Lost Foam Casting has emerged as a significant manufacturing process in the electric vehicle and aerospace industries due to its ability to produce complex, lightweight, and high-precision components. This article explores the applications, benefits, and advancements of lost foam casting in these critical sectors, emphasizing the importance of the process in modern manufacturing.
Introduction to Lost Foam Casting
Lost Foam Casting is a casting process where a foam pattern of the desired component is coated with a refractory material and placed in a mold. When molten metal is poured into the mold, the foam vaporizes, leaving a metal casting that precisely replicates the foam pattern. This method is particularly advantageous for creating intricate and complex geometries that would be challenging to achieve with traditional casting methods.
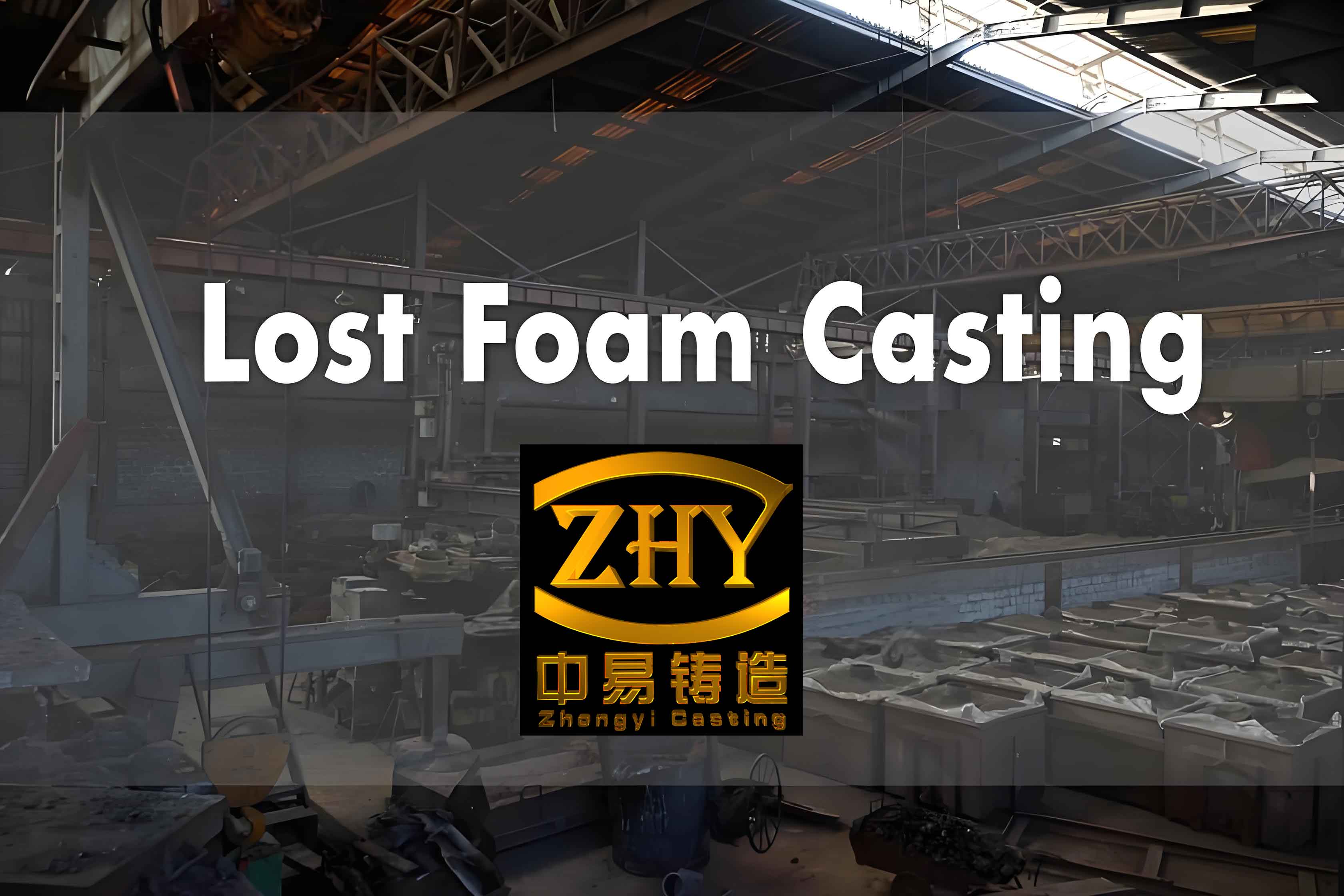
Applications of Lost Foam Casting in the Electric Vehicle Industry
The electric vehicle industry demands lightweight and high-strength components to improve efficiency and performance. Lost foam casting is well-suited for producing these components due to its precision and versatility.
