Sand casting is a versatile and cost-effective method of producing complex metal parts. However, one common issue that manufacturers often grapple with is porosity. This phenomenon, characterized by small voids or pores within the castings, can have significant implications for the quality and functionality of the final product. This article delves into the causes, consequences, and remedies of porosity in sand casting.
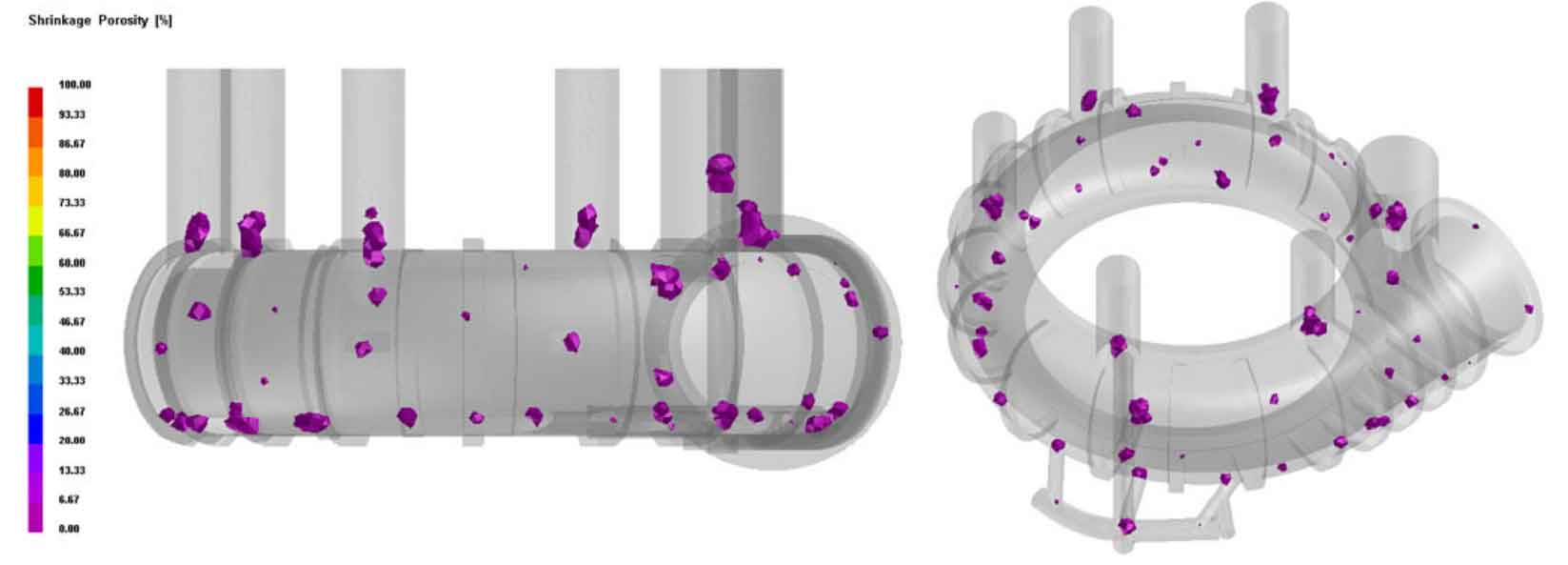
1.Causes of Porosity:
Porosity in sand castings can primarily be attributed to the following factors:
- Gas Entrapment: During the pouring process, gases can become trapped within the molten metal, forming bubbles that evolve into pores as the metal solidifies.
- Shrinkage: The contraction of metal as it cools can lead to voids in the casting, particularly if the shrinkage is not adequately compensated.
- Improper Venting: The sand mold must be suitably vented to allow gases generated during the casting process to escape. Inadequate venting can result in trapped gases and subsequent porosity.
2.Consequences of Porosity:
The presence of porosity can drastically impact the quality of sand castings, manifesting in the following ways:
- Reduced Strength: Porosity undermines the mechanical strength of the casting, making it susceptible to failure under load.
- Lower Fatigue Resistance: The voids in the metal can serve as initiation sites for cracks, reducing the fatigue life of the casting.
- Aesthetic Defects: Surface pores can cause cosmetic imperfections, detracting from the appearance of the casting.
3.Remedies for Porosity:
There are several strategies to mitigate porosity in sand casting:
- Proper Mold Design: An effective gating and venting system can facilitate a smooth, uninterrupted flow of molten metal, minimizing the risk of gas entrapment.
- Controlled Pouring: By carefully managing the temperature and rate of pouring, it is possible to reduce turbulence, minimizing gas entrapment.
- Use of Risers: Risers supply extra molten metal to compensate for shrinkage during solidification, thereby reducing the risk of shrinkage-related porosity.
- Gas Control: Employing methods to reduce the gas content in the molten metal and ensuring optimal moisture content in the molding sand can further mitigate gas-related porosity.
While porosity is a common challenge in sand casting, understanding its causes and implications can guide effective strategies to combat it. By implementing proper mold design, controlled pouring techniques, the use of risers, and gas control measures, manufacturers can significantly reduce the occurrence of porosity, thereby enhancing the quality and performance of their sand castings.