Lost foam casting, like any casting process, presents its own set of challenges that need to be overcome to ensure high-quality castings. Here are some common challenges in lost foam casting and strategies to enhance quality control:
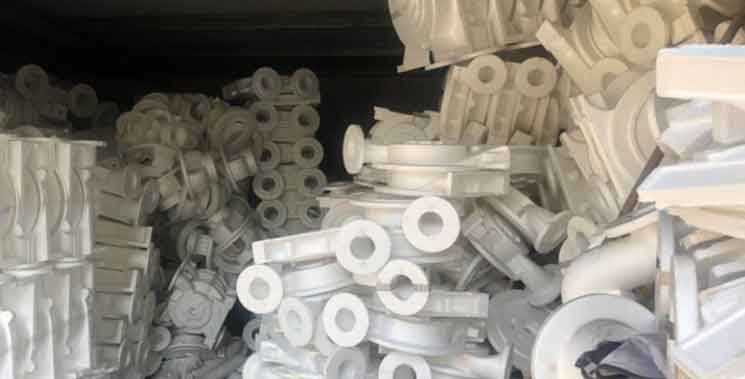
- Pattern Quality and Stability:
- Use high-quality foam patterns with consistent density, dimensional accuracy, and low decomposition rates.
- Implement proper storage and handling practices to prevent pattern damage or distortion.
- Mold Preparation:
- Ensure proper mold coating application to enhance surface finish and prevent defects like metal penetration.
- Implement effective mold drying techniques to control moisture content and prevent gas-related defects.
- Pattern Removal:
- Develop controlled and efficient pattern removal techniques to avoid mold damage or distortion.
- Utilize vibration or pneumatic methods to facilitate pattern removal without causing erosion or mold wear.
- Mold Venting:
- Optimize vent placement and size to allow for the escape of gases generated during pouring.
- Regularly inspect and clean vents to prevent blockages and ensure proper gas evacuation.
- Pouring Parameters:
- Control pouring temperature to prevent metal overheating or underheating, which can lead to defects.
- Optimize pouring rate and time to achieve complete filling while minimizing turbulence.
- Gating and Riser Design:
- Design gating systems to ensure smooth metal flow and avoid turbulence.
- Position risers properly to provide adequate feeding and minimize shrinkage-related defects.
- Metal Quality and Treatment:
- Use high-quality molten metal with proper alloy composition and appropriate treatment processes.
- Implement degassing and filtration techniques to remove impurities and minimize gas and inclusion defects.
- Solidification Control:
- Utilize cooling techniques, such as controlled cooling rates or the use of chills, to optimize solidification.
- Monitor and control solidification parameters to minimize shrinkage and thermal stress-related defects.
- Quality Control and Inspection:
- Implement rigorous inspection procedures to detect and address defects.
- Use non-destructive testing methods, such as X-ray or ultrasonic testing, to identify internal defects.
- Training and Continuous Improvement:
- Provide comprehensive training to personnel involved in the lost foam casting process to ensure proper technique and awareness of quality requirements.
- Continuously analyze and evaluate casting results, feedback, and data to identify areas for improvement and optimize the process.
By addressing these challenges and implementing effective quality control measures, it is possible to enhance the overall quality of lost foam castings, minimize defects, and ensure consistent production of high-quality components.