Lost foam casting indeed has the potential to redefine precision engineering in metal fabrication. This advanced technique allows for the production of metal parts with intricate designs and high accuracy, offering several advantages over traditional casting methods. Here’s how lost foam casting is changing the game:
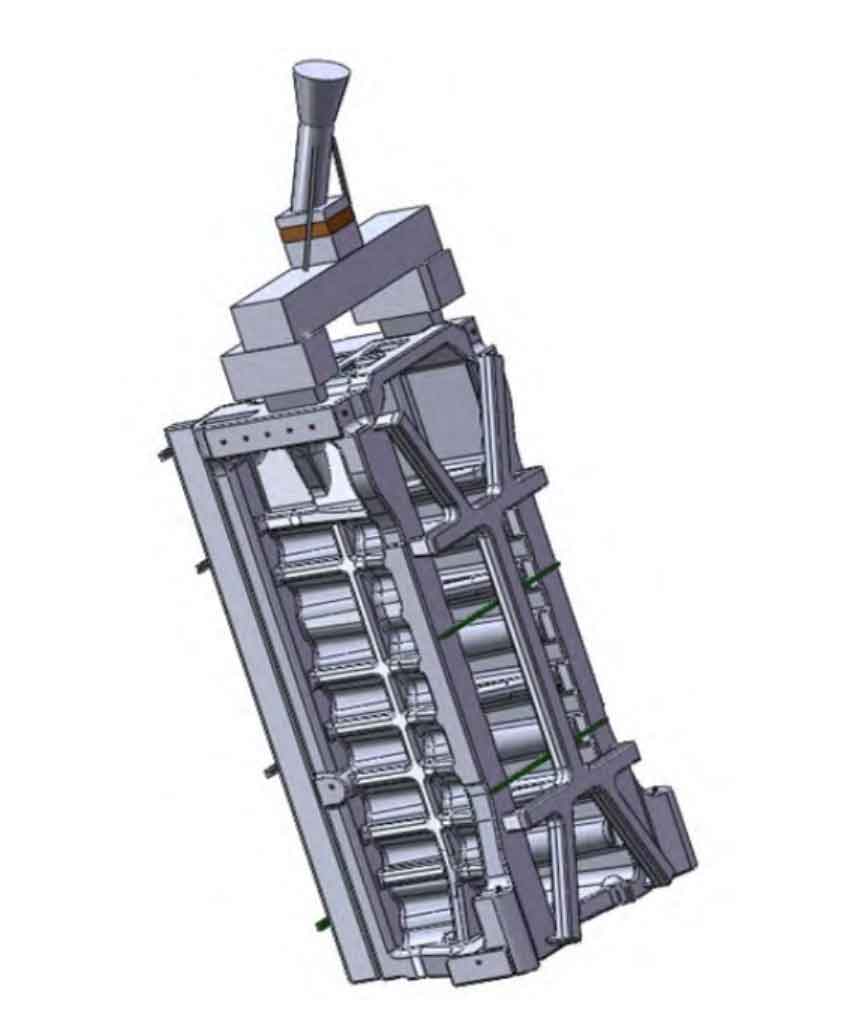
1. Enhanced Precision and Complexity: One of the primary advantages of lost foam casting is the ability to manufacture parts with complex geometries and internal structures that are challenging or impossible to create with conventional casting techniques. This capability extends the boundaries of precision engineering, enabling the production of components with enhanced features and functionality.
2. Superior Surface Finish: The use of advanced foam patterns and improved coating materials results in a superior surface finish compared to traditional casting methods. This minimizes the need for additional finishing operations, saving time and reducing costs.
3. Reduced Material Wastage: The near-net-shape production capability of lost foam casting means there is less need for machining and finishing operations, leading to reduced material wastage. This is not only cost-effective but also aligns with sustainability efforts to minimize resource use and waste.
4. Improved Quality Control: The use of simulation software in the lost foam casting process allows for the detection and correction of potential casting defects before they occur. This proactive approach to quality control leads to improved product quality, lower scrap rates, and increased efficiency.
5. Greater Design Flexibility: The ability to cast complex shapes with high precision gives designers greater flexibility when creating new products. They can experiment with innovative designs, confident that the lost foam casting process can accurately realize their concepts.
6. Potential for Automation: lost foam casting lends itself well to automation, with opportunities for automated foam pattern production, mold assembly, and casting removal. This can lead to increased productivity, reduced labor costs, and improved consistency and quality.
These features make lost foam casting a powerful tool in precision engineering, allowing for the creation of metal components that are more complex, more accurate, and of higher quality than those produced using traditional casting methods. With continued research and development, we can expect to see even greater advancements in this field, pushing the boundaries of precision engineering further and opening up new possibilities in metal fabrication.