This article provides a comprehensive introduction to low-pressure casting, including its basic principles, process characteristics, relevant process parameters, and common defect analysis. By detailing these aspects, it aims to help readers gain a deep understanding of this important casting method. The content is based on the relevant literature and research results, aiming to present a clear and detailed picture of low-pressure casting.
1. Introduction
Low-pressure casting is one of the important casting methods used for the production of non-ferrous metal castings, especially in achieving precision, thin-walled, and lightweight molding and manufacturing. Compared to gravity casting, low-pressure casting offers several advantages such as good casting formability, a small number of defects, and a high process yield. This article focuses on analyzing the technical principles, process characteristics, the influence of related process parameters on casting quality, discusses the causes and prevention measures of low-pressure casting defects, and looks forward to the development trend of low-pressure casting.
2. Basic Principles of Low-Pressure Casting
Low-pressure casting is a casting process in which the molten metal fills the mold cavity under a certain pressure to form a casting. The pressure used is relatively low, usually ranging from 0.02 MPa to 0.06 MPa. The basic process is as follows: In a sealed crucible (or sealed tank), dry compressed air or inert gas is introduced. Under the action of gas pressure, the molten metal rises steadily along the riser tube and enters the cavity through the inner gate. The gas pressure on the liquid surface in the crucible (or sealed tank) is maintained until the casting is completely solidified. Then, the gas pressure on the molten metal surface is released, causing the un-solidified molten metal in the riser tube to flow back into the crucible, and finally, the casting is pushed out. The schematic diagram of low-pressure casting is shown in Figure 1.
3. Process Parameters of Low-Pressure Casting
3.1. Liquid Lifting Pressure
The pressure required to raise the liquid metal surface to the vicinity of the gate is called the liquid lifting pressure. It reflects the rising speed of the molten metal in the riser tube. The rising speed of the molten metal in the riser tube should be as slow as possible to facilitate the exhaust of gas in the cavity and prevent splashing of the molten metal when it enters the gate.
3.2. Filling Pressure
This is the gas pressure required for the molten metal to rise to the top of the mold during the filling process.
3.3. Filling Speed
The rising speed of the metal liquid surface during the filling process is the filling speed. To prevent the occurrence of cold shut and underfilling defects, the filling speed should be higher than the minimum value, but not too fast to avoid the generation of oxide inclusions caused by turbulent molten metal.
3.4. Crystallization Pressure
After the molten metal fills the cavity, the pressure is further increased to allow the crystallization and solidification of the casting to proceed under a certain pressure, which is called the crystallization pressure. A higher crystallization pressure leads to better feeding effect, denser microstructure of the casting, and improved mechanical properties. However, increasing the pressure through crystallization to improve the casting quality is not applicable in all cases. The typical value range of crystallization pressure is usually from 0.1 MPa to 0.25 MPa.
3.5. Holding Time
After the pressure of the molten metal increases to the crystallization pressure, it needs to be maintained for a period of time until the casting is completely solidified, and the time required for pressure holding and solidification is called the holding time. If the holding time is insufficient, the molten metal in the cavity may flow back into the crucible before the casting is completely solidified, resulting in a “void” waste of the casting. If the holding time is too long, the gate residue will be too long, which not only reduces the process yield but also makes it difficult for the casting to be removed from the mold due to the “freezing” of the molten metal in the gate and riser tube. Therefore, an appropriate holding time must be selected in the production process.
3.6. Mold Temperature
Low-pressure casting can use various molds. The working temperature of non-metallic molds is generally room temperature. However, there are certain requirements for the working temperature of metallic molds. For example, when low-pressure casting aluminum alloys, the working temperature of the metallic mold is generally controlled at 200 °C to 250 °C, and even up to 300 °C to 350 °C when casting thin-walled and complex parts.
3.7. Pouring Temperature
Practical evidence shows that, on the premise of ensuring the molding of the casting, the lower the pouring temperature, the better. The pouring temperature of low-pressure casting is generally 10 °C to 20 °C lower than that of gravity casting.
4. Process Characteristics of Low-Pressure Casting
4.1. Advantages of Low-Pressure Casting
4.1.1. Avoidance of slag inclusion
Since the slag usually floats on the surface of the molten metal, and the low-pressure casting process fills the mold cavity with the molten metal from the bottom of the crucible through the riser tube, the possibility of slag entering the cavity can be effectively avoided, resulting in a high purity of the molten metal and a small number of inclusions in the casting.
