The “white zone” technology and equipment of China’s lost foam casting is the weakest link, mainly including the following:
Development of plastic beads foreign professional chemical companies research and develop expandable polystyrene, PMMA beads and their copolymer products for lost foam casting. They have their own advantages for users to choose from. At present, the expandable polystyrene beads used in the packaging industry are mostly used in China. This kind of raw material can be used for general castings, but it is not suitable for manufacturing thin-walled and complex foamed plastic patterns. Therefore, the foundry needs to work closely with the chemical plant to speed up the development of plastic beads with low density, stable size and no deformation, or new materials with better performance.
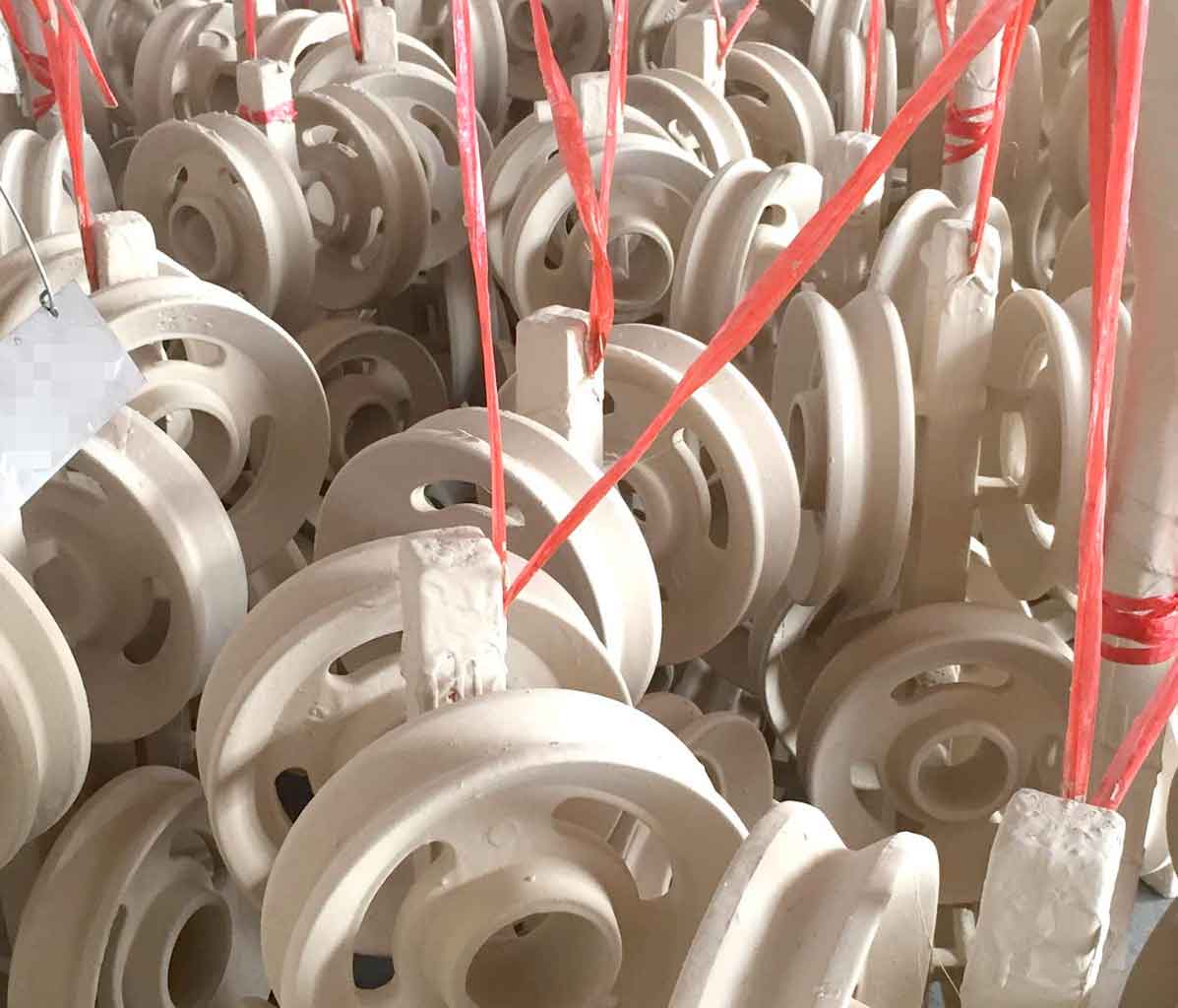
Tooling and mold cad\cam: the mold for foaming molding and die bonding is the most critical process equipment in the molding process. Cad/cam should be used to complete the mold of complex castings such as cylinder head and cylinder block. It is not enough to rely solely on the efforts of casting engineers. It is necessary to organize casting experts, mechanical designers, engineers in parts processing and NC processing technology experts, divide work and cooperate to jointly tackle key problems, and create an advanced and practical mold cad/cam system.
To improve the molding technology, we need to carry out a lot of experiments and production practice, master the size change law between foam mold and foam plastic pattern castings, and accumulate reliable data for new mold design.
Localization of molding machine and bonding machine develop high-precision and efficient molding machine and bonding machine, and realize the localization and serialization of molding machine and bonding machine.
With the establishment of strict quality control system and the improvement of key process monitoring instruments, the quality of lost foam castings will be further improved and the scrap rate will be greatly reduced. The latest progress of industrialized countries has shown a bright future in this regard. For example, a lost foam casting workshop in the United States has achieved the stable use of high-quality coatings due to the strict monitoring of the permeability of the coating, the adsorption of liquid pyrolysis products and the thermal insulation ability, and the weekly scrap rate has decreased from 5.5% to 0.25%; Due to the use of a new shaking table in a lost foam casting production line, the deformation scrap rate decreased from 17% to 1%; Due to the use of CMM with multiple sensors, the measurement accuracy of the model can be controlled within ± 0.0125mm. In the field of mold and manufacturing, rapid manufacturing technology and computer simulation in parallel environment will be widely used, so as to greatly shorten the production time of mold and realize the rapid production of castings. The so-called rapid manufacturing technology refers to the combination of prototype provided by rapid prototype manufacturing technology and precision casting technology to produce accurate mold castings at an extraordinary speed. A new method of computer simulation in parallel environment, that is, while designing products and performing performance analysis
Through step graphic information transmission and exchange, casting process CAD, casting forming process simulation (CAE) and casting tooling cad/cam can be carried out at the same time. When the product design is completed, the production preparation of castings is also completed at the same time, which greatly shortens the time for castings to be put on the market. With the improvement of tail gas purification device and old sand treatment equipment, as well as the improvement of automation between processes, a highly civilized green lost foam casting plant will appear. Lost foam casting will be combined with other new casting processes to create new composite process methods to further improve the quality and production efficiency of castings. For example, lost foam casting will be combined with low-pressure casting to achieve strict control of metal liquid filling speed, orderly gasification of lost foam patterns, and crystallization and solidification of castings under certain pressure, so as to obtain aluminum alloy castings with dense structure and high air tightness. In the 21st century, lost foam casting will become a considerable new field in the foundry industry and be widely used all over the world.