Spheroidal Graphite Cast Iron (SGCI), also known as ductile iron, plays a significant role in automotive engineering. Its unique combination of strength, ductility, and cost-effectiveness makes it a preferred material for various components. Let’s explore the current trends and future prospects of Spheroidal Graphite Cast Iron in automotive engineering.
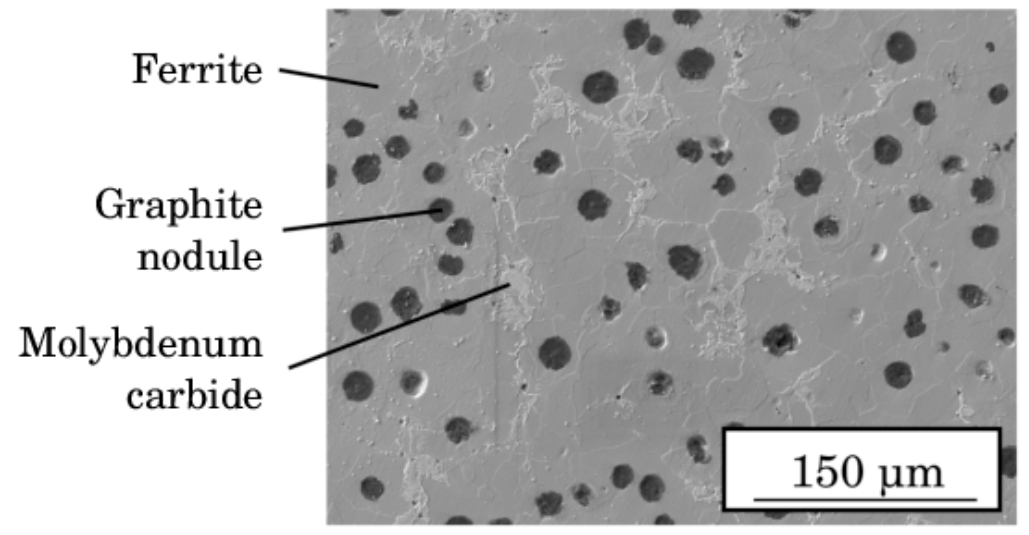
Current Trends in Automotive Engineering
- Lightweighting: While traditionally used for its strength, there’s a growing trend in using Spheroidal Graphite Cast Iron in applications where reducing vehicle weight is crucial. This involves designing thinner, yet strong components and sometimes blending Spheroidal Graphite Cast Iron with other lightweight materials.
- High-Stress Components: Spheroidal Graphite Cast Iron is widely used in manufacturing high-stress parts such as engine blocks, crankshafts, gearboxes, and drive shafts. Its high fatigue strength makes it ideal for these applications.
- Brake Systems: The excellent thermal conductivity and high heat capacity of Spheroidal Graphite Cast Iron make it suitable for brake rotors and drums, providing durability and consistent performance.
- Suspension Systems: For components like knuckles, control arms, and strut forks, Spheroidal Graphite Cast Iron offers the necessary strength and toughness, particularly in rough driving conditions.
- Noise, Vibration, and Harshness (NVH) Control: The damping properties of Spheroidal Graphite Cast Iron help in reducing NVH levels in vehicles, an important factor in improving ride quality.
Innovations and Advanced Applications
- Austempered Ductile Iron (ADI): This form of heat-treated Spheroidal Graphite Cast Iron offers superior strength and wear resistance. ADI is becoming more popular in automotive applications for parts that require high strength-to-weight ratios.
- Complex Castings: Advanced casting techniques allow for more complex Spheroidal Graphite Cast Iron components, reducing the need for additional machining and assembly, thereby cutting costs.
- Integration with Electric Vehicles (EVs): As the automotive industry shifts towards EVs, Spheroidal Graphite Cast Iron is used in battery frames and other structural components due to its protective strength and affordability.
Future Prospects
- Hybrid Material Components: There’s potential in developing composite materials that combine Spheroidal Graphite Cast Iron with lighter materials like aluminum or carbon fiber, offering strength without significantly increasing weight.
- Additive Manufacturing: Exploring 3D printing of Spheroidal Graphite Cast Iron could revolutionize how parts are designed and manufactured, allowing for more complex geometries and optimized designs.
- Sustainability Focus: As the automotive industry focuses more on sustainability, recycling and reducing the environmental impact of Spheroidal Graphite Cast Iron production will become increasingly important.
- Enhanced Alloy Development: Ongoing research into alloying Spheroidal Graphite Cast Iron with various elements aims to improve its properties, such as increased strength, corrosion resistance, and better performance under high temperatures.
- Application in Autonomous Vehicles: As autonomous vehicle technology advances, the demand for robust and reliable components that can withstand various environmental and operational stresses will likely increase the use of Spheroidal Graphite Cast Iron.
Spheroidal Graphite Cast Iron remains a key material in automotive engineering, offering an unbeatable combination of mechanical properties and cost-effectiveness. Its evolving applications, driven by industry trends towards lightweighting, electrification, and sustainability, are likely to expand, ensuring its continued relevance in the future of automotive design and manufacturing.