At present, most companies use sodium silicate sand mold casting and V-method casting process for production. In view of the characteristics of the production mode of broken type, the company adopts sodium silicate sand mold casting method. This kind of casting method has many characteristics, it can be concluded that it is suitable for multi variety and small batch production, especially for the complex structure of the axle housing, with low production cost and high production efficiency. The main advantages of this kind of cast steel axle housing are good strength and toughness, and high overall safety factor. However, due to its own characteristics of gravity casting, complicated design structure and strict quality requirements, the defective product rate is as high as 70%. Based on this, a tractor split axle housing is selected as a case, as shown in Figure 1 as the research object. The purpose is to carry out process analysis on the structure of the axle housing, design and calculate the casting process scheme, formulate the corresponding process parameter settings, and put forward the optimal casting process solution on the basis of process scheme optimization, simulation and optimization.
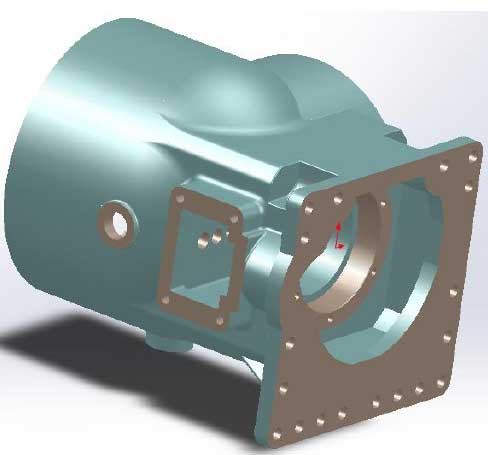
The casting process of the axle housing is complex. Under the action of gravity, the molten steel enters the specific cavity by heating and then cools down to produce the parts blank. The general casting process includes mold making and inspection, including mold, molding, melting, pouring, cleaning and other links. As a result, the product is affected by many factors, the product quality stability is poor, and the internal and external quality requirements of the axle housing are very high, resulting in three casting defects such as shrinkage cavity, lack of meat and unqualified air tightness in the process of processing and using. It is mainly reflected in the following aspects: the shrinkage cavity in the critical wall thickness position due to insufficient feeding pressure, resulting in the volume deficit of the axle housing itself, resulting in irregular shape and relatively rough hole type defects; the organization is not dense (oil leakage) and the product sealing is not good, after the assembly, there is oil leakage phenomenon in the driving process of the axle housing.
For this kind of sand casting axle housing, the above casting defects are common failures, both surface defects and internal defects. The main harm is that it can not be identified by visual inspection. The traditional detection equipment can directly and accurately detect the defect location, resulting in more quality defects and higher subsequent maintenance cost. Through the observation of the oil leakage position, the inspection results show that: the oil leakage parts are all in the depression under the oil seal seat of the axle housing, which is the wall thickness connection of the inter wheel differential, and other parts such as the axle housing connecting plate are sealed well without oil leakage. According to the preliminary judgment, the cause of oil leakage is the internal casting defects of the axle housing. According to the comprehensive review analysis, the oil leakage parts are the depression under the oil seal seat of the axle housing, and the specific position is shown in Fig. 2.
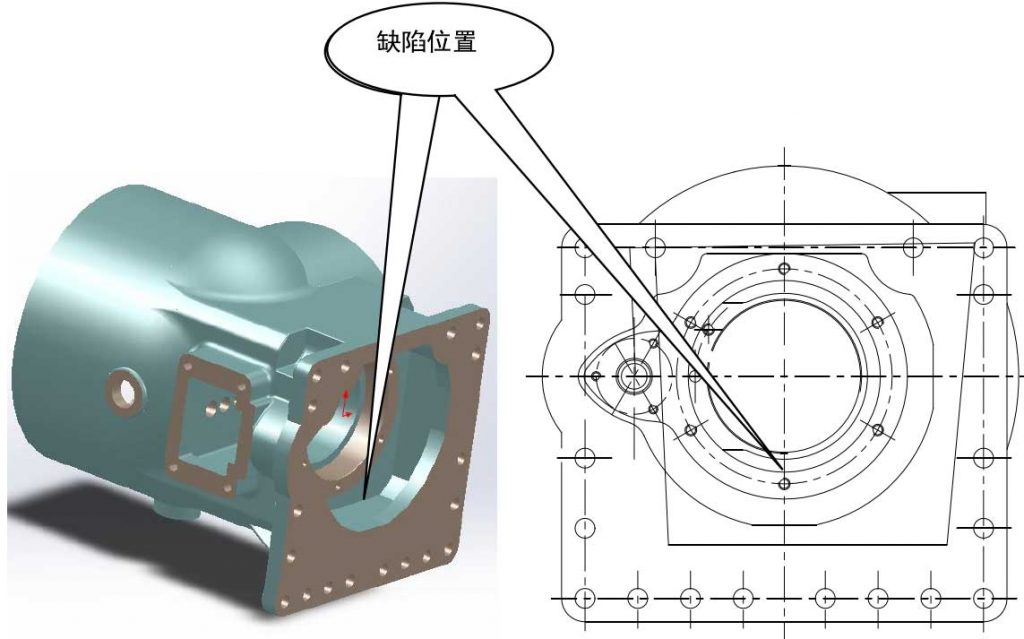