Lost foam casting has seen several innovations and advancements over the years, which have further improved its efficiency, accuracy, and capabilities. Here are some notable innovations in the lost foam casting industry:
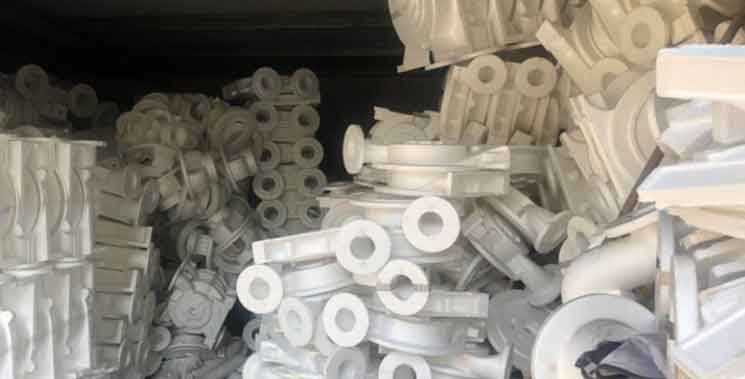
- Foam Pattern Technology: Advancements in foam pattern technology have led to the development of more precise and durable foam patterns. High-quality foams with improved thermal properties and dimensional stability are now available, enabling the production of more intricate and complex designs.
- Digital Design and Simulation: The use of advanced computer-aided design (CAD) software and simulation tools has revolutionized the lost foam casting process. These tools allow for virtual modeling, analysis, and optimization of the casting process, enabling designers and engineers to identify potential issues and make improvements before the actual casting takes place.
- Refractory Coatings: Innovations in refractory coating materials and application techniques have improved the quality and consistency of the coatings on foam patterns. New formulations provide better dimensional accuracy, enhanced surface finish, and improved resistance to thermal degradation during the casting process.
- Automated Pouring Systems: Automated pouring systems have been introduced to enhance the accuracy and repeatability of metal pouring in lost foam casting. These systems precisely control the pouring parameters, such as metal temperature, flow rate, and timing, resulting in consistent and high-quality castings.
- Real-time Process Monitoring: Advanced sensors and monitoring technologies allow for real-time monitoring of key process parameters during lost foam casting. This enables operators to make immediate adjustments if any deviations or anomalies are detected, ensuring optimal casting conditions and reducing the risk of defects.
- Additive Manufacturing and 3D Printing: The integration of additive manufacturing and 3D printing technologies with lost foam casting has opened up new possibilities in pattern creation. Complex foam patterns can now be produced directly from digital designs, eliminating the need for traditional pattern-making techniques and reducing lead times.
- Quality Control and Inspection Techniques: Non-destructive testing (NDT) methods, such as X-ray inspection and ultrasonic testing, have become more advanced and widely used in lost foam casting. These techniques enable the detection of internal defects and ensure the integrity and quality of the castings.
- Material Development: The development of new materials and alloys suitable for lost foam casting has expanded the range of applications and industries that can benefit from the process. This includes the use of specialized alloys with improved mechanical properties, heat resistance, and corrosion resistance.
These innovations and advancements in lost foam casting have resulted in improved casting accuracy, enhanced surface finish, reduced lead times, and increased productivity. They have also expanded the range of applications for lost foam casting, making it a viable and competitive option in various industries, including automotive, aerospace, and general engineering. As technology continues to evolve, further advancements can be expected, driving the efficiency and capabilities of lost foam casting even higher.