In order to ensure the quality of ductile iron castings, it is required to strictly control the mold assembly, dip coating and pouring links in the new process commissioning stage, and strictly track and guide the process indicators such as the size of the pouring system used for mold assembly, the Baume degree of the coating, the drying temperature (humidity) of the yellow mold, the drying time, and the pouring temperature, so as to ensure that each process is operated according to the process requirements.
Because the size of sand box of ZHY Casting lost foam mold plant is 1200 mm × 1 000 mm × 1 300 mm, one box for one molding, the total mass of molten iron poured is 310 kg, 700 kg spheroidizing bag is used for production, and two boxes are poured for one package of molten iron. The spheroidizing treatment of molten iron adopts the double-wire process of cover feeding and spheroidizing, the spheroidizing agent is FeSiMg25Re3, the addition amount is 0.7%, and the inoculation in the ladle adopts 0.3% pretreatment agent and 0.2% 75FeSi composite inoculation. Since the spheroidizing agent is wrapped in the steel sheet to avoid being oxidized, the wire feeding length and wire feeding speed are controlled by PLC and directly enter into the bottom of the molten iron. The alloy absorption rate is high and the spheroidizing effect is good. After spheroidizing, the molten iron is quickly skimmed, transported to the pouring station by forklift, and poured manually.
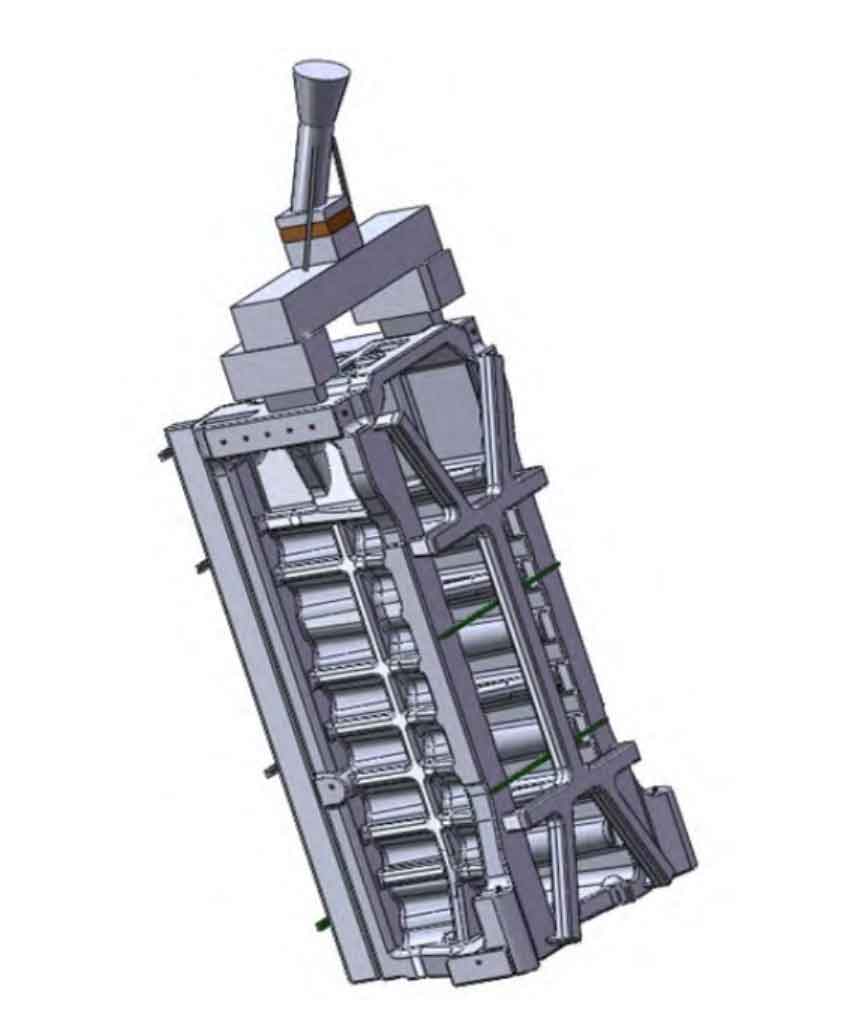
The lost foam casting process is as shown in the figure. The top-pouring inclined pouring process is adopted. Clean iron nails are inserted into the parts of nodular iron castings with large hot spots as internal cooling iron to improve the density of the structure in this part. Due to the largest size of hot spot at the top of ductile iron castings, the method of increasing the cross section area of the cross runner is adopted in the process, and the cross runner is used to replace the riser, which plays a role of feeding. The cross section size of the runner is set to 80 mm × 70 mm, the section size of the runner is 100 mm × 25 mm。 In order to reduce inclusions in molten iron, 75 mm is adopted below the sprue × 75 mm × 22 mm (10ppi) foam filter screen is used to filter molten iron to improve the purity of molten iron.
Element | C | Si | Mn | S | P | Mg | Sn |
Content | 3.70~3.80 | 2.75~2.95 | 0.4~0.45 | ≤0.025 | ≤0.03 | 0.04~0.06 | 0.018~0.022 |
The key links in the commissioning stage are controlled as follows:
(1) The pouring system used for mold assembly adopts resistance wire cutting. In order to prevent the deformation of nodular iron castings, fiber rods and molded foam anti deformation lacing bars are added on the open surface of the oil pan during mold assembly.
(2) When the coating is dipped, the Baume degree is controlled at 65 ° B é, the coating is dipped four times, the drying temperature of the yellow mold is 40~55 ℃, and the drying time is more than 12 hours. After the yellow mold is dried, the inner runner shall be coated to prevent the coating from breaking during the pouring process.
(3) In order to reduce the shrinkage tendency of ductile iron castings, the pouring temperature should not be too high, and the pouring temperature of molten iron should be set at 1450-1470 ℃; In order to reduce spheroidization deterioration and cause unqualified material quality, the process requires that molten iron be poured within 10 min after spheroidization; In order to reduce the deformation of ductile iron castings, the vacuum negative pressure is set to -0.05~-0.065 MPa, and the pressure holding time of the sand box after pouring should be greater than 20 minutes.
(4) The smelting process is controlled. The charge ratio is pig iron: scrap: return charge=2:2:4. The chemical composition of molten iron is controlled as shown in the table.