1. Introduction
Casting titanium alloy is an excellent casting structural material with small specific gravity, high strength, high and low temperature mechanical properties, and high corrosion resistance. It is widely used in the manufacturing of key components of aerospace engines and aircraft fuselage structures. ZTC4 is a commonly used titanium alloy in modern aircraft and engine structures. However, during the casting process of ZTC4 titanium alloy, various defects such as pores, inclusions, and cracks may occur, and depressions that require repair welding may also appear after hot isostatic pressing. In addition, the welding of castings in aircraft and engines often involves the welding with other castings or forging parts. Therefore, it is of great engineering significance and clear demand background to study the repair welding technology of casting defects for ZTC4 titanium alloy.
The main technical difficulty in the repair welding of large thin-walled titanium alloy castings is the formation of large stress concentration in the heat-affected zone after welding, resulting in cracks around the repair welded joint. This problem is affected by welding heat cycle, composition of welding filler material, joint form, welding restraint state, pre-welding base metal state, and post-welding heat treatment system. In this paper, aiming at the welding technical requirements of ZTC4 titanium alloy integrally precision-cast intermediate casings of a certain thrust-to-weight ratio engine prototype and a large aircraft engine in China, the weldability of casting materials and the influence law of the number of repair weldings on the performance of welded joints are studied through multiple repair welding tests of test pieces. The effects of pre-welding preparation and welding process on weld quality are studied through the appearance inspection of weld formation and non-destructive testing inside the weld. The effects of welding specification parameters and post-welding heat treatment system on the structure and performance of welded joints are studied through joint structure analysis and performance testing. The change of welding residual stress before and after repair welding of casting titanium alloy is studied through X-ray analysis. Finally, a suitable repair welding process for titanium alloy castings is formed.
2. Research Process and Methods
2.1 Materials
The base metal selected in this study is ZTC4 cast titanium alloy plate, in the state of casting + hot isostatic pressing. The welding materials are as follows: for automatic argon arc welding, φ1.6TC4 welding wire is used; for manual argon arc welding, low-hydrogen φ1.0TC4 welding wire is used; and for laser welding, TC4 powder with a particle size of 150 – 325 mesh is used.
2.2 Repair Welding Test Methods
2.2.1 Influence of Repair Welding Times on Joint Performance
The ZTC4 automatic argon arc welding repair method is used to study the influence of repair welding times on the performance of repair welded joints. 6mm thick ZTC4 titanium alloy plates are selected to study the influence law of repair welding times on joint performance. The repair welding scheme is designed as follows: first, two 6mm thick plates are butt welded, and then a V-shaped groove with a depth of 3mm – 4mm is machined on the weld for repair welding. Then, the weld is machined and repaired twice according to the above steps. By analogy, a total of 4 repair weldings are carried out to obtain test plates in 5 states: un-repaired, 1-time repaired, 2-time repaired, 3-time repaired, and 4-time repaired. The 5 test plates are subjected to post-weld heat treatment with a regime of 730°C × 2h in vacuum. Finally, the room temperature tensile and room temperature impact properties of the 5 states of test plates are tested to obtain the influence law of repair welding times on joint performance.
2.2.2 Influence of Preheating and Post-weld Heat Treatment on Joint Performance
The ZTC4 manual argon arc welding repair method is used to study the influence of preheating and post-weld heat treatment on the performance of repair welded joints. Two thicknesses of plates, 3mm and 6mm, are selected according to the defect situation of the actual workpiece to study the influence of preheating and post-weld heat treatment on the residual stress and performance of the joint. The joint forms of the two thicknesses of plates are as follows: the 3mm thick test plate is a conical hole of φ8 × 2.5, which is used for the room temperature tensile property test; the 6mm thick test plate is a conical hole of φ11 × 5.5, which is used for the room temperature impact and joint residual stress test. A welding preheating fixture is designed and fabricated to heat before and during welding. The preheating temperature is 150°C ± 10°C. The ZTC4 manual argon arc welding process is optimized, and the two thicknesses of plates are repaired with the optimized process to obtain 4 states of repaired plates: welding, preheating welding, welding + post-weld heat treatment, and preheating welding + post-weld heat treatment. The residual stress of the joint is tested by the X-ray method, and the room temperature tensile and room temperature impact properties of the joint are tested to obtain the influence law of preheating and post-weld heat treatment on the residual stress and mechanical properties of the joint.
2.2.3 Research on Preheating and Post-weld Heat Treatment before Repair Welding
In view of the welding crack and deformation problems, the preheating and post-weld heat treatment before repair welding of ZTC4 titanium alloy plates are studied. A welding preheating fixture is designed and fabricated as shown in Figure 2. This fixture can keep the temperature of the test plate constant during the repair welding process to ensure the preheating effect. The preheating temperature is determined to be 150°C ± 10°C, and the post-weld heat treatment regime is 730°C × 2h in vacuum. To prevent the appearance of post-weld delayed cracks, the selected φ1.0 TC4 welding wire is vacuum dehydrogenated before welding. The manual argon arc welding process parameters are shown in Table 1. The manual argon arc welding of two specifications of plates is carried out with these parameters, and the repair welded joint sample is shown in Figure 3.
