Lost foam casting, a revolutionary casting technology in the 21st century, has been widely adopted in various industries. This article aims to provide a comprehensive understanding of the lost foam casting process and its engineering design details.
I. Introduction
Lost foam casting, also known as full-mold casting, is a novel casting method where a foam plastic model, similar in size and shape to the casting to be produced, is bonded together to form a model cluster. After being coated with a refractory coating and dried, it is buried in dry quartz sand for vibration molding. Under negative pressure, the liquid metal is poured, causing the model to gasify and the liquid metal to take its place. Once cooled and solidified, the desired casting is formed.
II. Development History of Lost Foam Casting
The history of lost foam casting can be traced back to 1956 when an American, H.F. Shroyer, began experiments with using polystyrene foam for casting and achieved success, which aroused great interest. In 1958, it was patented and initially called “cavityless casting”. Initially, this method was mainly used to produce metal statues and other art 铸件. Later, in 1962, 西德 introduced the patent from the United States and began to develop and apply it industrially.
In 1964, an American, T.R. Smith, patented the use of dry sand without binders for molding to produce lost foam castings. However, until 1967, the lost foam casting method using ordinary clay sand and self-hardening sand was successful and applied in many countries, producing thousands of tons of castings. But the dry sand solid-molding without binders was still in the exploration stage. Throughout the 1960s and 1970s, lost foam casting was limited to single-piece and small-batch production, with typical products being automotive molds, machine bases, and artworks.
In 1968, a German, E. Kryzmowski, obtained a patent for pouring in a sand box with negative pressure, which is the current lost foam casting. Due to patent restrictions in the early 1980s, the use of dry sand without binders in lost foam casting was limited; there was insufficient coordination between the foundry industry and other industrial sectors; and due to improper processes, inappropriate mold sand and coatings, and poor model quality, the appearance and internal quality of solid-mold castings were not good enough, resulting in some people’s wait-and-see or even skeptical attitudes, which led to the slow development of lost foam casting.
After 1981, with the expiration of the corresponding patent technology, and after several years of efforts, significant technological advancements such as improved raw materials of expanded polystyrene beads, improved quality of model combination binders, and the development of high-quality coatings, the lost foam casting method developed rapidly and was soon applied in production. In 1982, the United States publicly disclosed the world’s first production line for complex aluminum castings using the lost foam casting process. Since then, lost foam casting, as a completely new casting process method, has been applied in production.
In China, in 1979, a research group led by Professor Huang Shuzhe, a renowned expert in lost foam casting in China and a researcher at the Changchun Institute of Optics, Fine Mechanics and Physics of the Chinese Academy of Sciences, started the principle tests of lost foam casting in China. In the same year, Professor Huang Shuzhe published a paper report on “Research on the Basic Characteristics of Lost Foam Casting” at the National Foundry Technology Conference, systematically expounding the characteristics and regularities of this method for the first time in China. In 1982, based on a large number of laboratory experiments, Professor Huang Shuzhe presided over the establishment of a lost foam casting pilot production line in the factory of the Institute of Optics. The project “Development and Industrial Application of Lost Foam Casting Technology” led by Professor Huang Shuzhe won the second prize of the Science and Technology Progress Award of the Chinese Academy of Sciences in 1997 and the third prize of the National Science and Technology Progress Award in 1998, which is the highest award in the scientific and technological achievements of China’s foundry industry. Professor Huang Shuzhe presided over the completion of dozens of advanced, functional, well-configured, and highly efficient lost foam casting production line projects.
In the late 1980s, the Zhengzhou Institute of Machinery also began the experimental application and research of lost foam casting. Since the 1990s, Tsinghua University, Harbin Institute of Technology, Huazhong University of Science and Technology, Xi’an Jiaotong University, and other institutions have also joined the research of lost foam casting. In 2013, China’s first 10,000-ton lost foam steel casting production line was officially put into operation, marking the official entry of China’s lost foam steel casting manufacturing industry into the era of mass production.
III. Production Principle of Lost Foam Casting
The production principle of this method is as follows: First, a foam plastic model is made according to the process requirements, and then a special high-temperature-resistant coating is applied and dried. It is then placed in a special sand box, filled with dry sand, and vibrated and compacted in three dimensions. Under negative pressure, the molten metal is poured into the mold. At this time, the model gasifies and disappears, and the liquid metal replaces the model, replicating a casting that is the same as the foam plastic model.
