1. White mold making
Due to the large size of the vacuum pump shell casting, the white mold of the vacuum pump shell casting cannot be made completely at one time, and the white mold can only be made by splicing. First, the vacuum pump shell casting is divided into several pieces with CAD software (as shown in Figure 1), and then cut with a full-automatic NC cutting platform. Among them, the vacuum pump shell cylinder is divided into 12 pieces, and the flanges at both ends of the vacuum pump shell are divided into 8 pieces. The round corner size of the cylinder is R10 mm, which is bonded with fine foam strips.
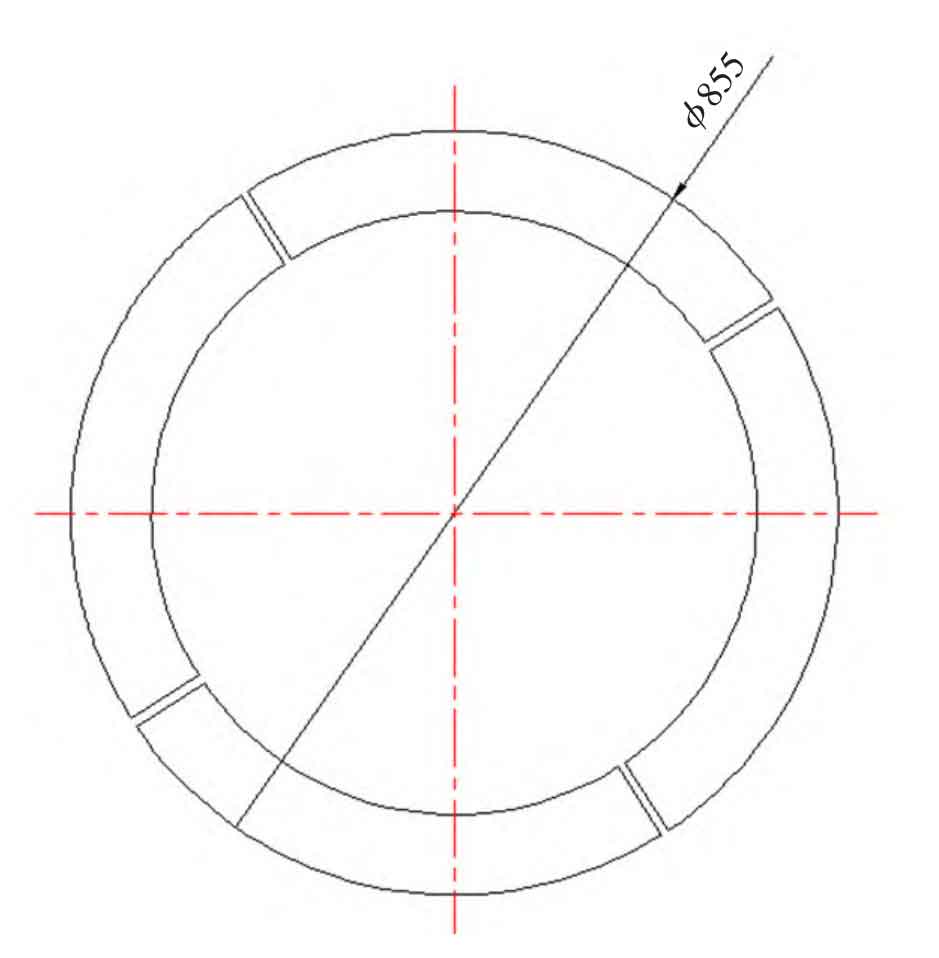
2. White module mold
The cut foam blocks are spliced manually. First, the center of the circle is aligned on the glass plate, then the cut foam blocks are aligned, and the foam is bonded with fiber rods to fix the position; Then glue and wrap paper tape on the gap of the white mold to eliminate the gap of the white mold and prevent the paint from entering the gap when the white mold is dipped. In order to prevent the white mold of the vacuum pump housing from deformation during coating dipping, two pieces of white mold with a cross-sectional size of 15 mm are bonded at the upper and lower ends of the white mold × 15 mm wooden strips for reinforcement. In order to prevent the vacuum pump shell castings from shrinkage cavity or porosity, the gating system is used to feed the vacuum pump shell castings. Finally, the fiber bar is used to bond and reinforce the white mold riser to prevent the white mold from being damaged in the production process. Figure 2 shows the white module mode.
