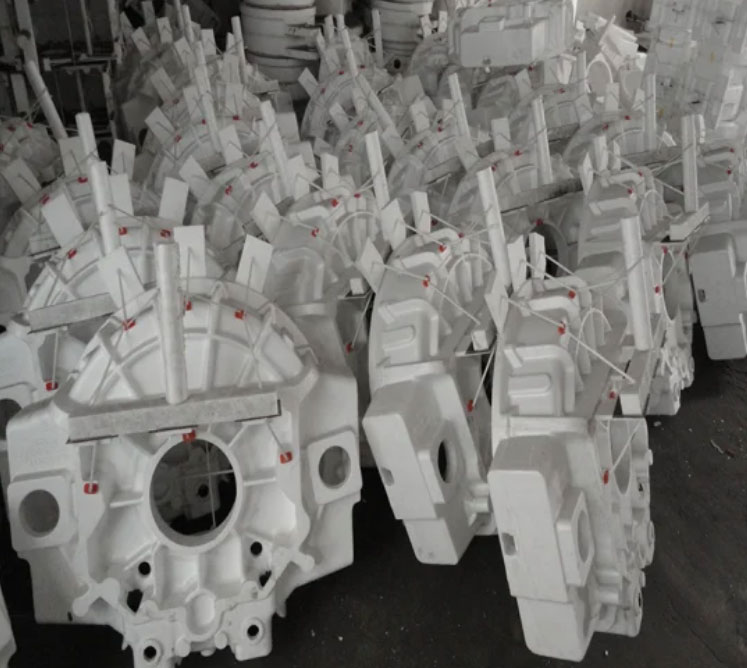
Lost foam casting (LFC) has proven to be a valuable solution for meeting modern engineering challenges related to the production of complex parts. Its unique capabilities and advantages make it well-suited to address the following challenges:
1. Design Freedom and Complexity:
Modern engineering often demands the production of intricate and complex parts with challenging geometries. Lost foam casting allows for the creation of parts with intricate details, undercuts, and thin sections that may be difficult or impossible to achieve with traditional casting methods. Designers have the freedom to explore innovative solutions and push the boundaries of conventional designs.
2. Reduction in Assembly and Welding:
Complex parts often require intricate assembly and welding processes, which can be time-consuming, labor-intensive, and prone to defects. Lost foam casting can produce complex parts as a single piece, eliminating the need for assembly and reducing the risk of assembly-related defects. This streamlined approach simplifies the manufacturing process and enhances part integrity.
3. Improved Dimensional Accuracy and Precision:
Modern engineering demands high precision and dimensional accuracy in components. Lost foam casting uses precision foam patterns that result in tight tolerances and consistent castings. This reduces the need for extensive post-casting machining, refining, and assembly, saving time and resources while ensuring precise parts.
4. Weight Reduction and Lightweighting:
Weight reduction is a critical consideration in various industries, including automotive, aerospace, and consumer electronics. Lost foam casting enables the creation of hollow sections and thin-walled components, offering opportunities for lightweighting without compromising structural integrity or functionality.
5. Rapid Prototyping and Customization:
In the fast-paced world of modern engineering, rapid prototyping and customization are essential for quick product development cycles. Lost foam casting’s ability to rapidly create and modify foam patterns makes it an ideal choice for rapid prototyping and small-scale production of custom parts.
6. Resource Efficiency and Waste Reduction:
Sustainability and environmental concerns are key challenges in modern engineering. Lost foam casting’s near-net-shape casting approach reduces material waste, and its recyclable foam patterns contribute to resource efficiency and waste reduction.
7. Complex Internal Passages and Cooling Features:
In industries like automotive and aerospace, parts often require complex internal passages and cooling features to optimize performance. Lost foam casting can create parts with intricate internal structures, facilitating the integration of these critical features.
8. Improved Surface Finish and Aesthetics:
Lost foam casting can achieve a smoother and high-quality surface finish on cast parts, reducing the need for extensive surface finishing and enhancing the aesthetics of the final components.
Lost foam casting meets modern engineering challenges by offering design freedom, reduced assembly, improved precision, lightweighting possibilities, and resource efficiency. It enables engineers and designers to realize complex and innovative solutions, making it a valuable technology for various industries seeking to address modern engineering demands. As engineers continue to push the boundaries of what is possible, lost foam casting will continue to play a crucial role in meeting these challenges and driving advancements in engineering and manufacturing.