preface
Lost foam casting is a new type of casting in which a foam model with a similar size and shape of the casting is bonded and combined into a model cluster, brushed with refractory coating, buried in dry sand after drying to vibrate the molding, poured under normal pressure or negative pressure to vaporize the model, liquid metal occupies the model position, solidifies and cools to form a new type of casting
Method. Lost foam casting consumes a foam pattern for each casting produced, which increases the process of pre-foaming and foam molding, and reduces many cumbersome processes such as mold (core) sand preparation, core making, molding, and core cutting. Engine block is usually composed of cylinder, cylinder barrel cooling water jacket, cylinder head joint surface strong screw hole, valve tappet hole, main oil channel system, oil circuit hole, oil pump hole, camshaft hole, crankshaft hole, crankcase box, oil pan flange, filter flange, flywheel shell flange, cooling water pump flange, oil cooler flange, various stiffener strips and spoke plates, etc., engine block manufacturing level reflects the development level of a country’s automobile industry, cylinder block castings belong to high-end casting products. Chengdu Castin Company has provided three cylinders for the country
Body casting manufacturers provide a full set of engine block lost foam casting production technology; It is now in normal mass production; The pass rate of one-time inspection is more than 95%.
1 Cylinder block casting features
The material of cylinder block casting is HT250 low-alloy casting, the material chemical composition control range is C (3.10% ~ 3.30%), Si (1.60% ~ 1.80%), Mn (0.60% ~ 0.75%), P (0.040% ~ 0.050%), S (0.050% ~ 0.060%), Cu (0.6% ~ 1.0%), Cr (0.3% ~ 0.5%), and the tensile strength is not less than 250 MPa; The casting is treated with internal stress relief, the hardness is 187~255 HBS, and the hardness difference is not more than 40 HBS.
2 Casting scheme and implementation
2.1 Design of cylinder block mold
At present, there are different schemes at home and abroad in the foam model structure process design of diesel engine and gasoline engine block, and the treatment of parting scheme is consistent. The processing of the parting scheme is mainly considered for the molding quality of the foam mold sheet, the ease of demolding and the overall model gluing quality The parting scheme of the engine block foam model is more consistent with cutting horizontally layer by layer, and the principle is to ensure inclusion
The mold of the exhaust duct can achieve smooth demolding in the two-opening and closing mold structure, according to several typical representatives at home and abroad The engine block lost foam process solution, combined with many years of production practice, adopts horizontal parting, and the crankcase is molded along the line The direction is carried out for partial sealing, and the parting mold is made from the outer wall of the crankcase in the local sealing part of the partial sealing part The solution is better. Figure 1 shows the parting effect of engine block castings according to this parting scheme. Under the premise that the equipment meets the requirements of the casting process, the casting molding quality of 50%~60% depends on the quality of the foam pattern, and the quality of mold production directly affects the quality of the foam mold, so the mold manufacturing technology must be selected, advanced equipment, honest and trustworthy mold manufacturer.
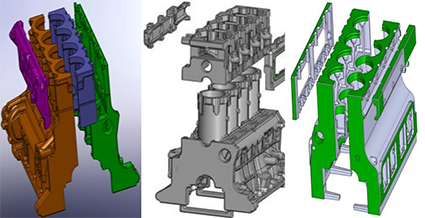
Figure 1 Parting effect of a cylinder block
2.2 Molded pre-development and maturation
At present, there are several manufacturers of expandable polystyrene beads that meet the requirements of lost foam casting in China, here according to the characteristics of engine block castings, after preliminary trials, finally choose Jiachang brand B107 model EPS material as the raw material for making foam molds, and EPS foam molds The sample density is strictly controlled in the range of 23~24 g/L. In order to achieve this pattern density requirement, it is necessary to strictly control the pre-foaming bulk density of EPS beads, which is controlled at 20~21 g/L. The EPS material can only be used after being foamed by the pre-foaming machine and matured in the curing chamber for 4~8 h.
2.3 Foam molding and maturation
Foam molding adopts hydraulic semi-automatic forming machine, optimized design mold to achieve cylinder block cylinder liner mold and crankshaft box one-time molding, which solves the problem of deformation and dimensional accuracy, and minimizes the impact of adhesive on the quality of castings. In order to reduce the residual moisture volatilization and foaming agent in the foam pattern
The adverse effects of diffusion volatilization on the casting process require the foam pattern to be naturally aged for 20 days at room temperature.
2.4 Foam pattern drying
Before assembling and bonding the complete mold, the foam pattern and the forming casting system need to be dried in a separate drying chamber under the condition of 55 °C ± 5 °C and relative humidity of less than 30% until the foam pattern and the casting system pattern are dry.
2.5 Finishing and bonding combination of foam molds
After the foam pattern is fully aged, it should be carefully trimmed to remove flash and burrs, repair damaged surfaces, smooth the mating surface, and check the finishing quality and the key geometries of the foam pattern. Fully qualified foam patterns, foam casting systems, etc. will be inspected, and cold and hot melt adhesives will be used to bond into molds
Type group. Engine block foam pattern structure is complex, currently using manual bonding method, in order to ensure sufficient operation time, cold glue is used to bond the cylinder block foam mold parting surface, the pouring system is bonded with hot melt adhesive bonding surface, the operation of glue should be uniform. Under the premise of satisfying the bonding, it is necessary to use as little glue as possible, and use double-sided tape paper to strictly seal it after the bonding is firm.
