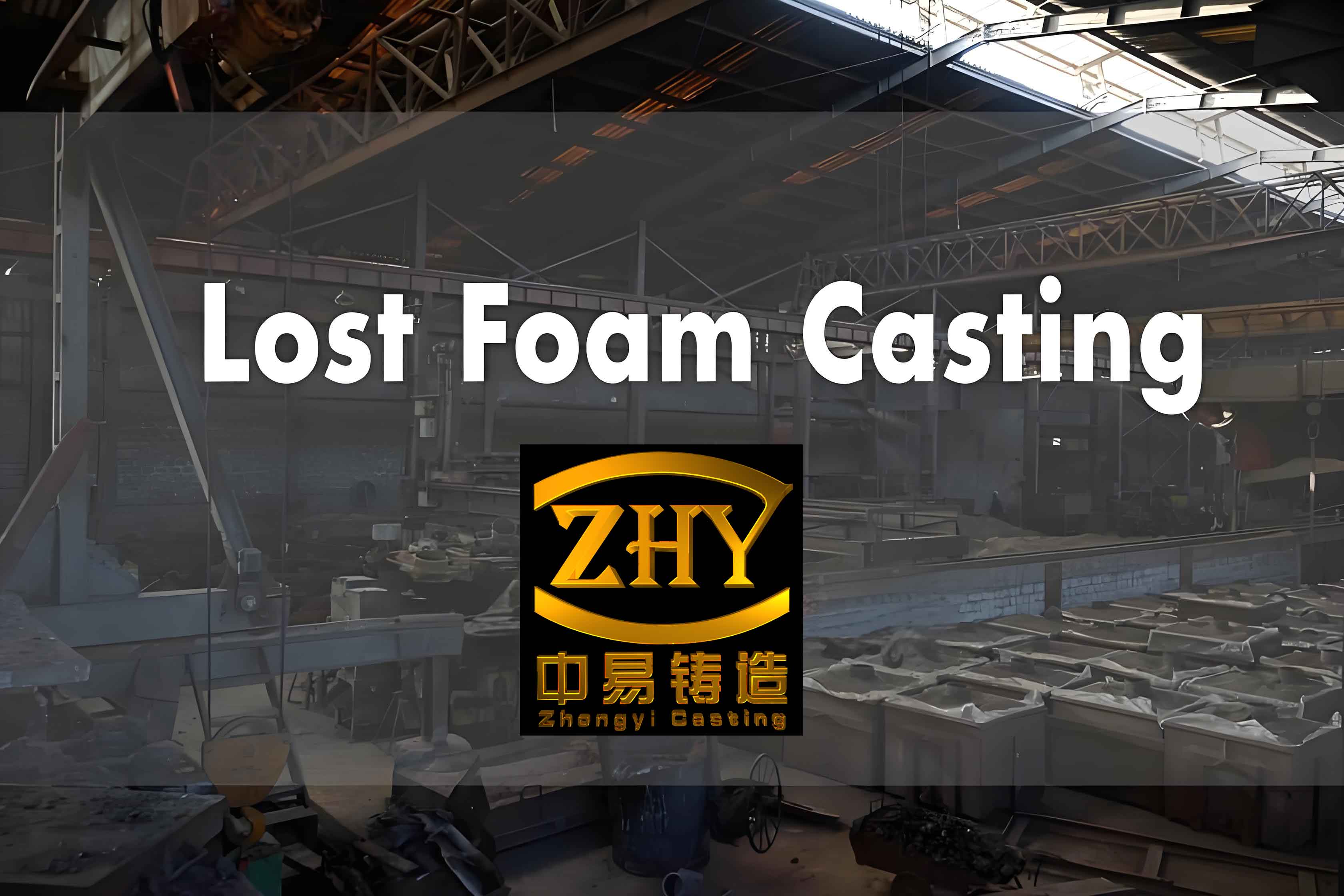
1. Introduction
Lost foam casting has emerged as a significant casting technique with numerous advantages such as high precision, good repeatability, flexibility in production, and excellent internal quality. This process has witnessed rapid growth globally since the expiration of its patent in 1980. It is particularly well-suited for complex shell components. In this article, we focus on the application of lost foam casting in the production of flywheel housing and other castings, analyzing the common defects and proposing effective solutions.
1.1 The Significance of Lost Foam Casting
Lost foam casting offers a more environmentally friendly alternative compared to traditional sand casting methods. It reduces the need for complex pattern-making and core-making processes, resulting in lower labor intensity and higher production efficiency. The ability to produce intricate shapes with good dimensional accuracy makes it a preferred choice for many industrial applications.
1.2 Focus on Flywheel Housing Castings
Flywheel housing castings are crucial components in many mechanical systems. The quality of these castings directly impacts the performance and reliability of the overall equipment. However, during the lost foam casting process, several defects may occur, which require in-depth analysis and appropriate corrective measures.
2. Common Defects in Lost Foam Casting of Flywheel Housing
2.1 Burn-on Defects
2.1.1 Causes of Burn-on
- Improper Placement and Design: In the case of the 9661 flywheel housing, its large size, thin base wall thickness, and certain design features such as the motor hole location can lead to insufficient vibration compaction of the mold cluster in the sand box. This results in loose sand in some areas, especially when the top angle is greater than 90 degrees.
- Influence of Process Parameters: Factors like the tightness of the molding sand, the refractoriness of the coating, the pouring temperature, and the coating thickness also play a crucial role. For example, if the molding sand cannot be compacted enough or if the coating is not resistant enough to the high temperature of the molten metal, burn-on defects are likely to occur.
