Lost foam casting is a new casting technology developed in the early 1980s. Because of its simple production process, good surface quality of castings and less machining allowance, it is a casting technology with near clean production and development prospects, and is known as “new casting technology in the 21st century”. The technology uses foam.
The plastic is made of foam pattern similar to the size of the casting, coated with suitable refractory binder, dried by the coating, embedded in special sand box, dry sand molding, through two dimensional or three dimensional micro vibration compaction, and poured under certain negative pressure conditions, so that the foam pattern is heated and gasified and decomposed and replaced by molten metal. After cooling, it is obtained by micromachining or non processing, which is the same as the product structure. A new casting process for castings with the same size.
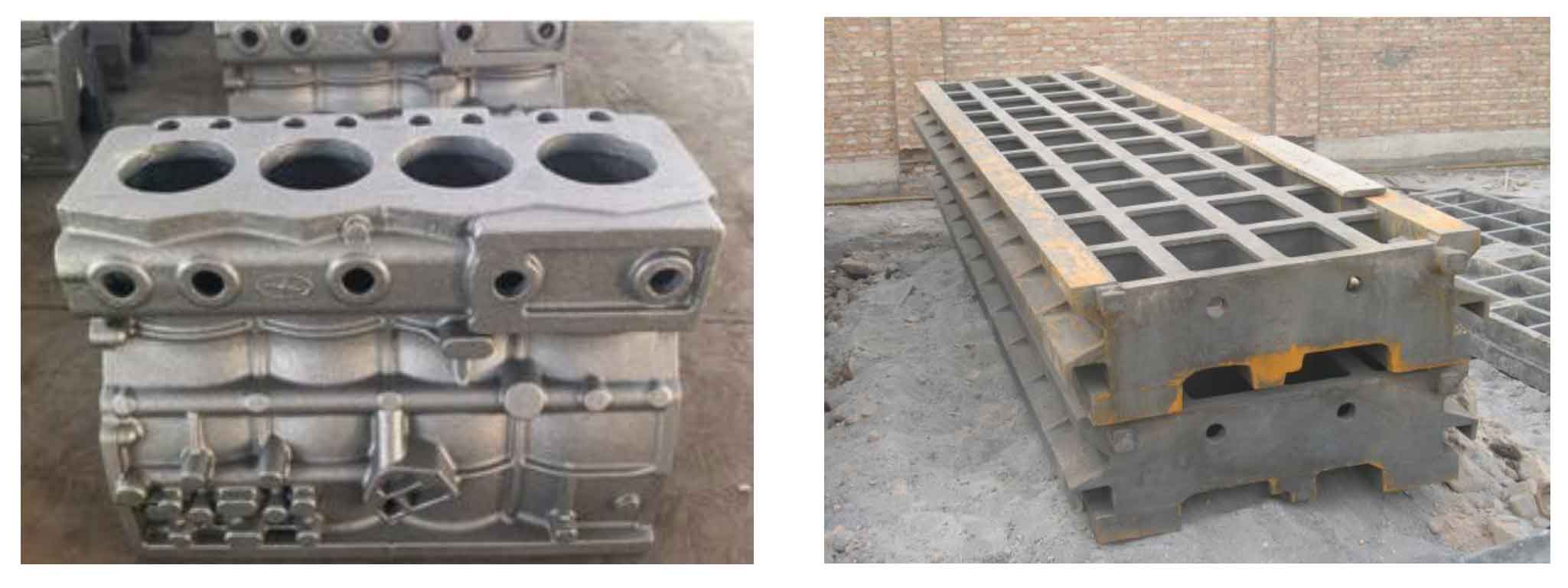
Compared with the traditional sand casting, the casting structure design of lost foam casting is flexible, which can integrate multiple parts produced in sand casting into a single piece and cast at one time. It is not only suitable for the single small batch production of small and medium-sized castings with complex appearance, but also suitable for the mass production of castings that are difficult to be completed by traditional casting methods, such as complex box Shell and tube castings (Figure 1). Therefore, lost foam casting provides a new method for the workpiece that is difficult to be cast by traditional casting.
Although lost foam casting has many advantages, it has been widely applied at home and abroad. However, lost foam casting process has its own shortcomings and shortcomings. For example, foam pattern clusters should be processed through foaming, bonding and combination processes. Not only the size of inner gate is relatively large, but also difficult to clean up, and the use of vibration modeling can easily cause deformation of foam pattern and affect casting. During the casting process of lost foam casting, the liquid metal at the filling front will be bioized with foam mold, and the solidification process will be relatively unique under dry sand negative pressure conditions, which may bring new defects such as collapse, sand sticking, cold separation, carburization, wrinkling, porosity and slag inclusion. Moreover, China’s lost foam casting is still in the initial development, and there is no mature experience and technology in the selection of lost foam casting process parameters and the design of gating and riser. Compared with traditional casting methods, lost foam casting is more difficult to determine its reasonable process scheme and the implementation of quality control. If the “trial and error method” is used to determine the casting process parameters, the cost of investment will be higher, and even the early investment and efforts may be wasted due to the inability to meet the casting quality requirements. In recent years, the rapid development of casting simulation technology can directly see the whole casting process with the naked eye through computer calculation and simulation, which is convenient for casting technicians to accurately predict casting defects and optimize the casting process. It can minimize the number of trial production of products in the development stage and greatly reduce the production risk and capital investment of castings. Studying the application of simulation technology in lost foam casting process and replacing “manual trial and error pouring method” with “computer simulation trial casting process” (as shown in Figure 2) is of great significance to the development of lost foam casting Technology in China.
Compared with manual trial casting and computer simulation, it is not limited by the production experimental conditions. It can analyze the influencing factors of mold filling process and solidification process quantitatively and qualitatively. lost foam casting simulation technology can effectively improve the rationality of product process design, simplify the trial production process of castings, shorten the manufacturing cycle of castings, reduce the trial production cost, and improve the production and development efficiency of enterprises. Therefore, promoting the application of casting simulation technology in the actual production of casting industry is an effective way to speed up the innovation of casting products and the independent development system of enterprises.