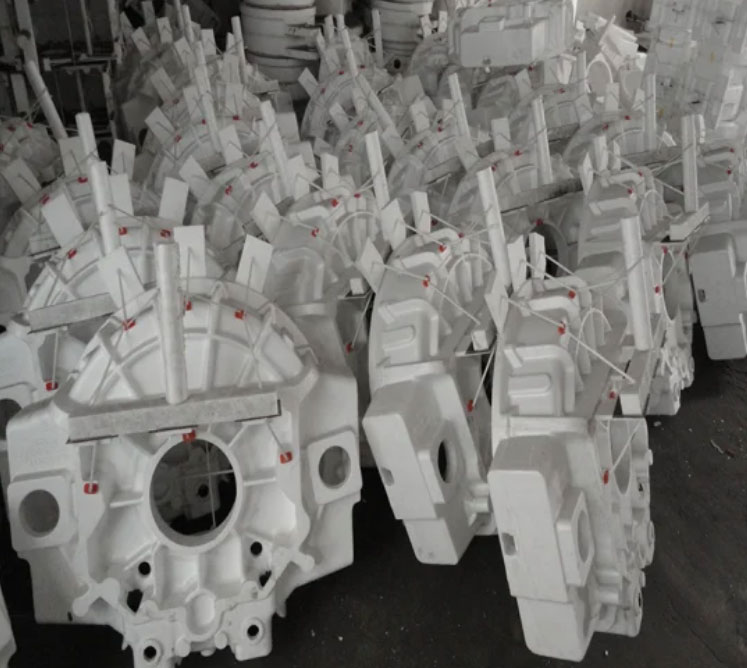
Choosing between lost foam casting (LFC) and sand casting depends on the specific requirements and characteristics of your project. Each casting method has its strengths and trade-offs, so it’s essential to consider various factors to make an informed decision. Let’s compare lost foam casting and sand casting:
Lost Foam Casting (LFC):
Advantages:
- Design Complexity: LFC allows for the production of complex and intricate geometries with fine details, undercuts, and thin walls. It provides designers with significant design freedom.
- Dimensional Accuracy: Foam patterns in LFC result in precise and consistent castings, reducing the need for extensive post-casting machining.
- Reduced Tooling Costs: Foam patterns are cost-effective and easy to produce, leading to lower tooling expenses compared to traditional sand casting.
- Surface Finish: LFC can achieve a smoother and high-quality surface finish, reducing the need for additional surface finishing operations.
- Single-Piece Castings: LFC can produce intricate components as a single piece, eliminating the need for assembly and minimizing assembly-related defects.
Trade-offs:
- Material Limitations: LFC is primarily used for non-ferrous metals like aluminum and some cast iron alloys. It may not be suitable for all materials.
- Equipment Requirements: LFC requires specialized equipment for foam pattern production and handling.
- Pattern Coating: Proper pattern coating is critical to prevent defects like veining and ensure a successful casting.
Sand Casting:
Advantages:
- Material Versatility: Sand casting can handle a wide range of metals, including ferrous and non-ferrous materials, making it suitable for diverse applications.
- Cost-Effective for Large Parts: Sand casting can be more cost-effective for larger and bulkier parts.
- Suitable for High Production Volume: Sand casting is well-suited for high production volumes, making it economically viable for mass production.
- Simple Tooling and Equipment: Sand casting uses basic tools and equipment, making it more accessible to smaller foundries.
Trade-offs:
- Design Constraints: Sand casting may have limitations in producing intricate and complex geometries due to the nature of sand molds.
- Dimensional Tolerance: Sand casting may have looser dimensional tolerances, requiring more post-casting machining.
- Surface Finish: Sand casting may result in a rougher surface finish, necessitating additional surface finishing operations.
- Mold Complexity: For more complex parts, sand molds can be challenging to produce and may require additional cores.
Choosing the Right Method:
Consider the following when choosing between LFC and sand casting:
- Design Complexity: If your project requires intricate and complex geometries, LFC may be the better choice.
- Material Requirements: Consider the specific material properties and if it is compatible with either casting method.
- Volume and Cost: For higher production volumes, sand casting might be more cost-effective, while LFC is suitable for smaller production runs and rapid prototyping.
- Tolerance and Surface Finish: Evaluate your project’s dimensional tolerance requirements and surface finish specifications.
- Equipment and Expertise: Consider the available equipment and expertise at your disposal for each casting method.
Ultimately, selecting the right casting method depends on the specific needs of your project, budget constraints, desired complexity, and the foundry’s capabilities. Consulting with experienced foundries and casting experts can help you make the best decision for your application.