3. Results and Discussion
3.1 Influence of Repair Welding Times on ZTC Joint Performance
The automatic argon arc welding repair process of 6mm thick ZTC4 titanium alloy plates is studied, and the influence of repair welding times (0 – 4 times) on joint performance is investigated. φ1.6TC4 wire is selected as the argon arc welding repair welding wire for ZTC4 titanium alloy plates, and the repair welding process for 6mm thick ZTC4 titanium alloy is determined as follows: no preheating before welding, and the parameters are shown in Table 2.
The room temperature properties of the joint after welding are tested. The room temperature tensile and impact properties of ZTC4 base metal are shown in Tables 3 and 4, and the room temperature tensile and impact properties of the joint under different repair welding times are shown in Figures 4 and 5. It can be seen that the tensile strength of the joint under different repair welding times reaches more than 98% or even 100% of the base metal, the elongation is lower than that of the base metal, about 70% – 80% of the base metal, and the room temperature impact toughness exceeds that of the base metal. Moreover, the strengths among them are basically the same. Therefore, it can be concluded that the repair welding times have little effect on the room temperature tensile and impact properties of the TC4 titanium alloy joint.
3.2 Influence of Preheating and Post-weld Heat Treatment on ZTC4 Plate Manual Argon Arc Welding
The joint properties of preheating and not preheating before welding and post-weld heat treatment and not post-weld heat treatment are compared. The joint structures in four states of not preheating welding, preheating welding, not preheating welding + post-weld heat treatment, and preheating welding + post-weld heat treatment are analyzed. The metallographic macro photos of different states are shown in Figure 6, and the weld structure photos of different states are shown in Figure 7. The room temperature impact and tensile property test results are shown in Figures 8 and 9.
It can be seen that the room temperature tensile strength in the four states reaches 97% or even 100% of the base metal. The joint strength slightly decreases after heat treatment, and the joint strength significantly increases after preheating welding + heat treatment. The elongation of the preheating welding joint is relatively low compared with other states, about 61% of the base metal, and the fracture basically occurs in the base metal as shown in Figure 10. The joint specimens in five states for residual stress testing are shown in Figure 11, and the distribution of residual stress testing points is shown in Figure 12. The measurement directions of each point are shown in Table 5.
The test results are shown in Table 6. It can be seen from Table 6 that the base metal is basically in a compressive stress state. After welding, tensile stress points appear in both X and Y directions, and a large tensile stress of 784MPa appears at the joint between the weld and the base metal, which is the main cause of repair welding cracking. After preheating welding, all points in the Y direction are compressive stresses, and the tensile stress value in the X direction is also significantly smaller than that without preheating welding. After post-weld heat treatment, all test points are basically compressive stresses, and the tensile stress values of individual points are also significantly smaller. Therefore, it can be concluded that welding preheating and post-weld heat treatment can effectively reduce welding stress and prevent the occurrence of repair welding cracks.
4. Conclusion
(1) Using the automatic argon arc welding method, four repair welding tests are carried out on the ZTC4 test plate, and it is concluded that the room temperature tensile and impact properties of the joint change little within the range of four repair weldings.
(2) Using the manual argon arc welding method, the residual stress, room temperature tensile and impact properties of the joints in four states of welding, preheating welding, welding + heat treatment, and preheating welding + heat treatment are analyzed. It is concluded that the stress state of the base metal is basically compressive stress, and the joints in the welded state are all tensile stress, which is the reason for the easy occurrence of cracks after welding. After preheating welding, the stress in the Y direction is converted to compressive stress, and the individual tensile stress in the X direction is also reduced compared with the welded state. After post-weld heat treatment, the stress of the joint is basically compressive stress, and the individual tensile stress value is also significantly reduced compared with that before treatment. Therefore, welding preheating and post-weld heat treatment can effectively reduce welding stress and prevent the occurrence of repair welding cracks.
(3) The room temperature tensile property of the argon arc welding repair joint reaches more than 97% of the base metal, and the impact toughness reaches 100% of the base metal.
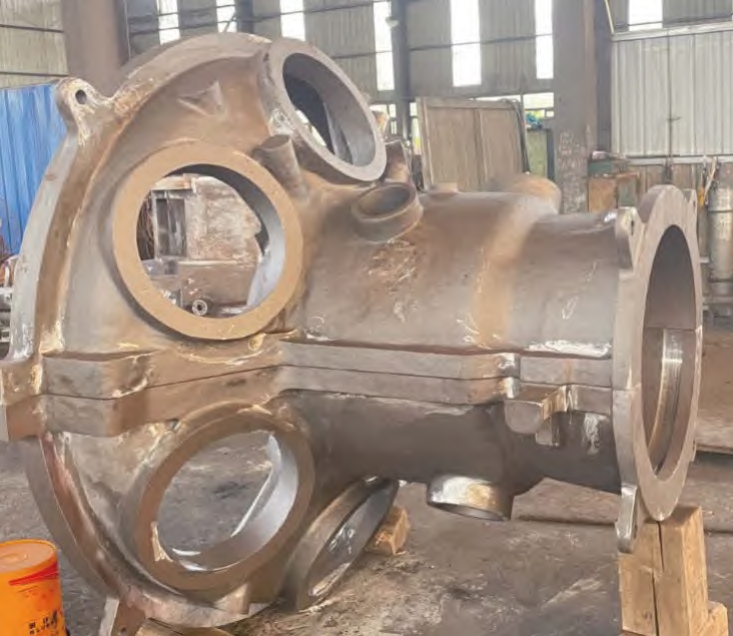