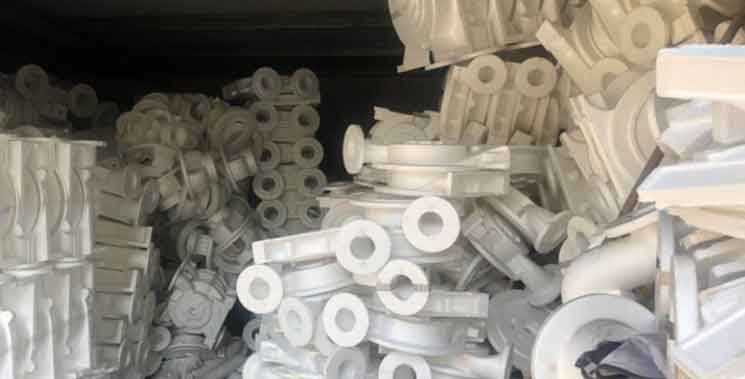
Lost foam casting, also known as evaporative pattern casting or full mold casting, is a modern and innovative casting process that allows for the production of complex and intricate metal components. This casting method involves using expanded polystyrene (EPS) foam patterns that are coated with a refractory material to create a mold. When the molten metal is poured into the mold, the foam pattern evaporates due to the high temperature, leaving behind a cavity that replicates the desired shape of the final component. Here are some key features and advantages of the lost foam casting process:
- Complex Geometry: Lost foam casting is particularly well-suited for creating parts with intricate shapes and complex geometry, including thin-walled structures and internal cavities that are challenging to achieve with traditional casting methods.
- Reduced Tooling Costs: Since lost foam casting does not require expensive molds, patterns, or cores, it can significantly reduce tooling costs compared to other casting techniques. This makes it more cost-effective for small-scale production or one-off prototypes.
- High Dimensional Accuracy: The foam patterns used in lost foam casting are typically produced using computer-aided design (CAD) models, which ensures high dimensional accuracy and precise replication of the desired component shape.
- Minimal Draft Angles: Unlike other casting methods that require draft angles for easy pattern removal, lost foam casting allows for near-net shape manufacturing with minimal draft angles, reducing the need for secondary machining.
- Smooth Surface Finish: Lost foam casting can produce components with a smooth surface finish, reducing the need for additional finishing processes.
- Reduced Core Shift: Since the foam pattern is consumed during the casting process, there is no risk of core shift, which can occur in traditional sand casting, leading to improved dimensional stability.
- Lower Environmental Impact: Lost foam casting produces less waste material compared to other casting techniques, making it more environmentally friendly.
- Design Flexibility: The design flexibility offered by lost foam casting allows for the integration of multiple features and functions into a single component, reducing the need for assembly and welding.
- Shorter Lead Times: The simplicity of the lost foam casting process allows for shorter lead times from design to finished product, making it attractive for time-sensitive projects.
Despite its advantages, lost foam casting also has some limitations, such as limitations on the size and weight of the castings and the need for careful control of the casting process parameters to avoid defects. However, advancements in technology and process optimization have enabled lost foam casting to become an increasingly popular choice for producing high-quality, intricate metal components for a wide range of industries, including automotive, aerospace, marine, and more.