4.1.2. Stable filling
The low-pressure casting process adopts a bottom-filling technique with balanced pressure, ensuring a relatively stable filling of the molten metal, effectively reducing or avoiding turbulence, splashing of the molten metal during the filling process, and minimizing the possibility of defects such as double oxide films and oxide inclusions in the casting.
4.1.3. Good formability
With the filling of the molten metal under pressure, the fluidity of the molten metal can be enhanced to a certain extent, which is conducive to the formation of castings with a good surface finish and clear contours, particularly beneficial for the formability of complex thin-walled castings.
4.1.4. Sequential solidification
The casting solidifies under a certain pressure and can achieve sequential solidification from top to bottom (as shown in Figure 3). This provides a good feeding effect, resulting in a denser microstructure of the casting with fewer shrinkage porosity and shrinkage cavity defects.
4.1.5. High metal yield
Generally, no riser is required in low-pressure casting, and the un-solidified molten metal in the riser tube can be refluxed to the crucible for reuse, thereby achieving a high metal yield, usually above 90%.
4.2. Disadvantages of Low-Pressure Casting
4.2.1. High equipment cost
The equipment cost of low-pressure casting is relatively high, requiring a large initial investment.
4.2.2. Low production efficiency
The production efficiency is relatively low, and it is generally used for casting non-ferrous alloys.
4.2.3. Corrosion of crucible and riser tube
When producing aluminum alloy castings, the crucible and riser tube are in long-term contact with the molten metal, prone to erosion and 报废,which may also cause an increase in iron content in the molten metal, leading to deterioration of the casting performance.
5. Common Defects in Low-Pressure Casting and Countermeasures
5.1. Porosity
5.1.1. Morphological characteristics
The porosity usually appears as round or oval shapes with smooth inner walls and often with a slight oxidized color.
5.1.2. Causes of generation
- Excessive filling speed of the molten metal leads to turbulent flow, entraining gas that fails to be discharged smoothly in a timely manner, resulting in the generation of porosity defects.
- After the filling of the molten metal is completed, due to the long-term heating and outgassing of the sand mold and core, the gas invades the not-yet-solidified molten metal, further causing the generation of porosity defects.
- Poor exhaust conditions in the mold cavity, with trapped gas areas existing, leading to the occurrence of porosity defects.
5.1.3. Prevention measures
- Select an appropriate filling speed to ensure the stability of the molten metal filling while avoiding the occurrence of porosity defects, without causing cold shut and underfilling.
- Optimize the exhaust conditions of the sand mold and core to prevent the gas generated by the sand mold and core from entering the molten metal. Additionally, under the premise of ensuring the strength of the sand mold and core, reduce the resin content of the sand mold and core to reduce the gas generation amount.
- Avoid clogging of the exhaust holes and plugs, and other exhaust structures.
5.2. Shrinkage porosity and shrinkage cavity
5.2.1. Morphological characteristics
The morphology of shrinkage porosity and shrinkage cavity is often irregular holes with relatively rough inner walls and many dendritic protrusions, mostly occurring in the hot spot center or the last solidification area.
5.2.2. Causes of generation
After the filling of the molten metal is completed, during the crystallization and solidification process, a temperature gradient from top to bottom fails to be formed, preventing sequential solidification, and thus, a good feeding cannot be achieved in the final solidification hot spot area, resulting in the generation of shrinkage cavity defects.
5.2.3. Prevention measures
- Enhance the heat dissipation capacity of the hot spot area (such as by arranging cold irons).
- Try to reduce the pouring temperature as much as possible without causing cold shut.
- Increase the holding pressure during crystallization and solidification to improve the fluidity of the molten metal and enhance the feeding ability of the shrinkage cavity area.
5.3. Cold shut
5.3.1. Morphological characteristics
The morphological feature of a cold shut is the presence of a cold shut line, where the front ends of the two convective molten metal streams fail to achieve good fusion.
5.3.2. Causes of generation
- Low pouring temperature or strong cooling capacity of the mold, which is prone to causing the generation of cold shut defects at the molten metal flow area.