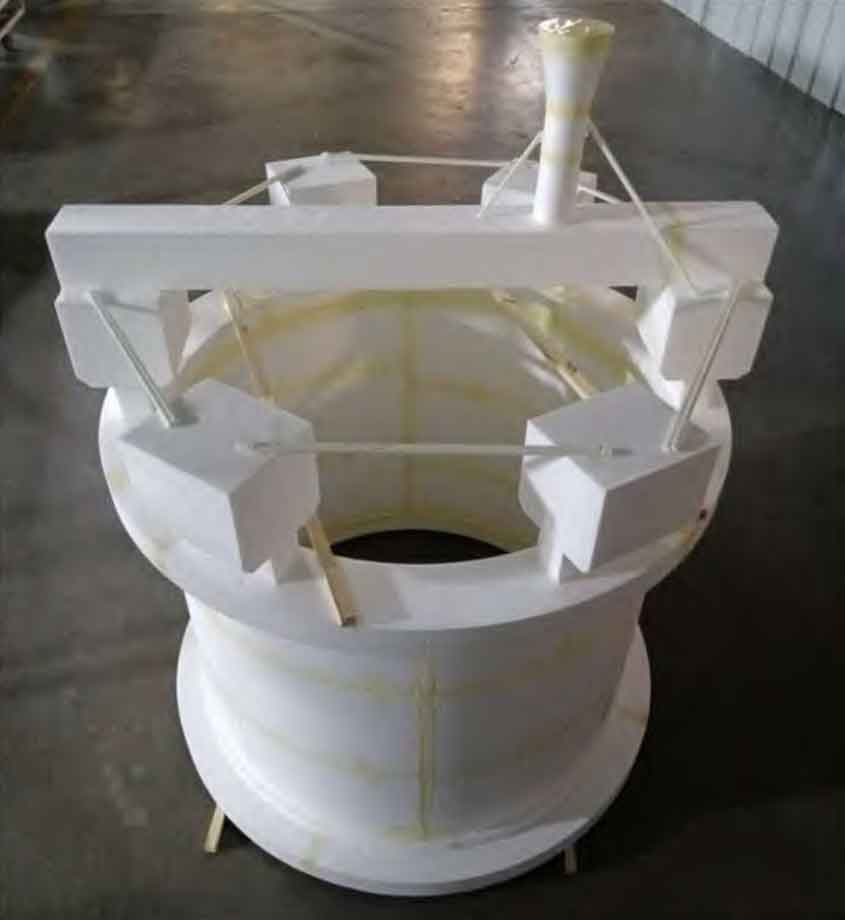
3. Coating dip coating
Due to the enlarged shape of the vacuum pump shell after mold assembly, it is required to dip the paint to every position of the white mold during the dip coating of the white mold. First, the operator slowly rotates the white mold when dipping the white mold in the paint pool, and then uses a small container to pour the paint to the place where the white mold is not easy to dip. After the coating is dipped, the Yellow mold is placed on the special drying rack car and pushed into the drying room for dehumidification and drying. In order to ensure that the molten iron will not be damaged during pouring, the coating is required to be dipped for 4 times, and the Baume degree of the coating is controlled at 69~71 ° B é. The Yellow mold status is shown in Figure 3.
4. Packing and pouring
First, scrape the bottom sand, and then two people work together to put the Yellow mold into a sand box (as shown in Figure 4), manually add sand flexibly to fill the sand box, and the three-dimensional vibration time of the sand box is controlled at 90 s.
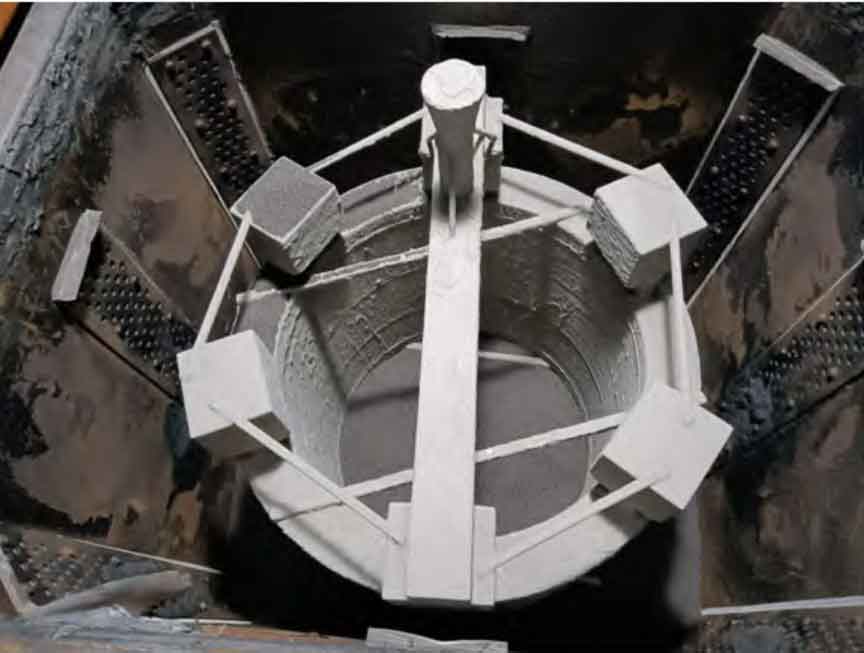