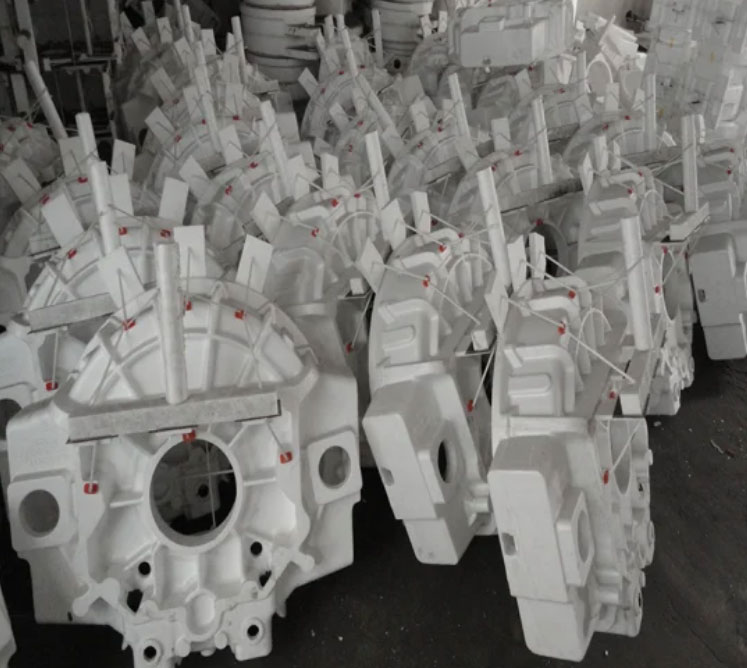
Lost foam casting has emerged as a significant player in meeting industry demands for lightweight components in various sectors. As industries increasingly prioritize weight reduction for improved performance, fuel efficiency, and sustainability, lost foam casting offers a competitive advantage due to its ability to produce complex, lightweight, and optimized designs. Here’s how lost foam casting meets industry demands for lightweight components:
1. Intricate Design Flexibility:
- Lost foam casting allows for intricate and complex designs, including thin walls, internal features, and intricate geometries. This design flexibility enables the creation of lightweight components with enhanced structural integrity and reduced material usage.
2. Near Net Shape Casting:
- Lost foam casting produces near net shape castings, minimizing the need for post-casting machining or material removal. This results in reduced material waste and optimized component weight.
3. Hollow and Cored Structures:
- Lost foam casting enables the creation of components with internal cavities, reducing weight without compromising structural integrity. Hollow or cored structures offer a high strength-to-weight ratio, making them ideal for lightweight applications.
4. Consolidation of Parts:
- Lost foam casting allows for the integration of multiple components into a single casting. This consolidation reduces the number of separate parts and associated fasteners, further contributing to weight reduction.
5. Lightweight Materials:
- Lost foam casting is compatible with a wide range of lightweight materials, such as aluminum and magnesium alloys. These materials offer excellent strength-to-weight ratios and are ideal for applications where weight reduction is critical.
6. Reduced Machining and Assembly:
- Near net shape castings from lost foam casting require minimal machining and assembly, reducing material waste and energy consumption during manufacturing.
7. Enhanced Performance in Aerospace and Automotive:
- Lost foam casting finds significant applications in the aerospace and automotive industries, where weight reduction is crucial for improved fuel efficiency, performance, and payload capacity.
8. Versatility in Industry Applications:
- Lost foam casting’s ability to produce lightweight, intricate components makes it suitable for various industries, including aerospace, automotive, marine, industrial machinery, and consumer goods.
9. Rapid Prototyping and Design Iteration:
- The ease of creating foam patterns allows for rapid prototyping and design iteration, enabling quick optimization of component designs for improved lightweight performance.
10. Integration with Other Lightweight Technologies:
- Lost foam casting can be seamlessly integrated with other lightweight technologies, such as composite materials, to further enhance weight reduction and component performance.
As industries continue to prioritize lightweighting strategies, lost foam casting will play a vital role in meeting these demands by enabling the production of lightweight, intricate, and high-performance components. Its design flexibility, near net shape capabilities, and suitability for lightweight materials position lost foam casting as a valuable solution to meet the challenges of weight reduction in modern engineering applications.