- Insufficient filling pressure, resulting in poor fluidity of the molten metal, also contributing to the occurrence of cold shut defects.
5.3.3. Prevention measures
- Appropriately increase the pouring temperature of the molten metal.
- For the cold shut lines caused by the excessive cooling speed of the cold iron rod, a moderate heating treatment can be performed on the cold iron rod.
- Appropriately increase the filling pressure of the molten metal to improve the fluidity of the molten metal.
5.4. Inclusions
5.4.1. Morphological characteristics
The morphology of inclusion defects is an irregular shape, and the color at the defect location has a significant difference from that of the casting body.
5.4.2. Causes of generation
- For the formation of non-metallic inclusions, it mostly originates from foreign objects that fall into the cavity during the mold cleaning process and then enter the molten metal during the filling process, forming inclusion defects.
- Oxide inclusions are mainly caused by the rapid filling speed of the molten metal, resulting in a turbulent liquid surface and splashing, forming a double oxide film that leads to the generation of inclusion defects.
5.4.3. Prevention measures
- During the mold cleaning process, ensure that the processing cavity is thoroughly cleaned.
- Adjust the filling pressure to avoid excessive filling speed causing turbulent splashing of the molten metal or add a filter screen at the liquid lifting port to play a role in filtering and stabilizing the molten metal.
6. Development History of Low-Pressure Casting
The low-pressure casting process has a history of more than 100 years. It was first proposed by British scientist E.F. Lake, but at the beginning of its proposal, this casting process did not form large-scale industrial application and production. It was not until 1945 that the British Armsco Company used the low-pressure casting process for large-scale and industrial production of products such as rainwater pipes and beer containers. After 1950, due to the rapid development of the automotive industry, the United States applied the low-pressure casting process to the manufacturing of automotive engine parts, which brought about a qualitative leap in the low-pressure casting process and related equipment. Around 1957, China officially introduced low-pressure casting equipment and conducted research on related casting processes.
7. Equipment of Low-Pressure Casting
7.1. Host
Generally consists of a mold closing mechanism, a static mold core-pulling mechanism, a frame, a casting ejection mechanism, a part taking mechanism, and a safety limit mechanism.
7.2. Insulation Furnace
Mainly includes crucible insulation furnaces and molten pool insulation furnaces. Crucible insulation furnaces have two types: graphite crucible and cast iron crucible. Molten pool insulation furnaces adopt an overall knotting process of the furnace refractory material, with silicon carbide rods for radiant heating and insulation. They have the characteristics of large capacity, long service life, and simple maintenance, which is very conducive to continuous production requirements and is widely used in modern low-pressure casting machines.
7.3. Riser Tube
It is a channel for diversion and feeding, and it is hermetically connected to the crucible cover in a detachable manner to form a sealed container that can withstand pressure. Under the action of process air pressure, the molten metal conducts filling and pressure-increasing crystallization and solidification through the riser tube; when the pressure is released, the un-solidified alloy liquid flows back to the crucible through the riser tube. Therefore, the correct design and use of the low-pressure casting riser tube are very important.
7.4. Liquid Surface Pressurization Device and Its Pressurization Specifications
In low-pressure casting, the correct control of the filling and pressurization of the mold is the key to obtaining good castings. This control is completely realized by the liquid surface pressurization control system. According to the requirements of different castings, the liquid surface pressurization system should be adjustable within the range of process parameters, with stable and reliable operation and a structure that is convenient for maintenance.
8. Application of Low-Pressure Casting
Low-pressure casting was one of the earliest anti-gravity casting technologies and began to be used in industrial production in the 1940s. Nowadays, low-pressure casting is mainly used in the production of aluminum alloy and magnesium alloy parts, such as automotive wheel hubs, cylinder blocks, cylinder heads, pistons, missile shells, impellers, guide vanes, etc. of internal combustion engines. When using low-pressure casting to produce cast steel, such as cast steel wheels, special refractory materials need to be used for the riser tube. Low-pressure casting can also be applied to small copper alloy castings, such as pipe fittings and bathroom faucet taps, and this technology has been industrialized in foreign countries.