2.6 Dip coating and drying
The casting success rate of lost foam casting depends on the lost foam coating and application process. The experiment used the lost foam coating produced by Sanmenxia Sunshine Casting Co., Ltd. for the cylinder casting, and the foam mold group was dried according to the number of applications. The coating thickness is tight The grid is controlled at 1.0~1.5 mm.
2.7 Gating system
For engine cylinders with complex structures and thin walls In terms of body, the design of the gating system is particularly important. The design of the gating system should consider two factors: first, the form of the gating system; The second is the setting position of the inner sprue. The gating system for cylinder castings is closed, i.e. F transverse> F inside > F straight, this(1.3~2):(1~1.5): 1, and a set of pouring system is designed to pour 2 pieces of cylinder castings, and the pouring time is controlled at 35~40 s. The internal sprue position design of the cylinder block casting is very important, and the internal sprue scheme with multi-point water inlet is adopted, as shown in Figure 2.

2.8 Styling
The shape of the cylinder block casting is made of dry sand of 40~70 purposes. For the foam type of the box, the coating should be carefully and carefully inspected before packing, and the fine cracks found must be repaired with quick-drying paint, and the model must be checked for deformation, and if there is deformation, it must be returned. It adopts a five-pump negative pressure special sand box, and four foam models are buried in each box. The shaking table adopts air bag frequency modulation lock to lock the shaking table, add bottom sand after the sand box is locked, 120 mm thick, after the shock, scrape out the inclination angle and then place the foam model, the model should be placed as close to the box side as possible to facilitate the pouring operation. Sand filling is carried out in two parts, the first time the height of sand filling is level or slightly higher than the end of the cylinder block. Adjust the appropriate frequency vibration, and the vibration time can be controlled at 10~20 s. The second sand filling uses cover sand, and the covering sand should have sufficient thickness to ensure sufficient sand eating and prevent the box from rising. The gating system of the cylinder casting has been determined, and the sand filling height is 15 mm lower than the end face of the gate cup after shocking. After the molding sand is compacted, the sand surface should be scraped flat, and it should not be hilly. The plastic film is covered by the landfill personnel, and protective sand should be added after the film is covered, and the protective sand layer thickness > 20 mm should also be scraped flat. The gate cup should be fully exposed. In the process of burying the box, the buried personnel should operate according to the process requirements. The buried sand box should be inserted and hung according to the process requirements and moved to the pouring station.
2.9 Pouring and cooling of falling sand
The pouring personnel should check whether the protective sand layer has sufficient thickness, whether the position of the gate cup is suitable, whether the position is aligned, whether the vacuum pump is running normally, whether the negative pressure is stable, the pouring bag is selected from the teapot bag, and the pouring bag is baked dark red before it can be used. Training and certification of pouring personnel and overhead crane operators On the post, the pouring person is responsible. Before pouring molten iron, the pouring bale must be lowered to the optimal height and position, and the pouring nozzle is as close as possible to the pouring cup, so that the first drop of molten iron can be accurately poured to the center of the pouring cup. When starting to pour, first use a small flow test pouring, wait for the gate cup to burn out black smoke, hear the molten iron water absorption sound after increasing the flow, after the water absorption sound is reduced, the experience judgment is almost full, control the flow in advance, from large flow to small flow, so that the gate cup is full and does not overflow. The 1.5 ton medium frequency electric furnace is used as the pouring equipment, and the pouring vacuum is controlled at -0.035~-0.040 MPa. The pouring temperature requires the furnace temperature to be controlled at 1600~1620 °C, and the current on-site pouring situation is 4 boxes per package of molten iron, four cylinders per box, and the final pouring temperature of the cylinder castings should be 1480 °C, the casting is cooled in a sand box for 1.5 h before falling sand. Fig. 3 is a cleaned cylinder block casting.
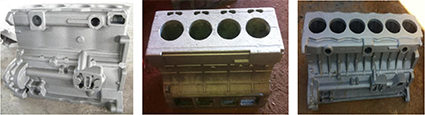
Fig. 3 Cleared cylinder block castings
2.10 Implementation Results
The yield of engine block castings produced by the lost foam casting process is 95%, the processing qualification rate of cylinder block castings that pass the inspection is 99%, and the process yield of castings is as high as 91%, as shown in Figure 4.
3 Conclusion
(1) Through the optimization design of the mold slicing process and the actual verification of production, the structural characteristics of the cylinder casting are analyzed, different mold structures are adopted for different structure cylinder blocks, and some process problems of lost foam casting are solved through the optimized design of the mold sheet.
(2) Casting technicians must conduct process analysis. The lost foam casting process in the local part of the casting cannot be satisfied, and other casting process means can be used to make up for the process to ensure that the technical parameters of the casting process meet the requirements of the lost foam casting process.