Key Components in Electric Vehicles
- Battery Housings
- Material: Aluminum alloys
- Benefits: Lightweight, excellent thermal conductivity, high strength
- Motor Housings
- Material: Magnesium alloys
- Benefits: Low weight, high strength-to-weight ratio, good corrosion resistance
- Suspension Components
- Material: High-strength steel
- Benefits: Enhanced durability, reduced weight, improved vehicle dynamics
Advantages in Electric Vehicle Manufacturing
- Lightweight Components: Reduces overall vehicle weight, improving efficiency and range.
- Complex Geometries: Allows for intricate designs that enhance performance and functionality.
- Cost-Effective Production: Reduces the need for extensive machining and assembly, lowering manufacturing costs.
Applications of Lost Foam Casting in the Aerospace Industry
The aerospace industry requires components that offer high strength, lightweight, and precision. Lost foam casting meets these requirements, making it an ideal process for aerospace applications.
Key Components in Aerospace
- Turbine Blades
- Material: Nickel-based superalloys
- Benefits: High temperature resistance, excellent mechanical properties
- Engine Housings
- Material: Titanium alloys
- Benefits: High strength-to-weight ratio, corrosion resistance, high temperature tolerance
- Structural Components
- Material: Aluminum alloys
- Benefits: Lightweight, high strength, easy to machine and fabricate
Advantages in Aerospace Manufacturing
- Precision Casting: Achieves tight tolerances and high-quality surface finishes.
- Reduced Weight: Produces lightweight components essential for fuel efficiency and performance.
- Enhanced Durability: Provides materials with high resistance to extreme conditions.
Advancements in Lost Foam Casting Technology
Recent advancements in lost foam casting technology have further enhanced its applications in the electric vehicle and aerospace industries.
High-Performance Materials
- Advanced Alloys: Development of new alloys with superior mechanical properties and thermal stability.
- Composite Materials: Integration of composite materials for improved strength and reduced weight.
Process Innovations
- Automated Casting Systems: Implementation of automation for increased precision and efficiency.
- Improved Coating Techniques: Enhanced refractory coatings for better surface finish and reduced casting defects.
- Simulation Software: Advanced simulation tools for optimizing casting processes and reducing trial-and-error.
Environmental Benefits
- Reduced Waste: The precision of lost foam casting minimizes material waste.
- Energy Efficiency: The process consumes less energy compared to traditional casting methods.
- Recyclability: Castings produced can be recycled, promoting sustainability.
Tables for Key Components and Benefits
Table 1: Key Components in Electric Vehicles
Component | Material | Benefits |
---|---|---|
Battery Housings | Aluminum alloys | Lightweight, excellent thermal conductivity, high strength |
Motor Housings | Magnesium alloys | Low weight, high strength-to-weight ratio, corrosion resistance |
Suspension Components | High-strength steel | Enhanced durability, reduced weight, improved vehicle dynamics |
Table 2: Key Components in Aerospace
Component | Material | Benefits |
---|---|---|
Turbine Blades | Nickel-based superalloys | High temperature resistance, excellent mechanical properties |
Engine Housings | Titanium alloys | High strength-to-weight ratio, corrosion resistance, high temperature tolerance |
Structural Components | Aluminum alloys | Lightweight, high strength, easy to machine and fabricate |
Lists for Advantages in Manufacturing
Advantages in Electric Vehicle Manufacturing
- Lightweight components reduce overall vehicle weight.
- Complex geometries enhance performance and functionality.
- Cost-effective production lowers manufacturing costs.
Advantages in Aerospace Manufacturing
- Precision casting achieves tight tolerances and high-quality surface finishes.
- Reduced weight produces lightweight components essential for fuel efficiency and performance.
- Enhanced durability provides materials with high resistance to extreme conditions.
Conclusion
Lost Foam Casting plays a crucial role in the electric vehicle and aerospace industries, providing an efficient and effective method for producing high-quality, lightweight, and complex components. The advancements in materials, process innovations, and environmental benefits further solidify its importance in modern manufacturing. As these industries continue to evolve, lost foam casting will remain a pivotal technology driving innovation and excellence in component production.