9. Comparison with Other Casting Methods
9.1. Gravity Casting
In gravity casting, the molten metal is filled into the mold cavity by its own gravity. This method is simple but has limitations. It is difficult to ensure high strength for castings, especially for magnesium alloys with a low density. A large amount of molten metal is required during the pouring process, resulting in a waste of materials and a relatively high process cost.
9.2. Pressure Casting
Also known as die casting, it first injects the molten metal into the injection cylinder, and then applies a high pressure (generally 30 to 70 MPa) through a plunger to make it fill and solidify in the mold cavity. Although this method can improve production efficiency, it may cause problems such as gas entrapment and the inability to perform heat treatment strengthening on the castings due to the high-pressure filling process. To address these issues, vacuum die casting and oxygen-charged die casting techniques have been developed. However, these methods require additional equipment and increase the complexity and cost of the process.
9.3. Centrifugal Casting
The molten metal is filled into the rotating mold cavity, and then solidified under the action of centrifugal force. This method can improve the process yield, reduce the consumption of the gating system and riser system, and improve the density and mechanical properties of the castings. However, it has certain limitations in the production of 异形 castings, and the inner hole diameter and surface roughness of the castings may not be very accurate.
9.4. Metal Mold Casting
The molten metal is filled into the metal mold under the action of gravity, and then solidified in the mold. This method has the advantages of a high cooling speed, dense microstructure of the castings, and good dimensional accuracy. However, the mold itself has no gas permeability, and measures need to be taken to 导出 the air and gas generated by the sand core in the cavity. Additionally, the mold has no deformability, and cracks may easily occur during the solidification of the castings.
9.5. Vacuum Die Casting
By evacuating the gas in the mold cavity during the die casting process, the generation of pores and dissolved gas in the castings can be eliminated or significantly reduced, thereby improving the mechanical properties and surface quality of the castings. However, the sealing structure of the mold is complex, the manufacturing and installation are more difficult, and the effect may not be very significant if not controlled properly.
9.6. Squeeze Casting
Both direct and indirect squeeze casting are carried out by injecting the molten metal into the mold cavity at a relatively low flow rate, and then solidifying it under high pressure. This method can eliminate internal pores, shrinkage porosity, and shrinkage cavity defects, improve the surface roughness and dimensional accuracy of the castings, and prevent the occurrence of casting cracks. It is suitable for the production of various alloys, but the process is relatively complex.
9.7. Lost Foam Casting
It is a new casting method that combines the lost foam casting process with low-pressure casting. By bonding and combining wax or foam models similar in size and shape to the casting into a model cluster, coating a refractory coating, drying, and then 埋没 in dry quartz sand for vibration molding, the model is gasified under negative pressure, and the liquid metal takes the place of the model to form a casting after solidification. This method can produce castings with high precision, no need for a sand core, and has a high degree of design flexibility. However, the cost of the process may be relatively high.
10. Future Development Trends of Low-Pressure Casting
With the continuous development of science and technology, the application scope of low-pressure casting is constantly expanding. To further improve the quality and performance of low-pressure castings, several trends can be expected in the future.
Firstly, the development of advanced simulation technologies will play a crucial role. By using more accurate numerical simulation models of molten metal filling flow and solidification crystallization sequence, which are highly consistent with the actual process, it will be possible to optimize the casting process parameters in advance. This can significantly reduce the trial-and-error process in production and improve the first-pass yield of castings. For example, through computer-aided engineering (CAE) software, engineers can predict potential defects such as porosity and shrinkage cavities more precisely and take corresponding preventive measures before actual production.
Secondly, the improvement of in-situ detection capabilities for casting properties is essential. Non-destructive testing methods like ultrasonic testing for residual stress in castings and thermal analysis techniques for predicting the mechanical properties of key parts will become more advanced and widely used. This allows for real-time monitoring of the casting process and immediate feedback on the quality of the castings. In this way, any problems can be detected and corrected in a timely manner, ensuring the stability and reliability of the production process.
In addition, the research and development of new materials for low-pressure casting molds and riser tubes will also be an important direction. The development of materials with better heat resistance, corrosion resistance, and wear resistance can extend the service life of these components, reduce production costs, and improve production efficiency. For instance, the exploration of advanced ceramic materials or composite materials may bring new breakthroughs in this regard.