IV. Lost Foam Casting Process
- Selection of Foam Beads for Lost Foam Casting
There are three types of special foam beads for lost foam casting:
- Expandable polystyrene resin beads (EPS): suitable for non-ferrous metals, gray iron, and general steel castings.
- Expandable methyl methacrylate and styrene copolymer resin beads (STMMA): suitable for gray iron, low-carbon steel, and alloy steel castings.
- Expandable polymethyl methacrylate resin beads (EPMMA): suitable for ductile iron, malleable iron, low-carbon steel, alloy steel, and stainless steel castings.
The characteristics of these beads are semi-transparent, with a pre-expansion multiple of 40-60, and a particle size of 0.18-0.80 mm (6 sizes). Generally, the selected original bead particle size is less than or equal to 1/9-1/10 of the minimum wall thickness of the casting.
- Model Making
There are two situations:
- Made from foam beads: pre-expansion – aging – foam molding – cooling and demolding
- Pre-expansion: Before adding EPS beads to the mold, pre-expansion is required to expand the beads to a certain size. The pre-expansion process determines the density, size stability, and accuracy of the model, which is one of the key links. There are three methods suitable for EPS bead pre-expansion: hot water pre-expansion, steam pre-expansion, and vacuum pre-expansion. The bead expansion rate of vacuum pre-expansion is high, and the beads are dry, so it is more widely used.
- Aging: The pre-expanded EPS beads are placed in a dry and ventilated material bin for a certain period to balance the pressure inside and outside the bead pores, give the beads elasticity and re-expansion ability, and remove the moisture on the bead surface. The aging time is 8-48 hours.
- Foam molding: The pre-expanded and aged EPS beads are filled into the cavity of the metal mold, heated to make the beads expand again, fill the gaps between the beads, and make the beads fuse with each other to form a smooth surface, that is, the model. Cooling must be performed before demolding to reduce the model temperature below the softening temperature, so that the model hardens and takes shape before demolding. There are two types of equipment for this process, namely, steam cylinder and automatic molding machine.
- Made from foam plates: foam plates – resistance wire cutting – bonding – model
- For simple models, a resistance wire cutting device can be used to cut the foam plates into the required models.
- For complex models, first, a resistance wire cutting device is used to cut the model into several parts, and then they are bonded together to form an overall model.
- Model Combination into Clusters
This is to combine the self-processed (or purchased) foam models with the gating and risering models and bond them together to form a model cluster. This combination can be carried out either before coating or during the process of coating preparation and embedding the box for molding. It is an indispensable process in lost foam (solid) casting.
Currently used bonding materials include rubber latex, resin solvents, hot melt adhesives, and adhesive tapes.
- Model Coating
It is necessary to apply a certain thickness of coating on the surface of the solid casting foam model to form the inner shell of the mold. The role of this coating is to improve the strength and stiffness of the EPS model, enhance the model’s ability to resist the erosion of the mold sand, prevent the model surface from being damaged during the process of adding sand, and ensure the dimensional accuracy of the casting during vibration molding and negative pressure shaping.
For the purchased special coating for lost foam casting, water is added in the coating mixer to obtain an appropriate viscosity. For black metals with high temperatures, coarser sand can be selected, while for aluminum alloys, finer sand is used.
The model cluster is coated by immersion, brushing, spraying, or pouring methods. Generally, two coats are applied to make the coating thickness 0.5-2 mm, which is selected according to the alloy type, structure, and size of the casting. The coating is dried at 40-50°C.
- Vibration Molding
Here is a commonly used molding method (one of the two methods):
The process includes the following steps: sand bed preparation – placing the EPS model – filling sand – sealing and shaping- Sand bed preparation: Place the sand box with a vacuum chamber on the vibration table and fasten it tightly. A certain thickness of bottom sand is placed at the bottom (generally, the sand bed thickness is more than 50-100 mm), and vibration compaction is carried out.
- Placing the EPS model: After vibration compaction, place the EPS model group on it according to the process requirements and fix it with sand.
