According to the 2022 data report of the (Manufacturing) Resabining Initiative, employment announcements for reshoring and foreign direct investment FDI reached a record high in 2022. Fourth-quarter announcements were even faster than expected due to chip and infrastructure legislation and deglobalization trends, the report said.
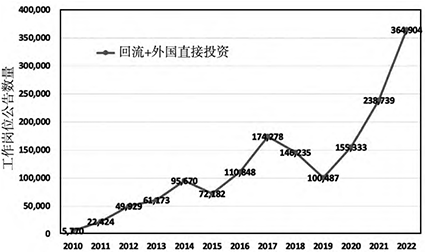
Number of job announcements since 2010 (repatriation + foreign direct investment)
The most important takeaways include:
364,000 (manufacturing) repatriation and FDI jobs were announced in 2022, up 53% from the record in 2021. Since 2010, the total number of job postings in 2022 has reached nearly 1.6 million. EV batteries make electrical equipment a top industry. With the Inflation Reduction Act, the CHIP Act, and the Infrastructure Act, the U.S. government is finally starting to warm up for industrial policy, although more comprehensive programs can be achieved at a lower cost. The IRA Act, or Inflation Reduction Act, contains $500 billion in new spending and tax breaks designed to promote clean energy, lower health care costs and increase taxes. Supply chain gaps and the need for greater self-sufficiency set the stage for the current upward trend of reshoring. The risk of conflict in the Taiwan Strait or decoupling between China and the United States is centering on these concerns. Unstable geopolitical and climatic forces have exposed our fragility and the need to address them. The White House uses the Inflation Reduction Act and the CHIP Act and the Infrastructure Act in response, for public beings interested in filling gaps
Divisions and industries provide some orientation and financial security. These government actions are necessary in the short term, but not enough, because they do not improve the cost structure of America’s lack of competitiveness. A genuine industrial policy would create equitable results through sweeping actions such as massive investment in skilled labour, a 25 per cent reduction in the dollar, and the immediate cost of preserving capital investment This Playing Field. “The current action and momentum is a good start. A real industrial policy would accelerate this trend and increase U.S. manufacturing by 40 percent (5 million jobs). Repatriation would reduce trade and budget deficits and make the United States safer, more self-reliant, and more resilient. Harry Mosser, founder and president of the Returnback Initiative, said. The American Foundry Association has long been a sponsor of the Reshoring Initiative.
American Foundry Association Casting of the Year: Cadillac casting design
By the end of 2023, Cadillac will deliver to customers for the first time the highly customized, all-electric ultra-luxury Celestiq sedan, GM’s most expensive and stylishly designed sedan ever, starting at $300,000. But the cost reduction of the main castings will be the main one for the launch of new cars
To be the key to profit.
Celestiq underbody castings are produced by a combination of collaborative engineering, proprietary materials and processes, and state-of-the-art technology. Staffed by AFS in Livonia, Michigan, Tooling International
& Equipment International TEI) produced the rear sideline of Celestiq
Rear rail underbody casting, named AFS 2023 Casting. A total of six huge castings are joined together to form the car
The entire floor of the car, which is basically the entire structure and the most critical part of the car, the two rear vertical plates are two of these six huge castings. The underbody has many parts, and hundreds of parts are connected to it, including the suspension, the battery and the entire body.
This is a newly designed, never-before-seen casting, weighing 59.5 pounds and measuring 58.5×22.5×33.3 (inches). The casting is produced using TAI’s own proprietary sand casting alloy, which was developed for high toughness (plasticity), which is a casting alloy for the automotive industry
A fundamental feature. This rear rail casting uses low-pressure precision sand casting, which combines the rail, shock tower and wheel well into a single casting, replacing many stamped parts of traditional design. The hollow box-section structure gives the casting high strength and stiffness, as are all inner cavity cores
Produced through additive manufacturing. The use of 3D printed sand cores makes the choices made to this casting, as well as its geometry, which cannot be produced by traditional tooling and process methods. By using a 3D printed sand core, these internal shape features – bosses and ribs – can be made in any desired shape inside the casting.
