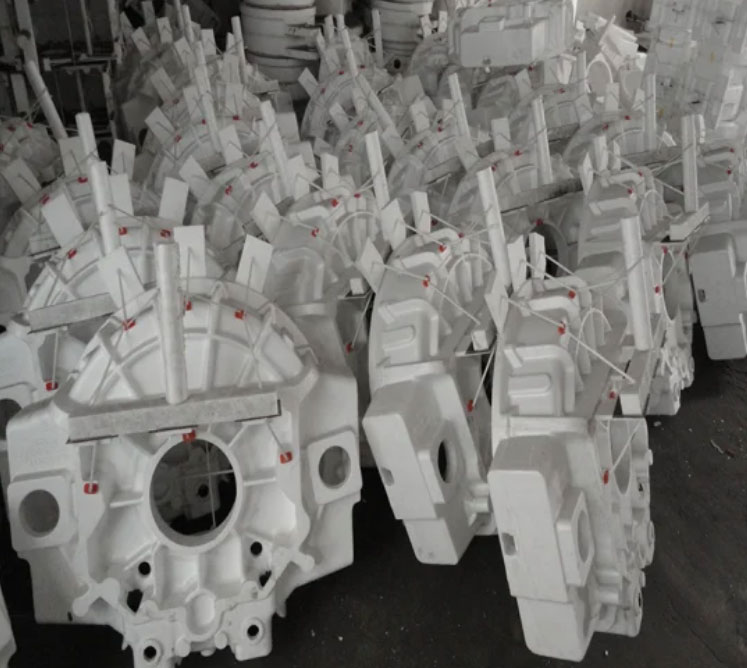
Lost foam casting (LFC) is considered a sustainable and eco-friendly casting method that offers several environmental benefits compared to traditional casting processes. Here are some of the environmental advantages of lost foam casting:
1. Reduced Material Waste:
Lost foam casting produces near-net-shape castings, which means the parts are cast very close to their final dimensions. As a result, there is minimal material waste during the casting process. Traditional casting methods, such as sand casting, often require extensive machining to achieve the final shape, leading to more material waste.
2. Lower Energy Consumption:
The lost foam casting process requires lower energy consumption compared to some other casting methods. The elimination of complex tooling and reduced machining result in lower energy requirements during the manufacturing process.
3. No Harmful Emissions:
Lost foam casting does not produce harmful emissions during the casting process. The evaporated foam patterns used in LFC are typically made of polystyrene, which undergoes a clean and complete vaporization in the mold. This process does not release harmful gases or fumes into the atmosphere.
4. Reduced Carbon Footprint:
The combination of reduced material waste, lower energy consumption, and no harmful emissions contributes to a reduced carbon footprint for lost foam casting compared to some other casting methods.
5. Fewer Chemical Binders:
Lost foam casting utilizes a refractory coating on the foam patterns to form the mold. This coating typically requires fewer chemical binders compared to sand casting, where binders are used to hold the sand together. Reducing the use of chemical binders is beneficial for environmental reasons.
6. Recycling Possibility:
The foam patterns used in lost foam casting are made from recyclable materials, such as polystyrene. This allows for the possibility of recycling the foam patterns and minimizing waste generation.
7. Streamlined Manufacturing Process:
Lost foam casting’s ability to create intricate and complex parts as single castings reduces the need for assembly, welding, and other secondary processes. This streamlined manufacturing process saves resources and reduces the overall environmental impact.
8. Lower Water Usage:
Lost foam casting typically requires less water usage compared to certain other casting methods, such as investment casting, which often involves a water-intensive shell-making process.
Lost foam casting’s eco-friendly features make it an attractive option for industries aiming to adopt sustainable manufacturing practices. Its ability to reduce material waste, lower energy consumption, and minimize harmful emissions align with the growing focus on environmental responsibility and resource conservation. As sustainable manufacturing practices gain importance, lost foam casting’s environmental benefits position it as a preferred choice for various industries seeking to reduce their environmental impact.