- Filling sand: Add dry sand (several sand-filling methods) while applying vibration in three directions (X, Y, and Z) for generally 30-60 seconds to make the mold sand fill all parts of the model and increase the bulk density of the mold sand.
- Sealing and shaping: Seal the surface of the sand box with a plastic film, and use a vacuum pump to draw a certain vacuum in the sand box. The difference between the atmospheric pressure and the pressure in the mold is relied on to “bond” the sand particles together to maintain the integrity of the mold during the pouring process, which is called “negative pressure shaping” and is more commonly used.
- Pouring and Replacement
The EPS model generally softens at about 80°C and decomposes at 420-480°C. The decomposition products include gas, liquid, and solid parts. Different thermal decomposition temperatures result in different contents of these three parts.
During the solid casting pouring, under the thermal effect of the liquid metal, the EPS model undergoes thermal decomposition and gasification, generating a large amount of gas, which continuously passes through the coating mold sand and is discharged outward, forming a certain pressure within the mold, model, and metal gap. The liquid metal continuously takes the place of the EPS model and moves forward, resulting in the replacement process between the liquid metal and the EPS model. The final result of this replacement is the formation of the casting.
The pouring operation process adopts the method of slow – fast – slow. And continuous pouring should be maintained to prevent the interruption of the pouring process. After pouring, the vacuum of the mold is maintained for 3-5 minutes before the pump is stopped. The pouring temperature is 30-50°C higher than that of the sand mold casting.
- Cooling and Cleaning
After cooling, the sand removal in solid casting is the simplest. The castings can be lifted out of the sand box by tilting the sand box or directly lifted out of the sand box, and the castings and dry sand are naturally separated. The separated dry sand is treated and reused.
V. Characteristics of Lost Foam Casting
Compared with traditional casting technologies, lost foam casting has the following remarkable characteristics:
- Good casting quality and low cost.
- Unlimited material types, suitable for various sizes of castings.
- High precision, smooth surface, reduced cleaning, and saved machining.
- Greatly reduced internal defects, and dense castings.
- Capable of large-scale and mass production.
- Applicable to the mass production of the same castings.
- Suitable for both manual operation and automated assembly line production and operation control.
- The production status of the production line meets the technical parameter requirements for environmental protection.
- Can significantly improve the working environment and production conditions of the casting production line, reduce labor intensity, and decrease energy consumption.
VI. Engineering Design of Lost Foam Casting
- Lost Foam Casting Process Characteristics
Lost foam casting bonds and combines paraffin or expanded resin models similar in size and shape to the casting into a model cluster, coats it with a refractory coating, dries it, and then buries it in dry quartz sand for vibration molding. Under negative pressure, the model gasifies, the liquid metal takes its place, and after solidification and cooling, the casting is formed. Compared with the common sand mold casting process in the foundry industry, the characteristics of the lost foam casting process are as follows:- It can use the combination of foam plastics to produce castings of different shapes and sizes, freely design the casting structure, and produce complex products. Especially suitable for the production of castings with difficult demolding, such as multi-edge, multi-core, and complex geometric shapes. Currently, it is the main casting process for motor shell castings.
- Generally, the sand core is required for complex castings in the green sand casting process, and harmful flue gas is often generated during the sand core preparation process. Among them, the technology for treating the triethylamine tail gas generated by the cold core making process is becoming more and more mature and can be effectively treated. However, it is very difficult and costly to completely treat the smoke, organic waste gas, and odor generated by the hot core. The lost foam casting process does not require a sand core, which is a clean and environmentally friendly casting process.
- There is no chemical binder in the lost foam molding sand, and the old sand recovery rate is high, usually reaching more than 90%, which meets the current strict environmental protection requirements. The energy consumption cost savings rate in casting production is about 15%, and the casting cost is reduced by about 30%.
- The castings produced by the lost foam casting process have no flash, burrs, or draft angles, with high casting dimensional accuracy, less reserved machining allowance, and the cleaning and grinding workload is reduced by more than 50%. Moreover, the surface quality of the castings is good.
- Generally, the equipment investment for lost foam casting is relatively low, which can be reduced by 30%-50% compared with sand mold casting.
According to the characteristics of the lost foam casting process, its production area is mainly divided into the white area, gray area, and black area. The process flow chart of lost foam casting is shown in Figure 1.
