The cold iron is directly attached to the area where the riser is not suitable. Because of the chilling effect of the cold iron, the solidification speed of the axle housing where the cold iron is placed is faster than that of the adjacent section. Therefore, a “V” shaped solidification front is formed on this section. The temperature difference formed in this way is equal to the temperature difference formed in the natural end area, which is conducive to the formation of sequential solidification. It is conducive to the formation of compactness of the axle housing. Cast steel is used as cold iron in this gating system. The size of chill is about 30mm × 50mm × 60mm. It is required to remove rust and grind without oxide layer and can be used repeatedly.
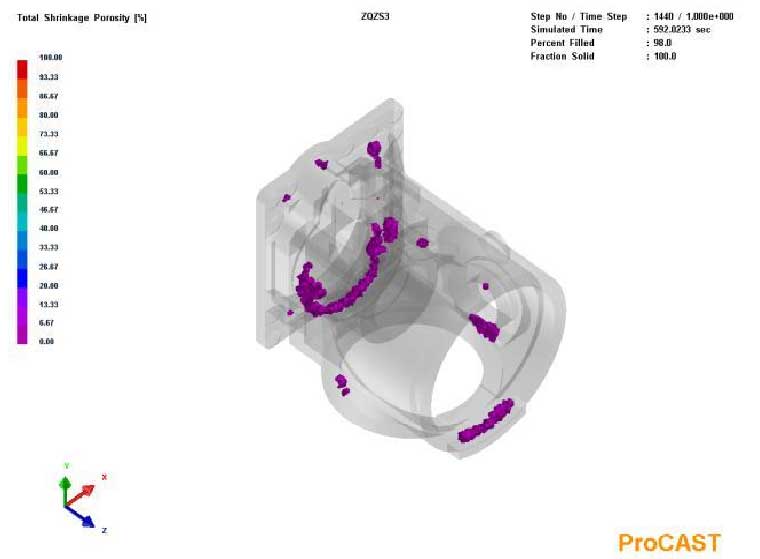
According to the results of ProCAST simulation software, shrinkage defects are easy to form in the lower part of the inner cavity of the axle housing. As shown in Figure 1, riser cannot be added here, so the cold iron is added here to form artificial temperature difference. The axle housing near the cold iron is solidified first to achieve the purpose of orderly solidification of the axle housing and eliminate the shrinkage porosity and shrinkage cavity defects here.
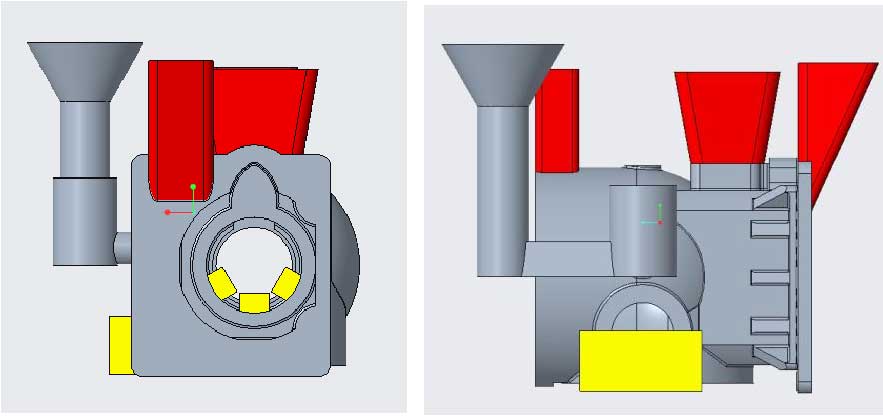
Creo three-dimensional drawing software is used to re model the axle housing with riser and cold iron. The three-dimensional structure diagram of the axle housing with riser and cold iron in scheme 1 is shown in Figure 2, and that in scheme 3 with riser and cold iron is shown in Fig. 3.
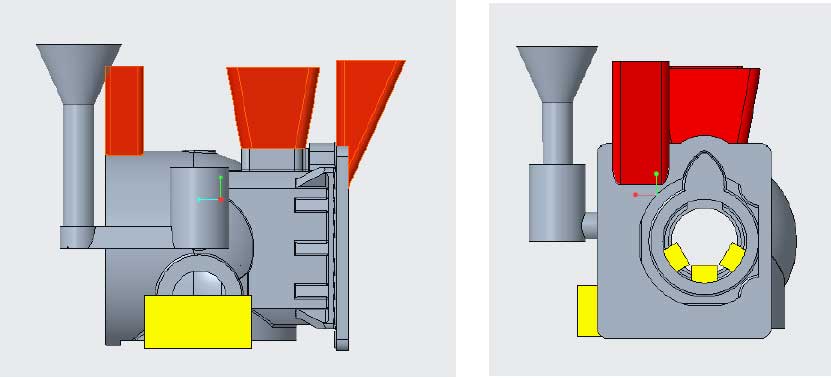