Lost foam casting has gained recognition for its efficiency and versatility in metal casting processes. This advanced casting technique offers several benefits that contribute to its efficiency and versatility. Here’s an exploration of how lost foam casting excels in these aspects:
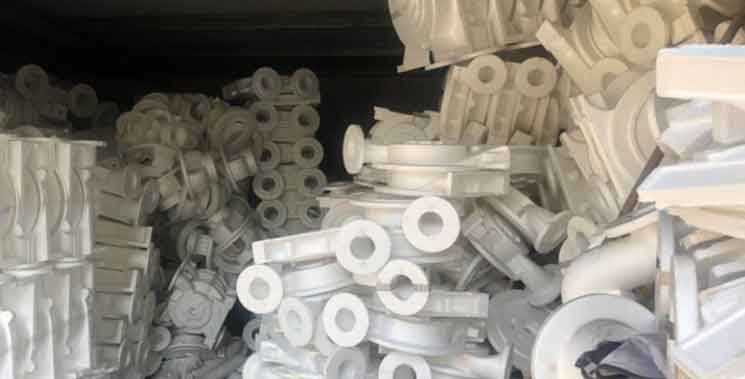
- Material Efficiency:
- Lost foam casting is highly material-efficient since it produces near-net shape castings.
- The foam patterns used in the process are designed to match the final part geometry, resulting in minimal material waste.
- This efficiency reduces material costs and ensures optimal utilization of resources.
- Time Efficiency:
- Lost foam casting is known for its time efficiency compared to traditional casting methods.
- The production of foam patterns is relatively quick, especially with the aid of advanced technologies like foam molding, CNC machining, or 3D printing.
- The elimination of complex core-making and core removal steps reduces the overall production time.
- Additionally, the near-net shape capability reduces the need for extensive post-casting machining or finishing operations, saving additional time.
- Tooling Flexibility and Cost Savings:
- Lost foam casting offers flexibility in tooling and reduces tooling costs.
- Traditional casting methods require permanent molds or expendable sand molds, which can be expensive to produce and maintain.
- In lost foam casting, the foam patterns serve as temporary molds, eliminating the need for expensive permanent tooling.
- This flexibility allows for quick pattern modifications or iterations, reducing tooling lead times and costs associated with design changes.
- Design Flexibility and Complexity:
- Lost foam casting enables the production of complex and intricate part designs with ease.
- The foam patterns can be easily shaped, manipulated, and assembled to create intricate geometries, thin walls, and internal features.
- This flexibility allows designers to explore innovative and optimized designs without the constraints of traditional tooling limitations.
- Versatility in Metal Selection:
- Lost foam casting is compatible with a wide range of metals and alloys, including aluminum, iron, steel, and various non-ferrous alloys.
- The process accommodates both ferrous and non-ferrous materials, making it suitable for diverse industrial applications.
- This versatility allows manufacturers to choose the most appropriate material for their specific requirements.
- Improved Dimensional Accuracy:
- Lost foam casting achieves excellent dimensional accuracy and repeatability.
- The foam patterns, which accurately replicate the final part geometry, contribute to precise casting replication.
- The absence of core-related factors, such as expansion or shrinkage, enhances the dimensional accuracy and consistency of the castings.
- Reduced Machining and Assembly:
- Lost foam castings often require minimal post-casting machining or assembly.
- The near-net shape capability and accurate reproduction of intricate features eliminate the need for extensive machining or assembly operations.
- This reduces labor costs, machining time, and potential errors associated with secondary operations.
- Environmental Sustainability:
- Lost foam casting aligns with sustainability goals due to reduced material waste and energy consumption.
- The foam patterns can be easily recycled or disposed of without significant environmental impact.
- The process also minimizes the generation of harmful emissions or byproducts associated with traditional sand casting.
Lost foam casting stands out for its efficiency in material usage, time savings, tooling flexibility, design versatility, dimensional accuracy, reduced machining requirements, and environmental sustainability. This combination of benefits makes lost foam casting a highly efficient and versatile choice for metal casting processes across various industries.