2.1.2 Analysis of Burn-on in 9661 Flywheel Housing
The 9661 flywheel housing exhibits mechanical burn-on, with sand grains and metal mechanically mixed and adhered to the surface. The main affected area is the top of the inner cavity, with a scrap rate of 20%. This is due to the inability to fill and compact the sand properly in this area.
2.2 Porosity Defects
2.2.1 Causes of Porosity
- Incomplete Gas Evacuation: When the molten iron enters the mold cluster, the decomposition of the white pattern generates a large amount of gas and residues. If these gases cannot be discharged in a timely manner, porosity defects will occur.
- Influence of Process Parameters: The pouring temperature, coating permeability, and pouring speed are key factors. For example, if the pouring temperature is too low, the foam may not burn completely, leaving unevacuated gases to form pores. Additionally, a thick coating around the motor hole can prevent gas escape, and insufficient vacuum can also lead to gas accumulation and porosity.
2.2.2 Analysis of Porosity in Flywheel Housing for SAIC Maxus
The porosity defect in the flywheel housing for SAIC Maxus is mainly manifested as smooth holes on the surface or near the surface after processing. The pores are concentrated at the top, especially around the motor hole, with a scrap rate of 30%.
2.3 Sand Wash Defects
2.3.1 Causes of Sand Wash
- Incomplete Sealing of Pouring System: In the pouring process, if the sprue, runner, and ingate are not completely sealed, especially the sprue, a siphon effect may occur, leading to sand wash defects.
- Unreasonable Pouring System Design: An inefficient pouring system design can cause uneven filling, resulting in high local pressure in the ingate. This can cause the coating to crack due to the impact of the molten iron, allowing the sand to enter the mold cavity along with the molten iron.
2.3.2 Analysis of Sand Wash in Connecting Rod Bracket Casting
In the connecting rod bracket casting, the sand wash defect is mainly located at the bottom of the cavity along the pouring line and near the ingate where the molten iron enters the cavity. The scrap rate is 20%.
3. Analysis of Defect Control Measures
3.1 Measures for Burn-on Defects
3.1.1 Adjusting the Placement of the White Pattern
By changing the orientation of the flywheel housing so that the motor hole faces upward, it becomes easier for the molding sand to fill the top area, ensuring sufficient sand coverage.
3.1.2 Increasing the Distance between Patterns
Increasing the distance between two flywheel housing patterns from 80mm to 120mm enhances the compactness of the molding sand between them, reducing the likelihood of burn-on defects.
3.2 Measures for Porosity Defects
3.2.1 Adjusting the Pouring Temperature
Increasing the pouring temperature from 1430 – 1440°C to 1450 – 1460°C helps to ensure more complete combustion of the foam and better gas evacuation.
3.2.2 Reducing the Coating Thickness
Reducing the coating thickness around the motor hole from 2.0mm to 0.5mm allows for easier gas escape.
3.2.3 Increasing the Vacuum Degree
Increasing the vacuum from -0.025MPa to -0.045MPa helps to draw out the gases more effectively.
3.2.4 Adding an Exhaust Sheet
Adding an exhaust sheet (50mm x 30mm x 5mm) near the motor hole provides an additional path for gas to escape.
3.3 Measures for Sand Wash Defects
3.3.1 Increasing the Coating Thickness of the Ingate
Adding an extra coating process to the ingate and increasing the coating thickness to 2.2mm improves the resistance of the coating to the impact of the molten iron.
3.3.2 Increasing the Number of Ingates
Adding an additional ingate at the bottom helps to distribute the molten iron more evenly, reducing the local pressure and the risk of sand wash.
4. Production Verification and Results
4.1 Burn-on Defect Verification
After implementing the measures for burn-on defects, a production verification was carried out. With the immersion coating process, pouring temperature, and vacuum degree remaining unchanged, the production volume was gradually increased from a small batch to a large batch. The result showed that the burn-on defect was completely eliminated, achieving the expected improvement.
4.2 Porosity Defect Verification
For porosity defects, different measures were tested separately while keeping other parameters constant. The results showed that adding an exhaust sheet had the best effect. Through subsequent small-batch to large-batch verification, it was confirmed that the porosity defect around the motor hole was completely resolved.
4.3 Sand Wash Defect Verification
In the case of sand wash defects, two measures were tested. The results showed that adding an additional ingate at the bottom was the most effective. Through further verification, it was demonstrated that the sand wash defect in the connecting rod bracket casting was completely eliminated.
5. General Considerations in the Process of Solving Defects
5.1 Defect Prevention in New Product Development
During the development of new products, it is essential to consider the potential causes of casting defects in advance. Through careful process design, many defects can be avoided, saving time and resources in the long run.
5.2 Gradual Process Verification
In the process of process verification, it is advisable to increase the production quantity gradually, from a small batch to a large batch. This approach allows for a more comprehensive assessment of the process and helps to avoid significant losses due to insufficient consideration of various factors.
5.3 Systematic Problem-Solving Approach
When dealing with casting defects, a systematic approach should be adopted, covering aspects such as understanding the current situation, analyzing the causes, formulating plans, implementing countermeasures, and confirming the effectiveness. This comprehensive approach ensures that the problems are thoroughly addressed and resolved.
6. Conclusion
Lost foam casting is a promising technology for the production of flywheel housing and other castings. However, several defects may occur during the process, including burn-on, porosity, and sand wash. Through a detailed analysis of the causes of these defects and the implementation of appropriate control measures, such as adjusting the pattern placement, optimizing the pouring system, and improving the coating and exhaust arrangements, these defects can be effectively resolved. The production verification results confirm the effectiveness.