The white area and gray area of the lost foam workshop are generally set in one place and are called the mold-making workshop, which is a unique workshop in the lost foam casting process. Its main function is to produce qualified mold clusters. It includes processes such as pre-foaming of bead particles, aging after pre-foaming, mold piece making, mold piece aging, gluing, coating, and drying. There are many forms of pre-foaming, including hot water pre-foaming, steam pre-foaming, and vacuum pre-foaming, among which steam pre-foaming is commonly used. When making mold pieces, steam is passed into the mold to heat the beads, so that the foam softens and expands to fill all the gaps in the mold cavity and adheres to form a whole.
The black area of the lost foam workshop is similar to the sand mold workshop, including the melting department, molding department, sand processing department, and cleaning department, and is generally called the lost foam workshop.
The characteristic of lost foam molding is to fill the sand box with dry sand and use a vacuum pump to draw negative pressure to form a solid mold. The molding process is as follows: adding bottom sand and vibrating and compacting – installing the mold cluster – adding sand and vibrating and compacting on the molding vibrating table – covering the film and adding sand on the cover – adding the gating cup – pouring – cooling – turning the box – sand falling and conveying – vibrating conveyer trough – taking out the casting.
The sand used for sand processing is dry sand without any additives, and the equipment is simple. The dry sand processing process is as follows: hydraulic box-turning machine – vibrating conveyer sand-falling trough – high-temperature-resistant bucket elevator – vibrating sand-falling screen – magnetic separator – automatic sand-feeding gate – air-cooled bed – bucket elevator – intermediate sand bin (upper and lower material level gauge) – bucket elevator – sand temperature regulator – automatic sand-feeding gate – bucket elevator – molding sand bin.
There is no core-making department in the lost foam workshop, and the melting department and cleaning department are similar to those in common sand mold workshops.
- Engineering Design Key Points of Lost Foam Casting
Lost foam casting process uses a large amount of resin-based raw materials, and the fire risk is relatively high. Fire protection design is related to whether the project can be successfully accepted by the government, which is an important factor that must be considered in the design. Among them, the fire risk level of the mold-making workshop is higher than that of the lost foam workshop, and the requirements for fire protection design are different, and the investment is also quite different. Based on this, in the engineering design of a new lost foam casting plant, it is inclined to set the mold-making workshop and the lost foam workshop as independent building sub-items to reduce the fire protection design cost of the lost foam workshop.
2.1.2 Layout of the Mold-making Workshop Building
The processes such as mold piece making equipment, mold piece aging, gluing, coating, and drying all require a large area, but the process equipment is generally not high. Therefore, the mold-making workshop is generally designed as a multi-story factory building, and elevators are set up to transport mold pieces up and down. Multi-story factory buildings can effectively reduce the project land area and maintain the same height as the lost foam workshop. The height of the workshops in the factory area is coordinated and beautiful. According to previous design experience, it is more appropriate to design the mold-making workshop as a three-story building.
The mold piece forming equipment is the core process equipment in the mold-making workshop. For products with large quantities, complex shapes, high casting dimensional accuracy and surface quality requirements, the high-temperature steam foaming forming process is generally selected. This process requires a large amount of high-temperature steam, and the drainage volume is large after the steam condenses. Moreover, the mold piece forming equipment needs a crane to change the mold. Therefore, the pre-foaming of bead particles, the aging after foaming, and the mold piece forming equipment are arranged on the first floor of the workshop.
The top floor can be set as a sunroom to complete the mold piece aging treatment with the help of solar energy, saving energy. And the white molds that have completed the aging treatment can be glued on the top floor.
The middle floor can be arranged with white mold coating and drying, and the mold cluster sending area. And it is more appropriate to automatically transport the mold cluster to the lost foam workshop by a suspension chain at the height of the second floor. A fireproof separation water curtain needs to be set up in the corridor between the mold-making workshop and the lost foam workshop. The boiler room is arranged near the mold-making workshop to provide qualified steam for bead pre-foaming and mold piece forming machines.
Figures 2, 3, and 4 show the schematic diagrams of the process plane layering of the mold-making workshop of a certain project.
2.2 Lost Foam Workshop
According to Article 3.1.1 of the “Code for Fire Protection Design of Buildings”, the production fire hazard of the lost foam workshop is Class D, and the workshop fire resistance rating is Class II.