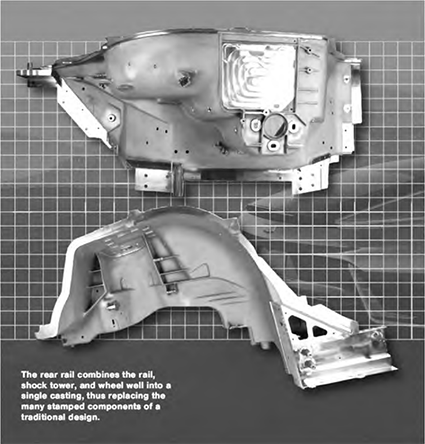
Unique and proprietary process
This rear longitudinal plate casting replaces many stamped parts in traditional designs by combining the rail, shock tower, and wheel well. 3D printing to be able to flexibly form the internal geometry of the casting, using additively manufactured cores The two ways to manufacture superior castings. One is to use them in the gating system. By placing the sand core in the fixture and then curing it with gas-cured sand during molding, the flow direction of the molten metal within the mold can be changed with a relatively simple tool. Therefore, additive manufacturing is used in processes to change the way metal flows into castings, enabling parts that are often difficult to fill.
Second, all these internal box-shaped structural parts and geometries were 3D printed, so we got a part with uniform performance, and the low-pressure sand castings produced by TEI were actually like high-pressure die castings. Another benefit of the TEI process is the high precision of the castings, in addition to the two rear longitudinal plates, TEI produces four castings to complete the entire underfloor plate. All mating surfaces between the six large castings are machined and these castings are dimensionally accurate.
Proprietary alloys
TEI recommends its own proprietary alloy for rear longitudinal plate casting. The combination
Gold has not been certified by any standards/norm committee and has been intentionally kept confidential,That means the GM team will conduct hundreds of sample tests to be sure
Ensure that it has the necessary performance. This is known as TTA (TEI tactical aluminum,
TEI tactical aluminum) alloys make parts with high elongation and more High yield strength. TTA is a low silicon content in the 300 series of alloys alloy variants, while the content of magnesium and other elements needs to be strictly controlled.What really matters in a collision is not only the stretching, but also the casting Crumpling. Therefore, when we developed this alloy The focus is not only on improving its bending resistance characteristics, but also improving its pulling characteristics Elongation under tensile conditions.
Great challenge
One of the inherent challenges of producing very large parts is how to move these huge volumes of cores, which weigh thousands of pounds, to make core components. Similarly, how to deal with large castings during heat treatment is also a problem. These castings are heated to 538 °C and then placed in 8,000 gallons of quenching medium. There must be some way to keep them straight so that they do not deform. These are the two main challenges, moving huge moulds and parts and then preventing the casting from deforming during the heat treatment process. After the heat treatment is completed, the casting is shot peening cleaned; TEI then sends the castings for 100% x-ray inspection, regardless of size, as they are safety-critical structural parts. Each part is laser scanned, the laser is aimed at the datum, and the casting is sent to a division of General Motors, where it is fully machined. The casting leaves the processing line, is coated with a chemically converted coating for passivated aluminum, and serves as the base layer for the paint.
Reduce capital investment
In the whole car, the number of parts will be reduced from 300~400 to about 100. The six underfloor castings also reduce manufacturing costs because there are few parts to be joined. Many common assembly accessory solutions have been integrated into the design to make installation easier. Phases with many stamped parts and fasteners with lengthy traditional assembly processes
Than, there are fewer parts to assemble on the assembly shop, which contributes to significant cost savings. In fact, reducing the number of underfloor parts to just six helped his customer, the assembly shop, significantly reduce capital investment on the front end.