Foamed plastic plays a very important role in lost foam casting, and its quality will directly affect the quality of castings. The model material should meet the requirements of high strength, low density, full combustion, less decomposition products, long storage life and so on. Materials suitable for making models include polystyrene, polymethylmethacrylate, polycarbonate, polyethylene, polypropylene, polyvinyl chloride, etc.
Polystyrene is an aromatic hydrocarbon containing 92% carbon and hydrogen. Its molecular structure can be expressed as (C8H8). It is a thermoplastic resin developed by Dow chemicals in. Dow chemicals uses rapid decomposition technology to study the decomposition mechanism of polymers. Through the observation of the decomposition products of foam plastics in lost foam casting, it is clear that the decomposition mechanism of foam plastics has a great impact on the formation and quantity of carbon residue.
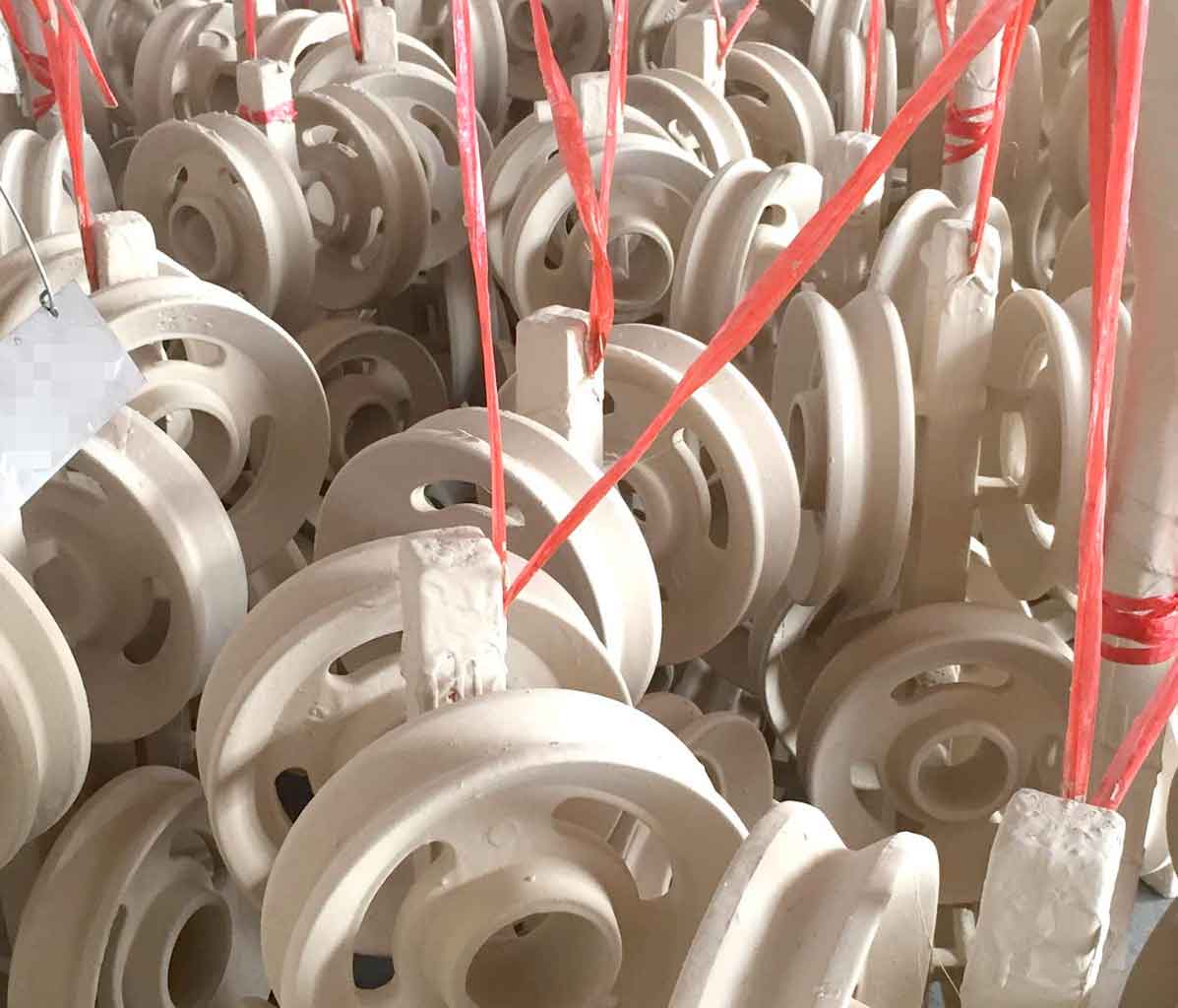
The research shows that the decomposition of foamed plastics is carried out by three mechanisms, namely, arbitrary fracture mechanism (staggered separation), binding separation and symmetrical separation. The staggered separation of foamed plastics has the advantage of low gas generation, but it has the tendency to decompose into highly viscous liquid residue nonvolatile carbon. Foam polystyrene is a staggered separation mechanism. The monomer does not contain oxygen atoms, and the carbon is enriched on the benzene ring. The benzene ring has high stability and is difficult to be thermally decomposed. A large amount of black smoke is emitted during pouring, which is easy to produce carbon deposition and bright carbon defects on the surface of iron castings, and the carbon increase on the surface of low carbon steel castings is up to 0.1-0.3%. In 1986, a new material developed by Dow chemicals of the United States, polymethylmethacrylate, is a non polymer structure with a combination separation mechanism. The molecular weight of the decomposition product of this mechanism is low, so the gas evolution is large, 40-50% higher than that of polystyrene foam. In PMMA, each monomer contains five carbon atoms and two oxygen atoms. Under the action of high-temperature metal liquid, the oxygen atoms of the polymer can combine with carbon to form Co, which takes carbon away from the cavity. In this way, one oxygen atom takes away one carbon atom, which reduces the carbon residue of PMMA. At the same time, PMMA does not have aromatic structure, which greatly reduces the chance of forming nonvolatile residue. In addition, PMMA has the property of shielding, so it is easy to preserve. It can be preserved for several months from pre foaming to molding. The temperature at which PMMA becomes glassy is 5 ℃ higher than EPS, so a higher temperature is required during pre foaming. The typical shrinkage of PMMA is 0.994-0.997%, and the size is stable after drying. Dow chemicals applied PMMA to cast iron, successfully eliminated carbon black defects, and applied it to alloy steel, significantly reducing carburization, which was only less than 0.05%.