The differences between the lost foam workshop and the sand mold casting process are mainly reflected in the molding department and the sand processing department.
2.2.1 Layout of the Molding Line in the Lost Foam Workshop
The core equipment of the molding line is the molding vibrating table, which enables the dry sand to quickly reach all parts of the pattern to form an appropriate compactness. During this process, the deformation of the mold cluster is small, ensuring the dimensional accuracy of the casting. When producing castings with high quality requirements, the requirements for the vibrating table are also relatively high. Pouring is usually carried out under negative pressure. The negative pressure makes the loose dry sand in the sand box form a hard mold with sufficient compressive strength to resist the action of the metal liquid. Moreover, this pressure difference can enhance the gas discharge effect after the mold cluster gasifies. Therefore, the lost foam workshop needs to be arranged with a vacuum pump room and should be arranged near the vacuum point.
2.2.2 Sand Processing Department in the Lost Foam Workshop
The molding sand is dry sand, and its cooling method is different from that of the green sand. The sand processing department in the lost foam workshop is arranged near the cooling equipment to provide circulating cooling water to cool the high-temperature sand. Advanced molding line equipment manufacturers generally arrange the molding and sand processing in a circular manner.
In conclusion, with the increasing maturity of the lost foam casting process and the characteristics of low investment and strong product adaptability of the lost foam casting workshop, there are more and more lost foam casting projects. The requirements for the engineering design of lost foam casting are also getting higher and higher. In the engineering design of lost foam casting, special attention should be paid to the following points: 1) The mold-making workshop should pay special attention to the impact of its fire hazard level on engineering design and project cost. At the beginning of the engineering design, it is necessary to communicate well with the local fire department to facilitate the completion of the project’s fire protection acceptance and other work as soon as possible; 2) The mold cluster pouring should be carried out under negative pressure, and a vacuum pump room should be established and the vacuum point should be set reasonably; 3) The sand processing department should be arranged near the cooling equipment to provide circulating cooling water to effectively cool the high-temperature sand. At present, the automation level of the mold-making workshop is relatively low, and future engineering design needs to focus on how to improve the automation level of the mold-making workshop.
This article comprehensively expounds the lost foam casting process and its engineering design key points, hoping to provide valuable references and guidance for the development and design of the lost foam casting industry.
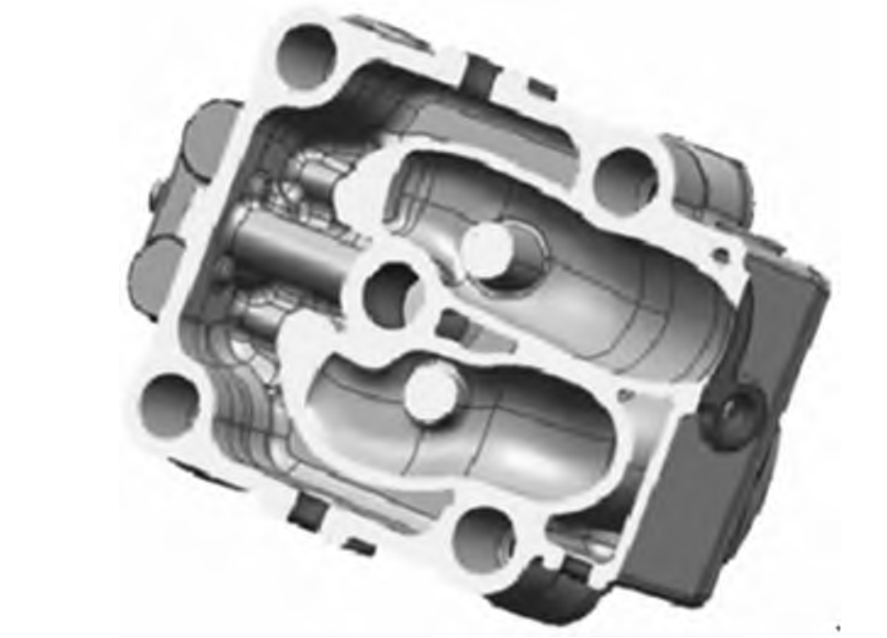