Moreover, the combination of low-pressure casting with other advanced manufacturing technologies will open up new possibilities. For example, integrating it with additive manufacturing techniques could enable the production of more complex and customized castings. This hybrid manufacturing approach can combine the advantages of both technologies, providing greater design freedom and better performance for the final products.
Finally, with the increasing demand for environmentally friendly manufacturing processes, the development of low-pressure casting technologies will also focus on reducing energy consumption and minimizing waste. This includes optimizing the energy utilization of the entire casting process and recycling and reusing materials as much as possible. By doing so, low-pressure casting can not only maintain its competitiveness in the manufacturing industry but also contribute to sustainable development.
In conclusion, the future of low-pressure casting is full of opportunities and challenges. Continuous innovation and improvement in technology will drive its development and expand its application in various fields, making it an important force in modern manufacturing.
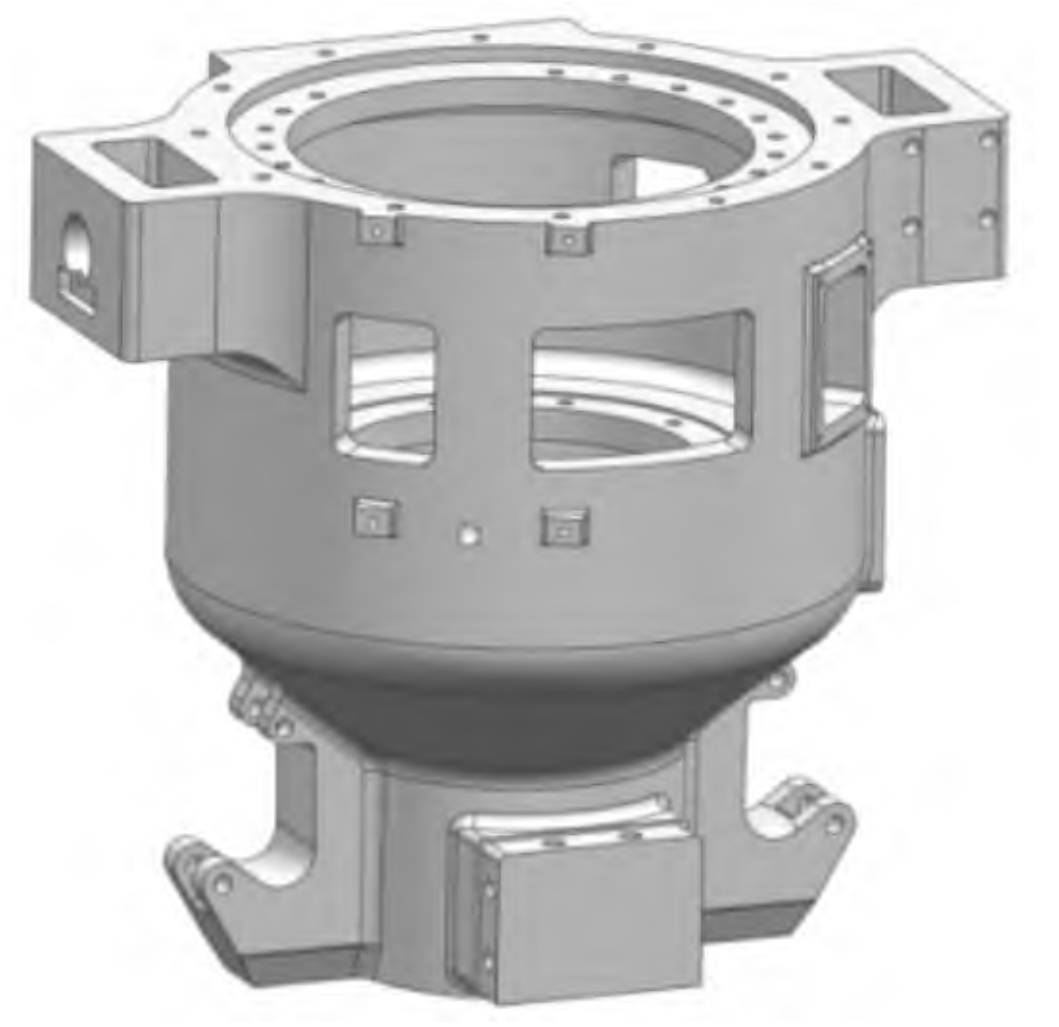